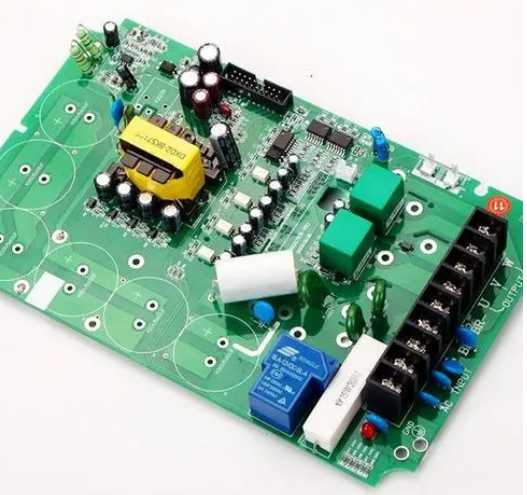
kingford is equipped with a team of professional component purchasing specialist and incoming material analysis and control engineer responsible for component purchasing and quality control, and professional PCBA production engineer responsible for SMT productionline operation. Business, purchasing and production departments can cooperate with the review of new orders, production arrangement and product testing. The following patch processing manufacturers to explain how to achieve PCBA rapid proofing and patch processing how to do a good job of material management knowledge.
1. How to do material management in patch processing
Material management is a very important process in SMT patch processing. Only strict material management can guarantee the smooth progress of SMT patch processing. In actual processing, we will encounter various SMT stoppage and rework caused by improper material management. Next, Shenzhen SMT SMT processing manufacturer - Shenzhen kingford Electronics to introduce the SMT SMT processing existing material problems and SMT processing material management measures. Material problems in SMT processing 1. Material loss (Grade A materials, PCB, CHIP materials); 2. Material throwing material (Grade A material, CHIP material); 3. Scrap materials (Grade A materials, PCB). Material management measures for SMT patch processing To solve existing problems, reduce manufacturing costs, improve delivery time, and strictly manage and use materials, the following management measures can be taken:
1. All raw materials brought into the workshop from the warehouse must be counted and logged by the material technician, and correctly placed in the material rack according to the Material Station Table or BOM of the current or future products to be put into production, and clearly marked. Any substitution or change should be confirmed in time and informed to relevant personnel.
2. In the process of operation, the material technician shall make A hundred percent count of Grade A materials or spare materials. If any doubt or deficiency is found, it shall immediately reflect and follow up. After the completion of the work order, the remaining materials should be properly stored and logged in or returned to the warehouse.
3. In the process of SMT patch proofing or processing and production, the material technician shall inspect the MISS condition of each equipment at any time, and cooperate with the team leader and engineering staff to improve it. Collect and classify the parts in time, and submit them to IPQC for confirmation before use.
4. During refueling operation, refueling technicians must carefully check the label of empty tray and "Material Station Table" with the material and label in the rack, and truthfully fill in the "Refueling Record Form".
5. The use of materials should be in line with the principles of first-in, first-out, full-in, full-out, first-round and then zero, timely collection and packaging of loose parts to avoid leaving or overloading. It is strictly prohibited to use or abuse the same specifications but different materials from manufacturers and customers.
6. The production line is equipped with empty trays and special garbage boxes. The operators should place the empty trays neatly in the special boxes when refueling, and check them carefully before getting off work every day to ensure that no materials are abandoned in them. If there are defective or discarded materials, the data should be accurate and clearly marked before handing over to relevant personnel. Choose Shenzhen kingford to do SMT SMT processing four reasons.
2. How to achieve PCBA fast proofing
Can provide 5-500 sets of PCBA fast proofing service. PCBA proofing is an important link that must be carried out before PCBA processing and production. The most important purpose of proofing is to verify whether the product design is reasonable, to detect the problem at the minimum cost, and to save the cost for the mass production. Often, when PCBA proofing is carried out, There is not much time left for engineers or product companies, so they often ask PCBA processing plant to speed up the progress of proofing, hoping to get the samples as soon as possible. Generally, the PCBA proofing time is 7-14 days, and the fast proofing only needs 3-5 days to complete, then the 3-5 days of PCBA fast proofing how to complete?
Firstly, it is necessary to ensure the accuracy of Gerber files and BOM files, and replace the components with those with a long delivery period with those that can be placed and taken delivery immediately. Because the proofing is only a preliminary verification of product design, alternative materials can be used appropriately to save the proofing time, or the supplier has prepared the materials with a long period before the proofing. When you want to make samples, you can directly pick up the goods, which is also a common method to reduce the waiting time for materials. When all the materials are set, the rest of the production is actually a very fast thing, usually only need to spend 1-2 days can be done, so in summary, the process of PCBA processing fast proofing is: prepare the data → choose the appropriate replacement material → procurement → production → verification. In the process of doing PCBA fast proofing, we must know our purpose, focus on the big and small, in order to achieve PCBA fast proofing.
▪ SMT workshop: We have imported SMT machines and several sets of optical inspection equipment, with a daily output of 4 million. Each process is equipped with QC personnel, who can keep an eye on product quality. ▪ DIP production line: We have two wave-soldering machines, among which there are more than 10 old employees who have worked for more than three years. The skilled workers can weld all kinds of plug-in materials.
2. Quality assurance, high cost performance. High-end equipment can stick precision special-shaped parts, BGA, QFN, 0201 materials. Can also template patch, loose material hand. ▪ Sample and size batch can be produced, proofing from 800 yuan, batch 0.008 yuan/point, no start-up fee.
3. Rich experience in SMT and welding of electronic products, stable delivery. Accumulated services for thousands of electronic enterprises, involving many kinds of automotive equipment and industrial control motherboard SMT processing services, products are often exported to Europe and the United States, quality can be affirmed by new and old customers. ▪ On time delivery, normal 3-5 days after complete materials, small batch can also be expedited on the same day shipment.
4. Strong maintenance ability, perfect after-sales service ▪ Experienced maintenance engineers, can repair all kinds of patch welding caused by bad products, to ensure the connection rate of each piece of circuit board. ▪ 24-hour customer service staff at any time response, the fastest speed to solve your order problems.