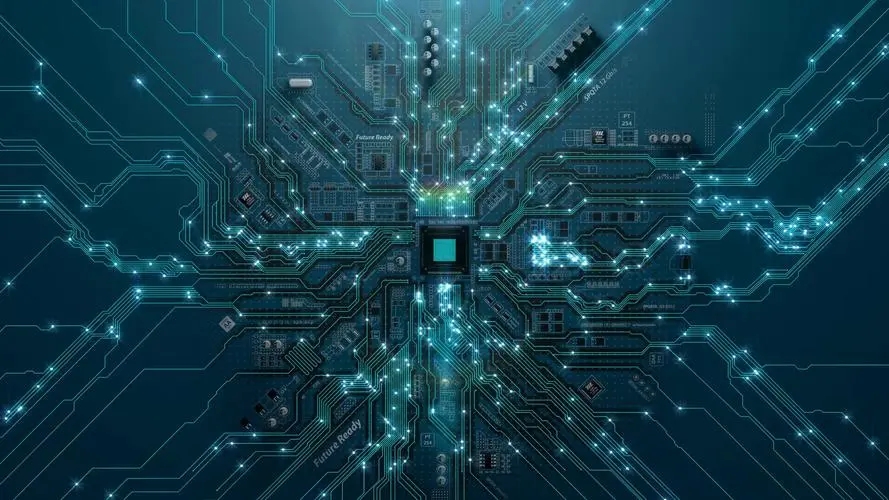
Surface treatment of lead-free welding by immersion silver plating
Circuit board manufacturer explains the surface treatment of lead-free welding: silver immersion
There are many kinds of lead-free soldering in SMT chip processing. OSP was introduced earlier, and another common processing method, silver immersion, is introduced here.
In the electrokinetic series arrangement of various elements in acid solution, the potential of silver is+0.80V, while that of copper is+0.52V; Copper was 0.279V more active than silver. Therefore, it is not difficult to prepare a silver bath for copper dissolution and silver deposition. In addition, at the moment of welding, the silver layer will soon dissolve into the high-temperature solder joints;, Therefore, the soldering time is very short and the solderability is very good, and the subsequent solder joint strength is very reliable. It can be seen that the silver layer does not participate in the structure of solder joints at all, but only protects the copper surface from rust.
1、 Organic Silver Summary
The new organic silver immersion plating with silver nitrate as the formula has four main processes, namely, pre cleaning of copper surface, micro etching, conditioning treatment, and silver immersion plating; Horizontal automatic conveying mode can be adopted for continuous double-sided processing. There are many current processes of silver dipping after green paint. Famous brands in Taiwan, such as SterlingTM Silver of MacDermid, Alpha Level of Cockson, and Silver Finish ST of Atotech, can only dip silver when specially designated by customers, because of various solder problems that they can't afford or solve! The customer should specify that the responsibility is not mine.
Although silver is also listed in the group of precious metals, the surface of pure silver is very easy to produce an ugly skin film of vulcanization and oxidation in the normal temperature environment, that is, the so-called Tarnish (pollution or discoloration) or Passivation (passivation) stubborn inferior film. In the absence of cleaning flux, it will immediately have a negative impact on the solderability. Therefore, various anti tarnish and anti tarnish treatments for silver surface have been the unremitting goal of metal surface treatment industry for many years.
Some organic inhibitors must be added into various commercial "silver dipping" baths to make them deposited in the coating, so as to help prevent the silver surface from discoloration. However, in practice, the first high temperature fusion welding almost has no defects, but the second fusion welding or wave welding depends on the degree of discoloration. Once it turns brown, even if it is highly active and water-soluble, it is still indifferent to excessive discoloration. Therefore, when doing the first welding, you must be careful not to pollute it, so as to prevent its delicate solderability from being stained and deteriorated.
Generally, the thickness of silver dip plating is about 0.2-0.3 μ The flatness is excellent. The organic inhibitor co deposited in the skin film can be seen from Auger depth profile. Such organics will be evenly distributed at 0.075 μ M surface depth. The distribution ratio of the amount of pure silver, organic matter and micro copper in the silver immersion coating is directly related to the depth of the film thickness. The following figure shows the relationship between the proportion of the three and their depth.
As for silver dip plating introduced by Alpha Level, the average thickness is 4-5 μ in(0.125 μ m) , a thin (5A) transparent organic protective film will appear on the surface upon completion, which is similar to the OSP protective film on the copper surface. Its imaginary composition can be seen in the following section diagram.
