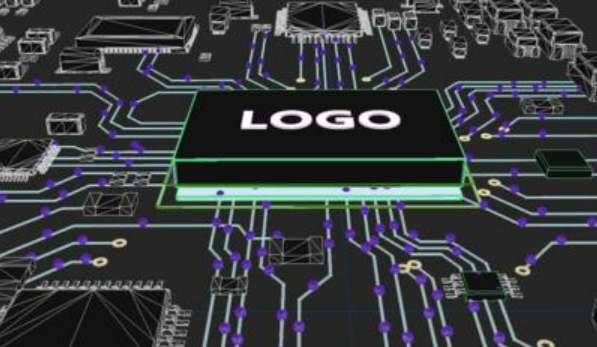
A sudden outbreak of the virus has a significant impact on the fluctuations of the global industrial chain. In the auto industry, for example, Hyundai Motor has had to stop production in China because its domestic cable and connector makers did not resume work, running out of inventory.
In addition to illustrating how interconnected global supply chains are, the non-accident also exposed a blind spot in Hyundai's design thinking. Related information shows that modern automobile in order to save the "physical consumption" of car cables, to meet the needs of lightweight cars, a large number of customized a bunch of non-standard cables, resulting in the production line of the cable versatility is very low, once a model inventory is used up, the relevant car type no cable available, the production line can only shut down and other materials.
This may sound like a myth to an industry that has been pushing its key components into general Motors, but Hyundai has done just that.
But this incident reminds me of something else that has nothing to do with Hyundai, but is very relevant to the future direction of the entire auto industry. Because that matter is related to Tesla, now everyone knows that Tesla's position in the automobile industry is similar to Apple's position in the smart phone industry. Many of its design concepts and product applications almost represent the development direction of the industry in the next few years.
About four years ago, in the process of contact with foreign material suppliers, I heard his sigh: We think disaster is coming, here is still partying!
Then a brief look at the source of the concern: As he knew at that time, Tesla's electric cars had redesigned the traditional automobile circuit, and both the design concept and assembly concept were completely different from the previous ones. However, a false proposition involved here was that if Tesla's approach was popularized in the industry, PCB and connector industries would be completely overturned. Because Tesla adopted FPC instead!
At that time, I just smiled and said to him, don't worry, one is the car FPC needs thick film circuit technology, Americans will not give to China; Second, the automobile electronic replacement cycle is at least five to ten years, during which you can rest assured to continue to sell your products in the Chinese market.
In recent years, as you can see in PCB and connector industries, although the industry entry threshold is constantly raised, due to the one-size-fits-all environmental policy, it is difficult for small and medium-sized innovative enterprises in these two industries to survive in the mainland of China, but it does not prevent listed companies from frantically expanding production capacity. Moreover, in the report of raising funds for production expansion, All but mentioned the bright future of automotive electronics.
Of course, from the current situation, the car PCB or connector business is still a small business of these companies, because the proportion of output value is too small, just like the 5G large base station PCB and connector business, even if you use ten thousand yuan for a large base station, the total number is only so much.
Take a look back at all the "bad" things Tesla has done. Not really. When Tesla designed the car, 90% of the one-kilometer cable line of traditional cars was replaced with FPC. Only about 100 meters of assembly line was still connected by high-rank copper cables and connectors.
In fact, it's not Tesla's fault. They're not making cars at all. They're making mobile computer robots.
What's unusual is that Tesla has also made the FPCS used in these cars standard, so that they can be assembled by robots on the production line, rather than by professional electrical technicians wiring, testing, assembling, fixing and retesting them.
You don't need to read it in detail to understand why Tesla's efficiency in the production of cars is so high. It is not the magic of simple automated production lines or gigafactory, but the "amateurs" of the car business, completely out of line with the cards, in addition to taking the laptop battery we despise as a power battery, We have used PCB, cable, connector for decades, hundreds of years, you can not look at it, using what FPC.
Materials or devices used in automotive electronics require high reliability, so FPC used in the automotive electronics industry, in fact, is not an ordinary FPC can be used. In addition, the United States has been cautious about the proliferation of weapons-grade thick film circuit technology, even allowing the emergence of civilian-grade thick film circuits. If FPC technology can replace traditional PCBS, cables, and connectors, then there is no point in regulating the thick-film circuit technology that Americans have always cared about.
As the operation of Tesla Gigafactory in China and the sales of Tesla cars in China increase, China's domestic automobile industry will absorb Tesla's technology and industrial resources at a faster and faster speed.
Unlike the automotive battery industry, Tesla can switch to the products of Chinese battery companies for the domestic policy needs of China, instead of using advanced battery management technology and advanced super batteries in China's domestic market.
But what about other components in the auto industry? Do you think it is possible for Tesla to completely transform "Tesla Motors" into "knowledge beans" by using PCB, cable, connector and other traditional products from Chinese domestic manufacturers?
It seems that it is possible to restock the listed companies with FPC technology for cars!