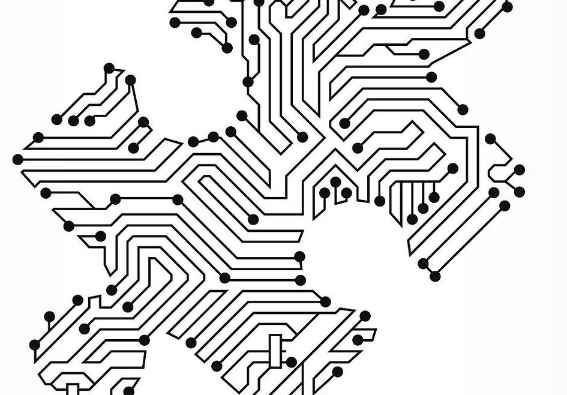
The physical parameters to be studied are: anode type, anode and cathode distance, current density, agitation, temperature, rectifier and waveform.
(1) Anode type. When it comes to anode types, it is nothing more than soluble anode and insoluble anode. Soluble anode is usually copper ball containing phosphorus, which is easy to produce anode mud, pollute the bath and affect the bath performance. Insoluble anodes, also known as inert anodes, typically consist of a titanium mesh coated with a mixture of tantalum and zirconium oxides. Insoluble anode, good stability, no need for anode maintenance, no anode mud generation, pulse or DC plating are applicable; However, the additive consumption is larger.
(2) the distance between anode and cathode. The spacing between cathode and anode is very important in electroplating process, and the design of different types of equipment is not the same. However, it is important to point out that no matter how you design it, it should not violate Faraday's law.
(3) Stir. There are many kinds of agitation, including mechanical shaking, electric vibration, gas vibration, air agitation, Eductor, etc.
For electroplating hole filling, it is generally inclined to add jet design based on the configuration of traditional copper cylinder. However, whether it is the bottom jet or the side jet, how to layout the jet pipe and air mixing pipe in the cylinder; What is the emission rate per hour; How much distance between jet tube and cathode; If the side jet is used, whether the jet is in front of or behind the anode; If the bottom jet is used, whether it will cause uneven mixing, plating solution mixing weak strong; The quantity, distance and Angle of the jet on the jet pipe are all factors that have to be considered in the design of the copper cylinder, and a lot of tests should be carried out.
In addition, the most ideal way is to connect each jet pipe to the flow meter, so as to achieve the purpose of monitoring the flow rate. Because of the large emission flow, the solution is easy to heat, so temperature control is also important.
(4) Current density and temperature. Low current density and low temperature can reduce the deposition rate of copper on the surface while providing enough Cu2 and brightener into the hole. Under this condition, the filling capacity is enhanced, but the plating efficiency is also reduced.
(5) rectifier. Rectifier is an important link in electroplating process. At present, the research of electroplating hole filling is mostly limited to full plate electroplating. If the graphic electroplating hole filling is considered, the cathode area will become very small. At this time, the output accuracy of the rectifier is very high.
The output accuracy of the rectifier should be selected according to the product line and hole size. The finer the line and the smaller the hole, the higher the accuracy of the rectifier should be. Usually the rectifier with an output accuracy of less than 5% should be selected. High accuracy of rectifier will increase the investment of equipment. The rectifier output cable wiring, first of all should be placed on the edge of the plating tank as far as possible, so as to reduce the length of the output cable, reduce the pulse current rise time. The rectifier output cable specification should be selected to meet the line voltage drop of the output cable within 0.6V at 80% of the maximum output current. The required cable cross-sectional area is usually calculated in terms of the carrying capacity of 2.5 A/mm. If the cross-sectional area of the cable is too small or the cable length is too long or the line voltage drop is too large, the transmission current cannot reach the current value required for production.
For the plating tank wider than 1.6m, the method of two-sided feeding should be considered, and the length of the two-sided cable should be equal. In this way, the bilateral current error can be controlled within a certain range. Each side of the flying bar of the plating tank shall be connected with a rectifier, so that the current of the two sides of the piece can be adjusted respectively.
(6) Waveform. At present, from the point of view of waveform, there are pulse electroplating and DC electroplating. These two electroplating filling methods have been studied. Dc electroplating hole filling using the traditional rectifier, easy to operate, but if the board is thick, there is nothing to do. Pulse electroplating hole filling using PPR rectifier, the operation steps are many, but the processing ability of thicker in the plate is strong.
4. The influence of substrate
The influence of substrate on electroplating hole filling can not be ignored, generally have dielectric layer material, hole shape, thickness to diameter ratio, chemical copper coating and other factors.
(1) dielectric layer material. The material of dielectric layer has influence on the hole filling. Compared with glass fiber reinforced materials, non-glass reinforced materials are easier to fill holes. It is worth noting that the glass fiber protrusion in the pore has an adverse effect on the chemical copper. In this case, the difficulty of electroplating hole filling is to improve the adhesion of the seed layer of chemical coating, rather than the process itself.
In fact, plating holes on glass fiber reinforced substrates has been used in practical production.
(2) thickness to diameter ratio. At present, both manufacturers and developers attach great importance to the filling technology for holes of different shapes and sizes. The capacity of filling holes is greatly affected by the ratio of hole thickness to diameter. Relatively speaking, PCB systems are used more in business. In production, the size range of the hole will be narrower, generally 80pm ~ 120Bm in diameter, 40Bm~8OBm in depth, thickness to diameter ratio not more than 1:1.
(3) electroless copper plating layer. The thickness, uniformity and placement time after electroless copper plating all affect the filling performance. Chemical copper is too thin or uneven thickness, its hole filling effect is poor. In general, chemical copper thickness is recommended. The holes were filled at 0.3pm. In addition, the oxidation of chemical copper also has a negative effect on the filling effect