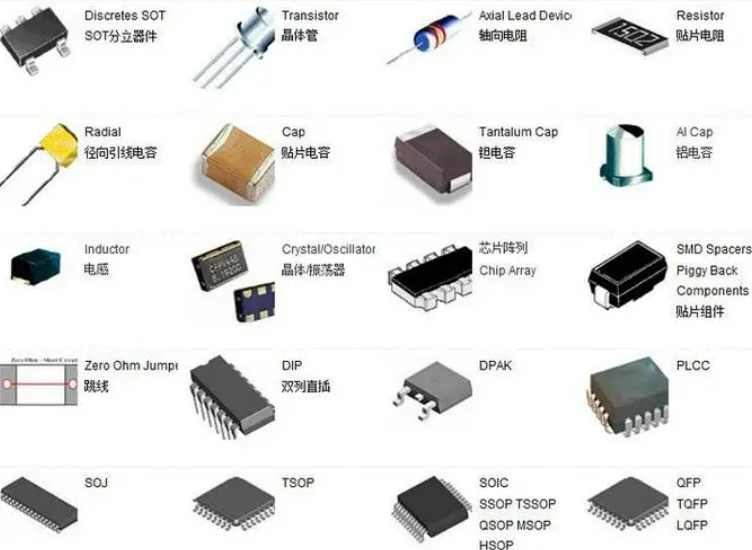
The basic factors affecting the electroplating process of PCB manufacturing
The output value of the global electroplating PCB industry accounts for the proportion of the total output value of the electronic components industry growing rapidly. It is the largest industry in the subdivided industry of electronic components, occupying a unique position. The annual output value of electroplating PCB is $60 billion. The volume of electronic products is becoming thinner and shorter. Direct stacking of blind holes is a design method to obtain high density interconnection. To do a good job of stacking holes, the flatness of the bottom of the hole should be done first. There are several typical flat hole surface production methods, electroplating hole filling process is one of the representative.
In addition to reducing the need for additional process development, the electroplating hole filling process is compatible with existing process equipment, which is conducive to obtaining good reliability.
Electroplating hole filling has the following advantages:
(1) Conducive to the design of Stacked holes (Via.on.Pad) and holes on the plate;
(2) Improve electrical performance, conducive to high-frequency design;
(3) help heat dissipation;
(4) the plug hole and electrical interconnection are completed in one step;
(5) The blind hole is filled with copper plating, which has higher reliability and better conductive property than conductive glue.
1. Chemical influencing factors
1.1 Inorganic chemical composition
Inorganic chemical components include copper (Cu) ions, sulfuric acid and chloride.
(1) copper sulfate. Copper sulfate is the main source of copper ions in plating solution. The concentration of copper ions in plating solution remained constant through coulomb equilibrium between cathode and anode. Usually the anode material is the same as the coating material, where copper is both the anode and the ion source. Of course, the anode can also be used insoluble anode, Cu2+ by the way of dissolution outside the tank, such as the use of pure copper Angle, CuO powder, CuCO, etc. However, it should be noted that the way of adding outside the tank is easy to mix with air bubbles, so that Cu2 is in a critical state of supersaturation in the low current area and is not easy to precipitate. It is worth noting that increasing copper ion concentration has a negative effect on through-hole dispersion.
(2) Sulfuric acid. Sulfuric acid is used to enhance the conductivity of the plating solution. Increasing the concentration of sulfuric acid can reduce the resistance of the bath and improve the plating efficiency.
However, if the concentration of sulfuric acid increases in the process of filling holes electroplating, it will affect the filling of copper ions, resulting in poor filling holes. Low sulfuric acid concentration system is usually used to obtain better filling effect.
(3) cupric acid ratio. The traditional high acid and low copper (C+ : C: +=8-13) system is suitable for through hole electroplating, and the electroplating holes should be filled with low acid and high copper
(C+ : Cz=3-10) bath system. This is because in order to obtain a good filling effect, the plating rate in the micro-through hole should be greater than the plating rate on the surface of the substrate. In this case, compared with the traditional plating solution in the through hole, the solution formula is changed from high acid and low copper to low acid and high copper, ensuring the supply of copper ions in the depression without worries.
(4) chloride ion. The main function of chloride ion is to form a stable electron transfer bridge between copper ion and metal copper.
In the process of electroplating, chloride ions in the anode can help to dissolve and bite the phosphorus copper ball uniformly, forming a layer of uniform anode film on the anode surface. At the cathode, the synergistic action with the inhibitor allows stable deposition of copper ions, reducing polarization and making the coating fine.
In addition, the conventional chloride ion analysis is carried out in the ultraviolet visible spectrophotometer, and because of the strict requirements on the chloride ion concentration of electroplating bath, and copper sulfate bath blue, the measurement of the spectrophotometer is very important, so should consider the use of automatic potential titration analysis.
2. Organic additive
The use of organic additives can make the copper grain fine, improve the dispersion ability, make the coating bright and smooth. There are three types of additives in acidic copper plating solution: Carrier, Leveler and Brightener.
(1) Transport agent. The carrier is a combination of polyalcohols of high polymers.
The carrier is adsorbed on the cathode surface and acts together with chloride ions to inhibit the plating rate, reducing the difference between the high and low current zones (i.e. increasing the polarization resistance), so that the copper plating can be uniformly and continuously deposited. The inhibitor also acts as a wetting agent, reducing the surface tension at the interface (reducing the contact Angle), allowing the bath to enter the pore more easily and increasing the mass transfer effect. Copper layers can also be uniformly deposited by inhibitors in porous electroplating.
(2) leveling agent. Leveling agent is usually nitrogen-containing organic matter, the main function is adsorbed in high current density area (convex area or corner), so that the plating speed slows down but does not affect the plating of low current density area (sag area), so as to flatten the surface, is a necessary additive in plating. Generally, the plating with high copper and low acid system will make the coating rough. The research shows that the addition of leveling agent can effectively improve the poor coating.
(3) brightener. Brightener is usually full of sulfur-containing organic matter, the main role in electroplating is to help copper ions accelerate reduction at the cathode, while forming new copper-plated crystal nuclei (reduce surface diffusion deposition energy), so that the copper layer structure becomes more detailed. Another role of brightener in hole filling plating is that if there is more brightener distribution ratio in the hole, it can help the copper plating in the blind hole deposition quickly. For laser blind hole filling electroplating, the three additives are all used, and the amount of leveling agent should be increased appropriately, so that the higher current area on the board, the formation of leveling agent and Cuz competition situation, prevent