Modified organic silver surface treatment layer
The surface glossiness of silver dipping is directly related to the micro etching coarsening of the copper substrate. When the roughness of the bottom copper surface is large, the silver surface will have a foggy appearance. The thickness of deposition is related to treatment time, temperature, pH, and silver ion concentration. From the principle of replacement, when a copper atom dissolves into a univalent copper ion, there will be a synchronous deposition of silver atoms, and Cu+will continue to be oxidized into blue Cu++and enter the solution as pollution.
Such "organic silver" I-Ag bath solution is available in acidic formula (SterlingSilver of Matt), neutral formula (Silver Finish ST of Ato) and other commodities. In addition to the main agent silver nitrate or organic acid (MSA methyl sulfonic acid) silver, the cylinder must be added with organic copper complexing agent (to prevent the copper in the bath solution from having adverse effects on the reaction), organic inhibitor (to prevent the bath solution from being sensitive to light and to strengthen the uniformity of the coating), Surface wetting agent (to prevent the subsequent undesirable electromigration of silver layer and inhibit the occurrence of discoloration) and buffer (to adjust pH), etc. As a result, the replaced I-Ag coating is no longer a simple metallic silver layer, but a coating mixed with organic matter, called "organic silver". In addition, the horizontal mass production line is also equipped with a "copper crystallizer" to remove too much dissolved copper and extend the life of the bath solution‘
2、 Improvement of migration of organic silver seals
As organic inhibitors have been infiltrated into the silver immersion coating, the industry has long been worried about the consequences of rapid "silver migration". It seems that it can breathe a sigh of relief. According to the ElectroMigration ResistanceTest of Telcordia TR-78, the researchers of Matte Company once found that the resistance of silver immersion coating was higher than that of bare copper and tin spraying after 96 hours and 596 hours of aging respectively under the conditions of 85 0C/85% RH and bias voltage (Bias) 10VDC. The high electrometeorite value of course indicates that the migration phenomenon has been reduced, thus it can be proved that the electrical migration between dense lines will no longer occur in the impregnated organic silver layer.
3、 Soldering property of organic silver
As for the solderability, it seems that it is better than OSP after research by many manufacturers, and it is no inferior to the tin plate. Even the samples after steam aging still show good solderability. Others deliberately made it pass through three times of high temperature fusion welding, and found from the Wetting Balance test that its Wetting Force was almost equal to the brand new sample. In addition, many operators have also confirmed that silver immersion is also very good in the results of various reliability tests.
In addition to being available for welding, the silver immersion barrel can be used as the surface treatment of semiconductor wire bond. Generally, for ultrasonic aluminum wire with a diameter of lOmil, the effect is quite good. Sometimes it can also be used as a contact connection, but it is directly related to the thickness. When the micro etching of the bottom copper surface is coarsened to a certain extent, the silver immersion thickness is usually 10 μ m. So you can execute the contact task.
However, these excellent solderability and anti-aging ability are all written for the purest and cleanest bath solution and sample. Once the operating bath solution is slightly polluted, or the surrounding environment for assembly and welding is not ideal, the solderability presented by silver dipping will be greatly different. The current solderability of silver dip plating will be seriously affected by trace ammonia, sulfur dioxide (SO2) and nitrogen dioxide (N02) in water gas. The water quality in the immersion process is also extremely important, and a little chlorine ion pollution will bring bad adverse effects. In addition, special "sulfur free paper" should also be used for shipping packaging. This kind of delicate paper is not only very expensive but can only be used once. When arriving at the client, the paper seal must be removed one by one, and the board must be immediately "stamped with parts" and welded. If the site environment is left too long, the solderability may cause problems. When welding again for the second or third time, the disaster scene of poor welding and refusal to weld was really terrible, and the Sales talk had to be silent
4、 Process Management of Silver Dipping
The commercialized silver dip plating is known only by "Silver Finish ST" of German ATO, Sterling of American Matt and Alpha Level of Cockson. The following five stations are the horizontal process of "Silver Finish ST".
Two key pre-treatments, including micro etching and Conditioner, can slow down the initial silver plating, reduce the porosity of the overall silver layer, and increase the compactness of the crystalline structure. The silver carving in this non nitrate silver bath appears as a halogenated complex of (AgX2,, It will slow down the replacement rate of silver immersion plating, reduce the increase of copper ions in the bath, and reduce the functions of porosity and densification crystallization. The thickness of 0.2-0.4 can be obtained by immersion silver plating at pH 7.5-8.5, temperature 60 ℃ for 2-3 minutes μ m. The whole process only takes 6-7 minutes on average