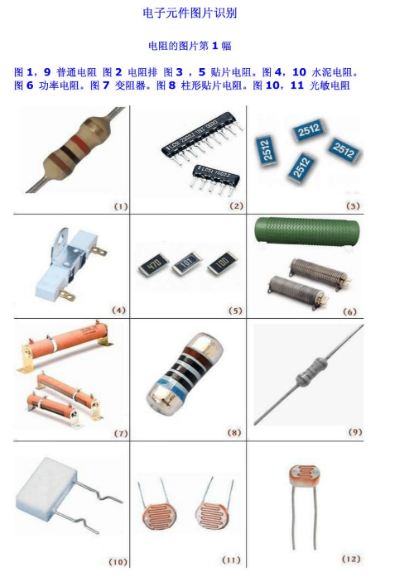
Warm tip: The size of the positioning hole should not be too large or too small. It is appropriate to make the needle not fall off after insertion, not shake, and a little tight when insertion, otherwise the positioning is inaccurate. As shown below:
And it is suggested that the space should be set aside within a certain range around the BGA to place the device, so as to be able to put the screen scraping paste when repairing.
14. About the color of PCB board: it is recommended not to make it red. Because the red circuit board is white under the red light source of the camera of the patch machine, it cannot be programmed and is not convenient for the welding of the patch machine.
15, about large devices below the small devices: some people like the small devices in the same layer of large devices, such as: digital tube under the resistance, as shown below:
This layout will cause difficulties to repair, repair must be removed first, and may cause damage to the digital tube. It is recommended to drain the resistance under the digital tube to the Bottom surface, as shown in the figure below:
16, about the impact of copper coating and welding plate connected to molten tin: because the copper coating will absorb a lot of heat, resulting in solder is difficult to fully melt, thus forming virtual welding. As shown in the picture:
The device pad is directly connected with the copper coating; Although the 50Pins connector in FIG. b is not directly connected with the copper coating, the solder paste in FIG. a and b cannot be fully melted because the copper coating absorbs a lot of heat because the middle two layers of the four layers are covered with copper. The body of 50Pins connector in Figure b is a plastic that is not high temperature resistant. If the temperature is set high, the connector will melt or deform. If the temperature is set low, the copper coating will absorb a lot of heat, resulting in the solder paste cannot be fully melted. Therefore, it is recommended that the pad be isolated from large area copper coating. As shown in the picture:
17. Suggestions on the board and adding process:
Iii. Summary
Nowadays, more and more engineers can draw, wire and design PCB with software. However, once the design is completed, the welding efficiency can be improved. The author believes that the above factors need to be paid attention to. And cultivate good drawing habits, good communication with the processing plant, is every engineer to consider.
PCB through hole (via) process is the core of quality control, but also accounts for about 30 to 40 percent of the entire PCB manufacturing cost, because it has a pivotal position. Using scientific and standard via process flow and drilling equipment, and equipped with professional inspection procedures is the basis to ensure the quality of PCB circuit board via hole.
1. Basic concepts of via through holes
via through hole is a circular aperture through the circuit board, according to its role can be divided into signal through hole, power/ground through hole, heat dissipation hole, among which the signal through hole is the most common. Signal through hole (via) is mainly used for electrical connection between PCB layers and positioning of components. In terms of process classification, signal through holes (via) are further divided into blind via, buried via and through via.
2. via perforation process
PCB via holes must be completed with the help of professional drilling RIGS, such as Hitachi, Schmoll, Timax and other brands. The PCB substrate is fixed on the drilling machine, and the drill bit meeting the aperture requirements is assembled. The drilling process can be completed by inputting the drilling coordinate program in the PCB file on the drilling machine and adjusting the corresponding drilling speed. In the via process, drilling accuracy, position deviation and bit fracture must be monitored in real time, and problems can be solved in time.
3. pcb drilling machine via drilling equipment
Drilling machine is the most important equipment for via perforation. There are many styles and functions in the market. PCB factory selection can be evaluated based on the following factors:
A. Number of shafts: directly related to output
B. Effective drill plate size
C. Drilling machine surface: select the material with small vibration and good strength.
D. Spindle
E. Drilling disc: automatic change of bit and bit number
F. Pressure foot
G. X, Y and Z axis drive and size: accuracy, X and Y move independently
H. Dust collection system: equipped with pressure foot, good chip removal, and cooling bit function
I. Ability to Step Drill
J. Broken needle detection
K. RUN OUT
4. Process notes for via through holes
In through hole via process, the following faults often occur, and operators and technicians need to have rich problem identification and solution capabilities.
A. Broken cobalt nozzle
B. Hole damage
C. Hole offset and mismatch
D. Through hole size distortion
E. Leaking borehole
F. The Cape
G. The hole is not drilled through
H. Curly debris appears on the panel
I. The hole is blocked
PCB hole via process is one of the most critical links in the whole process of PCB manufacturers, which determines PCB quality and electrical connection performance, and is also an important node for batch scrapping or rework. Therefore, every PCB factory will establish a strong and perfect mechanism from the process documents, personnel control, inspection procedures and other aspects, in order to ensure the good operation of batch PCB production.