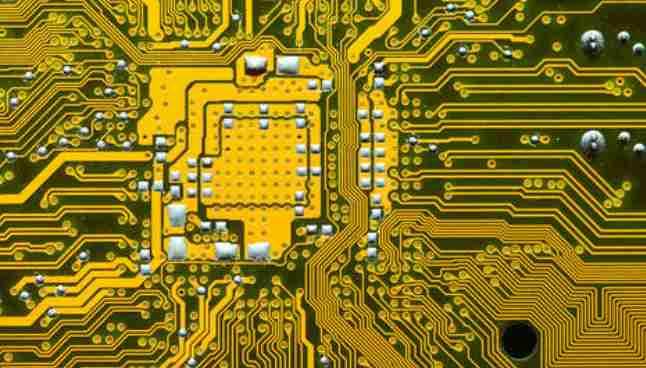
1, low loss, CAF/ heat resistance and mechanical toughness (viscosity) (good reliability)
2. Stable Dk/Df parameters (small variation coefficient with frequency and environment)
3. Small tolerance of material thickness and adhesive content (good impedance control)
4, low copper foil surface roughness (reduce loss)
5, try to choose flat window small glass fiber cloth (reduce skew and loss)
Next, we will make a detailed description of the above five requirements for high speed PCB materials.
The integrity of high-speed signal is mainly related to impedance and timely delay consistency of transmission line loss. The integrity of signal can be guaranteed if the appropriate waveform and eye map can be received at the receiving end. Therefore, the main parameters of PCB material selection of high-speed digital circuit are Dk, Df, loss, etc.
Whether analog circuit or digital circuit, the dielectric constant Dk of PCB material is an important parameter for material selection, because the Dk value is closely related to the actual circuit impedance value applied to the material. When the Dk value of PCB material changes, whether with the change of frequency or temperature, the circuit transmission line impedance will produce unexpected changes, which will adversely affect the signal transmission performance of high-speed digital circuits. If the Dk of PCB material presents different values for harmonic components of different frequencies, the impedance also presents different resistance values at different frequencies. The unexpected change of Dk value and impedance will lead to a certain degree of loss and frequency offset of harmonic components, which will cause distortion of analog harmonic components of high-speed digital signals, and thus reduce the integrity of the signal.
Dispersion, which is closely related to Dk values, is also a property of the material, and the less Dk values vary with frequency, the smaller the dispersion, and the better the application for high speed digital circuits. The polarization of dielectric material, the loss of material and the surface roughness of high frequency copper conductor will cause the dispersion of the circuit. Therefore, the Dk value of high-speed materials is required to be stable. Under different frequency segments and temperatures, the smaller the fluctuation, the better.
Transmission line losses usually include dielectric losses, conductor losses and radiation losses.
Dielectric loss can also be called insulation layer loss, PCB signal insulation layer loss increases with the increase of frequency, especially with the high order harmonic components of high speed digital signal frequency change, will produce serious amplitude attenuation, resulting in high speed digital signal distortion. Dielectric loss is proportional to the signal frequency, the square root of the dielectric constant Dk of the insulation layer, and the dielectric loss factor Df of the insulation layer.
Conductor loss is related to the type of conductor (different kinds have different resistance), insulating layer and physical size of conductor, and is proportional to the square root of frequency; In PCB manufacturing, the main influence of different substrates on conductor loss is caused by skin effect and surface roughness. When different copper foils are used, the surface roughness of signal lines is different. Affected by skin effect/depth, the length of copper foils and copper teeth is directly related to the transmission quality of high-speed signals.
The radiation loss is related to the dielectric properties and is proportional to the dielectric constant Dk, the dielectric loss factor Df, and the square root of the frequency.
Reminder: The better the material, the higher the cost will be. Engineers should strike a balance between meeting the design requirements and mass production and cost, so as to meet the best cost performance of the product.
10. Arrange the devices with the highest power consumption and maximum heat dissipation near the optimal location for heat dissipation. Do not place hot components at the corners and edges of the printed board unless a cooling device is arranged near it. Choose as large a component as possible when designing the power resistance, and adjust the layout of the printed board to allow enough space for heat dissipation.
11, high heat dissipation devices in connection with the substrate should be able to reduce the thermal resistance between them. To better meet the requirements of thermal characteristics, use some thermal conductive materials (such as a layer of heat-conducting silicone) on the bottom surface of the chip, and keep a certain contact area for heat dissipation.
12, device and substrate connection:
(1) Shorten the lead length of the device as far as possible;
(2) When choosing high-power devices, the thermal conductivity of the lead material should be considered. If possible, try to choose the maximum lead transverse surface;
(3) Select devices with more pins.
13. Package selection of devices:
(1) When considering thermal design, attention should be paid to the package description of the device and its thermal conductivity;
(2) Consideration should be given to providing a good heat conduction path between the substrate and the device package;
(3) In the heat conduction path should avoid air partition, if there is such a case can be filled with thermal conductive materials.