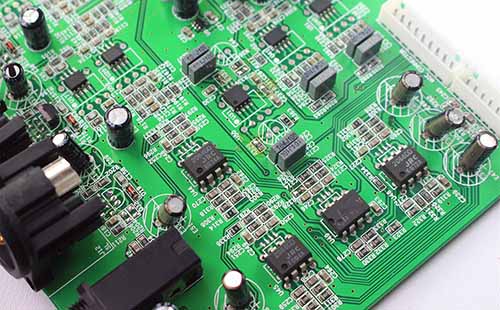
Detailed explanation of PCBA welding industry quality standards
The quality standard of PCBA welding industry, namely IPC-A-610 Acceptability of Electronic Components, is the acceptability standard of international electronic assembly. It is formulated by the global non-profit International Electronic Industry Connection Association and has become an internationally recognized standard. At present, IPC-A-610E is the latest version.
IPC-A-610E collects the acceptable requirements for appearance quality of electronic components in the industry, and describes the acceptance requirements for the manufacturing of electrical and electronic components.
1. Standard definition
[Accept Criterion]: The acceptance criteria include ideal conditions, acceptance conditions and rejection conditions.
Target Condition: This assembly situation is close to the ideal and perfect assembly result. It has good assembly reliability and is judged as ideal.
[Accept Condition]: This assembly condition is not in line with the ideal condition, but it can maintain the assembly reliability, so it is regarded as qualified and judged as acceptable.
Reject Condition: This assembly condition fails to meet the standard, which may affect the functionality of the product. However, based on the appearance factors to maintain the competitiveness of the company's products, it is determined as a rejection Condition.
2. DEFINITION OF DEFECTS
[Critical Defect]: refers to a defect that can cause injury to human body or machine, or endanger the safety of life and property. It is called a fatal defect, and is represented by CR.
[Major Defect]: it refers to the defect that has lost the practicality or reduced the reliability of the product in terms of its substantial function. Product damage and poor function are called major defects, which are represented by MA.
[Minor Defect]: refers to the service performance of a unit defect, which does not substantially reduce its usefulness, but can still achieve the desired purpose. Generally, it is the difference in appearance or mechanism assembly, expressed in MI.
3. Welding and high voltage
Acceptability requirements for welding, abnormal welding, high voltage welding connection.
4. Connection of terminal
Riveted parts, insulating skin, conductor, repair ring, terminal - stress relief, terminal - lead wire/wire placement - general requirements, terminal - welding - general requirements, tower and straight thorium needle shaped, double fork shaped, slot shaped, perforated shaped, hook shaped, solder cup, AWG 30 and thinner wires, serial connection, edge clamp spring.
5. Through hole technology
Placement of elements, fixing of components, support holes, non support holes, jumpers.
6. Surface mount assembly
Adhesive fixation, SMT lead, SMT connection (only bottom terminal, 1-3-5 end faces, cylinder cap shaped, castle shaped, flat gull wing shaped lead, round or flat round gull wing shaped lead, J-shaped lead, I-shaped connection, flat solder, high profile bottom terminal, inner L-shaped, BGA, bottom terminal components, components with bottom radiator terminal, flat head connection), special SMT terminal, surface mount connector, jumper, etc.
7. Component damage and printed circuit board and its components
Printed circuit boards and components (gold surface contact area, laminate condition, conductor/pad, flexible and rigid printed circuit, marking, cleanliness, solder mask coating, conformal coating, potting), component damage, etc.
8. Discrete cabling
No welding winding (number of turns, turn gap, winding of wire end/insulation section, overlapping of wire turns, winding position, wire arrangement, wire relaxation, wire coating, insulation skin damage, conductor and connection).
IPC-A-610E is the basic standard for PCBA welding processing. When checking the appearance of PCBA, it can be referred to. However, the actual PCBA welding standard is more strict. Generally, the final quality inspection standard is obtained by combining the quality standard of PCBA welding industry with the specific customer.
PCB manufacturers, PCB designers and PCBA processors explain the quality standards of PCBA welding industry.