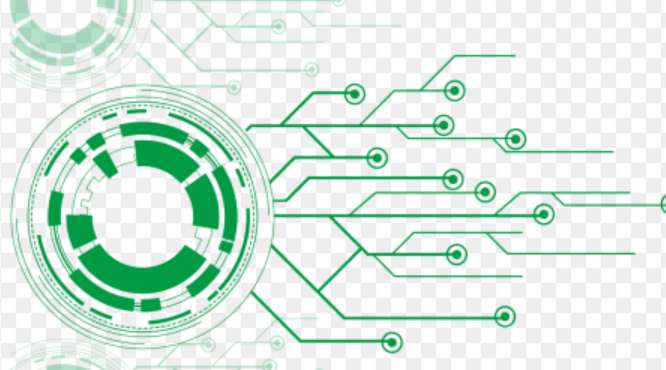
Do you know that copper coating is an important part of PCB design?
The so-called copper coating, is to use the idle space on the PCB as the base level, and then fill with solid copper, these copper areas are also known as copper filling.
The significance of copper coating is: reduce ground impedance, improve anti-interference ability; Reduce voltage drop, improve power efficiency; Connected with the ground wire, it can also reduce the area of the loop.
There are generally two basic ways to cover copper, that is, large area of copper (solid copper) and grid copper, that is a large area of copper or grid covered copper is good? It's not good to generalize, they all have advantages and disadvantages.
1. Advantages of solid copper coating: It has the dual role of increasing current and shielding. Disadvantages: If over wave soldering, the board may tilt up, and even blister. Solution: Generally, several slots will be opened to relieve copper foil foaming.
2, grid covered with copper advantages: from the point of view of heat dissipation, grid has advantages (it reduces the heating surface of copper) and plays a certain role of electromagnetic shielding. Disadvantages: simple grid copper is mainly shielding effect, increase the role of current is reduced.
Advantages and disadvantages of copper coating
Benefit: Provide extra shielding protection and noise suppression for inner signals. Improve the heat dissipation capacity of PCB. In PCB production process, save the amount of caustic agent.
Avoid PCB warping deformation due to copper foil imbalance caused by different stress during reflow welding.
Con: The outer coppered plane will be fragmented by the surface components and signal wires. If there is poorly grounded copper foil (especially that thin long broken copper), it will become an antenna, resulting in EMI problems.
If the pin of the component is fully connected with copper, heat loss will be too fast, resulting in diswelding and repair welding difficulties. The outer copper-covered plane must be well grounded. It needs to be connected with the main ground plane through more holes. If more holes are played, it is bound to affect the wiring channel, unless the buried blind holes are used.
Precautions for copper coating
When coating copper, engineers need to pay attention to the following aspects in order to achieve the desired effect:
1, if the PCB is more, have SGND, AGND, GND, etc., will be depending on the position of PCB board face, respectively to the main "to" independent copper clad as reference point, to digital and analog to separate copper from a few words, at the same time before the copper clad, first of all, bold corresponding power cords: 5.0V, 3.3V and so on. In this way, multiple deformation structures of different shapes are formed.
2, for different single point connection, the practice is through 0 ohm resistance or magnetic beads or inductance connection.
3. The crystal oscillator near the copper coating, the crystal oscillator in the circuit is a high-frequency emission source, the practice is to surround the crystal oscillator with copper coating, and then the crystal oscillator shell is grounded
4, the island (dead zone) problem, if you think it is very big, it will not take much to define a hole to add it.
5, at the beginning of wiring, the ground should be treated the same, when the wire should be good, can not rely on the copper coating by adding holes to eliminate the pin for the connection, the effect is very bad.
6. It is best not to have sharp corners on the board. =180 degrees), because electromagnetically speaking, this constitutes a transmitting antenna! For others there will always be an impact is just big or small, it is recommended to use the edge of the arc along.
7, multi-layer wiring empty area, do not cover copper. Because it's hard to make the copper "well grounded."
8. The metal inside the equipment, such as metal radiator and metal reinforcement bar, must be "well grounded".
Conclusion: Copper coating on PCB, if the grounding problem is handled well, is "more advantages than disadvantages", it can reduce the signal line backflow area, reduce the signal external electromagnetic interference.