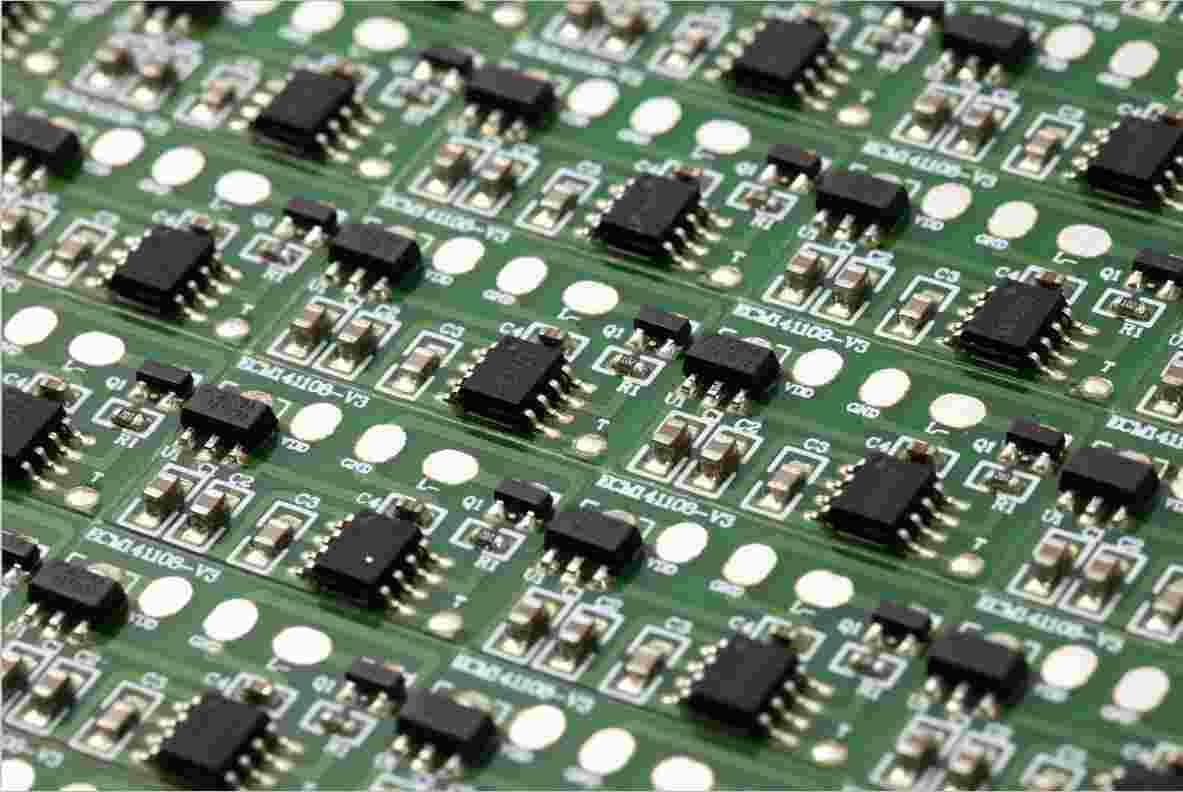
PCB drilling method
Over the decades of PCB industry development, the use of mechanical drill holes has been the dominant technology, mechanical drilling has withstood the growing demand for printed circuit boards, and is still recognized as a safe and cost-effective method of opening holes. Of course, for small aperture requirements of the circuit board, you can also use laser drilling, but the cost is much higher.
Since the hole position of each PCB design project is different, the PCB board factory would Control and drill the hole position of Numerical Control Date (NC data) based on the design information.
Can the holes on PCB be drilled at will?
In theory, for the current advanced CNC machining, as long as it is greater than the minimum machining size, any shape of the hole can be processed out.
However, the number of holes in a standard PCB machining panel may be in the thousands, and it is obviously much more efficient and economical to drill directly with a standardized drill bit.
So, the size of the drill on the PCB is obviously limited at least by the size of the mechanical drill bit, and the size of the drill bit can be as big as the size of the hole.
Many bits of different specifications are placed on the side of the drilling machine, and the drilling machine will automatically replace the bits of the corresponding diameter according to the different holes on the PCB.
But every time you replace a bit, you need to go through a series of operations, such as picking up the new size bit, unloading the current bit, loading the new size bit, repositioning the bit and so on. This involves the processing efficiency. Of course, the plate factory hopes that you can drill a size bit in the end.
At the same time, the bit diameter specification is also in proportion to a certain scale, not any size of the bit specifications, which involves the optimization of the aperture specification.
