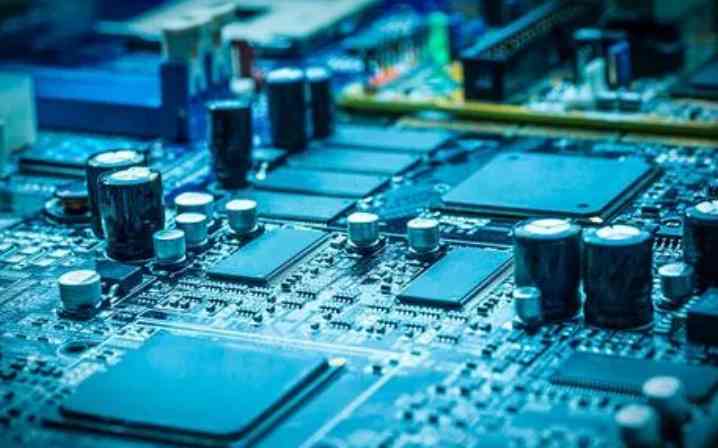
n order to ensure the high reliability and safety of the circuit board in key applications, three anti-corrosion paint is widely used on the circuit board, because electronic failure may cause very serious consequences, even including life-threatening. In order to ensure that the reliability and safety of the three coatings meet the requirements, the components coated with the three coatings must be exposed to a range of different environments under appropriate test conditions to determine the range of performance and limitations suitable for the board function. Basic tests include electrical performance tests and accelerated humidity tests, with advanced tests that simulate a variety of harsh environmental conditions, such as salt spray, extreme temperatures, or rapid environmental changes. The purpose of applying tri-resistant paint in circuit board design is to protect PCBS and ensure that they will work effectively in the final use environment. However, in some cases, even if the circuit board is coated with three-proof paint, the circuit board may have local dysfunction, or even complete failure. In this case, these three-proof paint tests become a costly and time-consuming nightmare for the manufacturer of the circuit board, and will affect the manufacturer's reputation. In this article, Phil Kinner, Electrolube's global Business and Technical Director for tri-paint, explores why testing a tri-paint coated circuit board is so important and analyzes the variables that can lead to board failure.
With the development of electronic technology, more functions have to be achieved in a smaller size, the chance of circuit board failure has increased. As component sizes get smaller and the spacing gets narrower, many designs are approaching the limits of design rules, sometimes even pushing the limits of manufacturability. The more a designer pushes the limits of manufacturability, the greater the chance of failure.
In addition to problems related to the design of the board, when the board is exposed to moisture and ionic contaminants, because the components are denser than before, they are closer together, making the hardware on the board more vulnerable to corrosion, a complex, diffuse-controlled electrochemical process that occurs on exposed metal surfaces. Cleaning the circuit board before applying the triple paint is a way to remove corrosive conditions, which can be applied more effectively, improve the surface insulation resistance in these sensitive designs, and reduce the failure caused by the working environment.
As PCB is very complex, there are many variables that may cause the failure of the circuit board. Some failure mechanisms occur slowly, which can be helpful for detection, maintenance, and even repair, but others are sudden and unexpected, in which case the PCB is more likely to fail completely. Even though the circuit board has been coated with three anti-paint, but still the failure will occur, the reason for this is that the PCB before the three anti-paint coating process already existed problems, and also the coating material itself may not be suitable for the circuit board, or the coating method is not suitable for the circuit board. There are many other factors that can affect proper coating of the PCB, including failure to clean the components before coating, failure to remove the original tri-guard paint from the surface, electrostatic discharge, and possibly even poor construction of the unit to be coated itself.
The first and most critical step in applying a tri-resistant paint to the circuit board is to inspect the board before applying it. This step is critical as it verifies the overall quality of the PCB to be coated and ensures that it is suitable for the coating material and meets the customer's specifications. The inspection performed at this stage is also critical to detect any conditions that may cause the board to fail, such as component failure, insufficient thickness of the board, loose connections that affect the performance of the connection. When it comes to protecting the circuit board, the three-proof paint does have its limitations. During coating operations, pre-existing contaminants on the circuit board can be sealed by the coating, which can lead to long-term problems -- these contaminants can include fingerprints, flux residue and moisture, as well as other atmospheric pollutants. In order to achieve the best performance of the circuit board, the board should be cleaned and dried frequently before applying the triple resistant paint. Even when the board is assembled using a so-called no-clean flux, cleaning before applying the tri-proof paint can help improve the performance and reliability of the board.