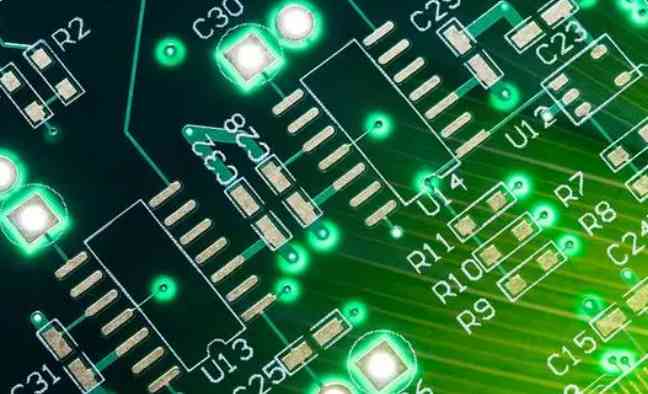
The integrity of the power supply and the ground is also a very important factor in high speed circuits, because the integrity of the power supply and the integrity of the signal are closely related. In most cases, the main cause of signal distortion is the power system. For example, too much ground rebound noise, inappropriate design of decoupling capacitance, multiple power sources or poor ground plane segmentation, unreasonable ground design, unequal current distribution will lead to power integrity problems, resulting in signal distortion and affect signal integrity. The main ideas are to determine the power distribution system, divide the large size circuit board into several small size boards, determine the decoupling capacitance according to the Ground Bounce noise (Ground Bounce), and consider the whole PCB board.
When there is a large current inrush in the circuit, ground elastic will be caused. For example, when a large number of chip outputs are turned on at the same time, a large transient current will flow through the power plane of the chip and the board. The inductance and resistance of the chip package and the power plane will cause power noise, which will produce voltage fluctuation and change on the real ground plane, and this noise will affect the action of other components. In the design, reducing the load capacitance, increasing the load resistance, reducing the ground inductance and reducing the number of devices switching at the same time can reduce the ground elastic. Due to geoelectric plane segmentation, for example, the stratum is divided into digital ground, analog ground, shielded ground, etc., when the digital signal goes to the area of analog ground wire, ground plane backflow noise will be generated. At the same time, according to the different devices selected, the power layer may also be divided into several different voltage layers, in this case, ground elastic and reflux noise need more attention. The choice of power distribution system and decoupling capacitance is very important in the design of power supply integrity. Generally, the impedance between the power supply system (the power supply and the ground plane) is as low as possible. The desired target impedance can be determined by specifying the maximum range of voltage and current variations, and then the impedance of each part of the power system can be approximated by adjusting the relevant factors in the circuit. For decoupling capacitors, must consider the parasitic parameters of capacitors, quantitative calculation of the number of decoupling capacitors and the capacity of each capacitor and the specific location, as far as possible to do a capacitor is not much, not a few. In the Cadence simulation tool, the ground bounce is known as Simultaneous switch noise. In the simulation, the parasitic inductance, capacitance and resistance between the power supply, as well as the parasitic inductance, capacitance and resistance of the device package are considered, and the results are more consistent with the actual situation. It can also be based on the circuit type and working frequency of the system, set the expected parameters of the relevant indicators, calculate the appropriate capacitance size and the best placement position, design a grounding circuit with low impedance to solve the problem of power integrity.
3. Design method of high speed PCB
Traditional design methods
Traditional design methods, before the final test, do not do any processing, basically rely on the experience of the designer to complete. Only when the prototype is tested can the problem be found and the cause of the problem be determined. In order to solve the problem, it will probably have to be designed from scratch again. Both in terms of development cycle and development cost, this method which mainly relies on designers' experience can not meet the requirements of modern product development, let alone the high complexity of modern high-speed circuit design. So must use advanced design tools to qualitative and quantitative analysis, control the design process.
3.2 Cadence design method
More and more, high-speed design is a more efficient way to speed up the development cycle. First, a set of physical design rules is established to meet the design performance index, through which the PCB layout is restricted. Before the device installation, the simulation design is carried out. In this virtual test, designers can compare design metrics to estimate performance. These key preconditions are to establish a set of physical design rules for performance indicators, and the rules are based on model-based simulation analysis and accurate prediction of electrical characteristics, so the simulation analysis at different stages is very important. Cadence software has developed its own design process for the design of high-speed PCB, as shown in Figure 2. Its main idea is to prevent the occurrence of problems with good simulation analysis and design, and try to solve all possible problems before PCB production. Compared to the traditional design flow on the left, the main difference is the addition of control nodes to the flow, which can effectively control the design flow. It integrates schematic design, PCB layout and high-speed simulation analysis, which can solve the problems related to electrical performance in every link of design. By analyzing many factors such as timing, signal noise, crosstalk, power structure and electromagnetic compatibility, the optimal design can be made for the signal integrity, power integrity and electromagnetic interference of the system before wiring.
4 Conclusion
High speed PCB design is a very complex system engineering, only with the help of those who can not only calculate the physical and electrical characteristics of each component used in the design of the impact and interaction, but also must be able to automatically extract and build models from the design of the PCB, In addition, EDA software tools with powerful functions such as simulators that can describe dynamic characteristics of actual design operations can solve the above problems of signal integrity, electromagnetic interference and power integrity more comprehensively. In the specific design process, in the horizontal requirements of all parts of the designers full cooperation, in the vertical requirements of each stage of the design comprehensive consideration, the design and simulation throughout the whole design process, to achieve the process of control, the quantification of specific indicators. Only in this way can we achieve efficient design.