PCB board factories do not manufacture their own drill bits, but purchase drill bits for PCB drilling, and standard drill bits are manufactured in 0.05 mm increments. Before PCB manufacturing, the board factory will optimize the round hole in our PCB design according to the bit specifications of the board factory. Domestic board factories generally adopt the metric system, and the aperture will be in millimeter and rounded to the nearest bit specification with 0.05mm increment.
Is it done when the holes in the PCB are drilled?
For the interconnection between layers, we also need to protect the holes. In PCB, the hole to realize interconnection conduction is plated with a thin layer of copper in the drilled hole wall through the subsequent electroplating process to realize the conduction in the hole, that is, the metallization of the hole.
How thin is the copper in this hole wall.
The copper in the hole wall is a very thin layer, and the hole is empty state, so it is necessary to avoid the copper in the hole wall in the subsequent process by chemical solution corrosion or long-term contact with the air, atmospheric corrosion of copper will affect the electrical connection performance of the hole, that is, the long-term reliability of the hole, and also to avoid the impact of the hole on the subsequent PCB manufacturing and assembly process, such as:
Prevent soldering or reflow solder into the hole, affect the appearance of PCB or tin short circuit
The PCB needs to be vacuum-grabbed or fixed during subsequent processing, and unsealed through holes will affect air tightness
Among them, the simplest and no additional process cost method is the hole cover oil, that is, similar to the welding resistance protection of the line, the welding resistance ink will cover the hole to achieve the protective effect of the hole closure.
It should be noted that the smaller the diameter of the hole, the better the cover effect of solder resistance ink, diameter less than 0.3mm hole cover oil effect is better, and diameter between 0.3mm to 0.5mm hole, filling effect may not be the same, because this is an uncontrolled process.
The advantage of using the hole cover oil is that there is no extra cost, but the hole cover oil also has shortcomings. In the process of ink baking, the ink is permeated into the hole, especially the hole with a larger aperture, which cannot be 100% guaranteed that the hole is covered by welding resistance oil without light leakage. The plate factory can only ensure that the hole of the cover oil is no longer sticky tin. However, the hole ring may affect the appearance of PCB by false copper yellows. The hole that is not completely closed may also hide potions or tin beads in the subsequent process, resulting in reliability problems.
Even if the hole has been closed by solder resistance ink, in the subsequent process of heat cycle, the heat expansion of the air in the hole will cause the solder resistance ink to burst.
As for the process of hole cover oil, if it is only PCB proofing, the PCB design is verified without the pursuit of long-term reliability of hole through, there is no scene like BGA where the fan hole is very dense, and there is no strict requirement on the appearance of PCB hole through.
For mass-produced PCBS that pursue long-term perforation reliability, at least the perforation should not be allowed to burst the closed hole due to the expansion of air in the thermal cycle of the subsequent process. The best approach is to fill the hole without leaving air in it, and the commonly used ink plug hole or resin plug hole process.
The ink plugging process, although the heat cycle process will not burst, but there will be the problem of oil, not only affect the appearance of PCB, but also affect the SMT yield.
For PCB with BGA encapsulated chip requiring SMT welding, since the BGA fan outlet hole is very close to the BGA pad, it is recommended to use the through hole plug resin process to fill the hole.
Choice of over hole protection process trade-offs
Through the hole window, through the hole cover oil, through the hole plug oil, through the hole plug resin, copper paste Jia Li Chuang home to provide a variety of options.
The normal process must be to close and protect the through holes. Plate factories generally produce by default according to the through holes protection process. If some holes need to be used as test points or heat dissipation, graphic information corresponding to the through holes and Windows should be added to the solder resistance layer in Gerber.
The hole cover oil, for the sample does not require the long-term reliability of the hole, do not worry about the hot cycle cover oil explosion caused by poor welding, can use the hole cover oil process, after all, will not be more money.
Through hole plug oil, through hole plug oil process relative to through hole cover oil, the reliability of through hole protection is greatly improved, can achieve 100% plug hole opaque, PCB appearance is more beautiful, but the expansion coefficient of plug hole ink is too large compared with PCB resin, which causes the plug oil in the subsequent thermal cycle, there will be through hole oil, for the BGA fan through hole, The through hole is very close to the pad, the oil will pollute the pad of BGA, bringing the risk of poor welding, and the through hole plug oil is not suitable for the plate hole process.
The through hole plug resin is completely filled inside the through hole, so the risk of chemical residue or tin bead residue in the through hole can be completely eliminated. There is no air in the hole, and the air will not make the filling of the through hole burst due to thermal expansion. At the same time, the expansion coefficient of the filled resin is close to that of the PCB substrate resin. The PCB has better appearance, which is very suitable for the SMT process of BGA. At the same time, the process of plate hole via in pad can be realized by electroplating after plugging the hole with resin.