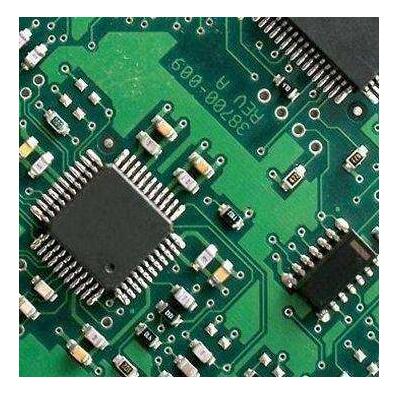
Holes on the PCB board are divided into coated holes (PTH) and non-coated holes (NPTH) according to whether they participate in the electrical connection.
Coated hole (PTH) refers to a metal-coated hole in the wall that enables electrical connections between conductive patterns on the inner, outer or inner layers of the PCB. Its size is determined by the size of the borehole and the thickness of the metal coating.
Non-plated hole (NPTH) does not participate in the PCB electrical connection of the hole, that is, the nonmetallic hole.
According to the level of holes through the PCB's inner and outer layers, holes can be divided into through holes, buried holes and blind holes.
The through-hole runs through the entire PCB and can be used for inner connection and positioning and installation of components. Wherein, the holes for the component terminals (including pins and conductors) to be fixed and, or to achieve electrical connection with the printed circuit board are called component holes. A plated hole used for inner connection without inserting component leads or other reinforcing material is called a pass hole. The purpose of drilling through a PCB is twofold: one is to create an opening through the board, allowing subsequent processes to form electrical connections between the top, bottom and inner wiring of the board; Second, the installation of components on the board to maintain structural integrity and position accuracy.
Blind and buried holes are widely used in high density interconnection HDI. Blind holes usually connect layer 1 to Layer 2. In some designs, blind holes can connect layers 1 to 3. Combining blind and buried holes allows for more connections and higher board densities required for HDI. This allows for increased layer density in smaller spaced devices, while also increasing transmission power. Hidden through-holes help keep the board light and compact. Blind and buried hole designs are common in complex, lightweight, and costly electronic products such as mobile phones, tablets, and medical devices. Blind holes are formed by controlled drilling depth or laser ablation. The latter is the more common method used today. The stack of pilot holes is formed by sequential lamination. The resulting pilot holes can be stacked or staggered, adding additional steps to manufacturing and testing, as well as increasing costs.
According to the purpose and function of the hole, it can be divided into:
Through hole (via) A metallized hole for electrical interconnection between different conductive layers on a PCB circuit board, not intended for use as a plug-in component.
PS: The through-hole here can be subdivided into through-hole, buried hole and blind hole according to the level of through-inner and outer layers of PCB mentioned above.
A hole, usually a metallized hole, used for welding fixed plug-in electronic components and connectors. It also doubles as an electrical connection between different conductive layers.
Mounting hole: A large-diameter hole on a PCB used to secure the PCB to a carrier such as the shell.
Slot: A slot that is automatically converted into a collection of multiple single holes or machined by milling in the drilling program of a drilling rig. It is generally used as the installation of pins of plug-in devices, such as oval pins of sockets.
Back drilling: A hole of a certain depth (larger than the front electroplated through hole) is drilled in the electroplated through hole to block the stub of the hole and reduce the reflection during signal transmission.
The following are some auxiliary holes used by PCB manufacturers in the process of PCB manufacturing. PCB design engineers can have a general understanding of them:
Positioning hole: Three or four holes at the top and bottom of the PCB. Other holes on the board take this as the benchmark, which is also called target hole or target hole. Before drilling, the target hole machine (optical hole punching machine or X-RAY target drilling machine, etc.) is used for pin positioning and fixing during drilling.
Inner counterholes: Holes at the edge of a multilayer board used to determine whether the board is offset before drilling in the board pattern. Thus determine whether the drilling procedure needs to be adjusted.
Code hole: a row of holes on the bottom side of the board, used to indicate some information about the production, such as product model, machining machine, operator code, etc., many factories now use laser typing instead.
Tail hole: A number of holes in the edge of the plate of varying sizes used to determine whether the drill bit is being drilled correctly during use. Many factories now use other techniques instead.
Slice hole: Coated hole for PCB slice analysis, can reflect the quality of the hole.
Impedance test hole: Coated hole used to test PCB impedance.
Anti-hole: generally non-coated hole, used to prevent the plate position reverse, often used in forming or imaging process positioning.
Tool holes: Generally non-coated holes, used for related processes.
Rivet hole: non-coated hole, used for riveting fixation of each layer of core plate and bonding sheet when multilayer plate is pressed together. When drilling, the rivet position should be drilled through to prevent residual bubbles in this position, which may lead to subsequent plate explosion.