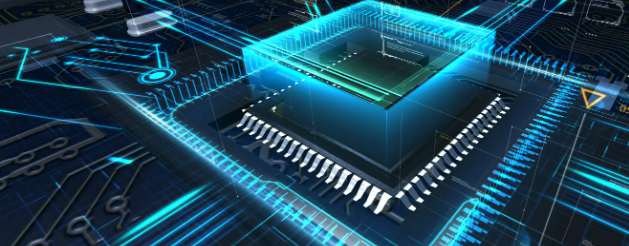
Solder paste printing technology originated from the well-established industry of silk screenprinting, so the term "silk screenprinting" came to be used for solder paste printing, which requires a thicker sediment. Thick latex mesh is originally much more economical than metal formwork, but it does not last long and is not practical for tight feet (finepitch).
The manufacturing process is as follows:
Lay a sheet of nylon, polyester, or stainless steel wire mesh over the frame. Stainless steel wire is best because of its rigidity. Industrial screen printing with a very fine mesh, about 400 silk per inch, so small ink particles (2~3μm) can be very smooth through the screen. To pass the tin beads through the mesh, a much coarser mesh of about 80 threads per inch is recommended.
The screen is coated with a photosensitive latex, usually about ten layers, to seal the mesh, forming a layer typical of 8thou thickness. Place positive phototaxis (black pad) clear glass on top and expose it to strong UV light (e.g., 2kw for a few seconds). Exposure area hardened, soft areas not exposed, can be washed away leaving mesh. Therefore, when screen printing solder paste can be printed through these holes.
Screen printing screen and PCB between the screen with a gap of 1~3mm, the scraper will be depressed and PCB contact, then "tear". This action is necessary, otherwise, the solder paste will linger on the screen rather than on the PCB pad.
The application of thick latex screen, its limitations are mainly due to the obstruction of the screen on the opening hole, the obtained silk screen sediment is limited, can not be used for less than 30thou dense interval.
Metal form
Metal stencil is now used on most solder screen printing machines. Its composition is a thin metal plate with holes, solder paste from the print, to solve the problem of irregular sediment in front of the screen printing. It is not required that the screen scraper have pump action, as the solder paste can easily flow through the opening. There is also no requirement for a gap between the template and the PCB.
There are three ways to make metal templates: chemical, laser and electrical.
Chemical corrosion
At present, silk screen printing templates are mainly manufactured in this way. The process is as follows:
A thin copper plate, or more commonly stainless steel plate, is coated with a photosensitive acid-resistant substance on both sides. Positive phototaxis (black pad) templates are stacked on each side and exposed to intense UV light. The exposure area hardens, while the soft pad area can be rinsed off. The plate is then bathed in acid to erode away the desired holes on both sides.
The mutual positioning of positive phototaxis on both sides of the metal plate is critical, especially for elements with close pin spacing. If the stencil is not positioned well, the hole will form a slope, resulting in a bad screen print. The chance of this happening is usually one in ten, but in the past few years, the problem has been very
This was largely solved because improved CAD data and manufacturing techniques reduced the error rate to about one in fifty. A successful technique would make the stencil like an envelope, with an empty plate placed into it, with an accuracy of 2 to 20micron.
The wall of the hole cannot be too flat, because the acid is gradually corroded into the hole, but also into the lateral side of the plate. Form a "figure 8" section.
However, this is usually not a problem because the screen printing template is very thin.
Laser engraving of template
Another technique uses a computer-controlled CO2 or YAG laser to cut wire holes from one side of the plate. It can take about half an hour to carve a stencil. The larger the hole area, the more time and expense it takes. Laser machines cost about $400,000, so the laser is expensive to use, often resulting in a stencil that costs three times as much as chemical etching.
The system is sophisticated, but apart from being expensive, there is another disadvantage: the laser cuts holes in the molten metal, but it also tends to melt the surface of the template, creating a rough surface. Therefore, the surface needs to be sanded or cleaned with chemical methods, leaving a few micron roughness, which looks dull, has a wear effect on the polyester scraper, and makes the stencil difficult to clean, although it is believed that the roughness will help the solder paste "roll".
Electroetched form
Electroerosion formwork currently accounts for about 2~3% of the use. Its manufacturing process is additive. Unlike other processes, the formwork forming method is as follows:
The core plate (substrate) is covered with photosensitive insulating latex and exposed with UV light through negative phototaxis template (transparent pad area, opaque non-screen area). The pad area is hardened and the rest of the area is cleaned off. Then the core plate is immersed in an acidic electrolytic solution and connected to the power supply as a cathode and a dissipative nickel as an anode. After a few hours, the nickel settles in the conducting area (not the pad) and can be torn off like a piece of paper to form a wire hole.
This form has an advantage over other forms. The inner wall of the hole is smooth and can be formed into a trapezoid, which means the bottom is slightly wider than the top and has an Angle of 1 to 2°. This helps the solder paste to pass through the form and onto the PCB. The "tip" of 10~20micron is formed around the bottom of the hole, and a ring of border is formed around the pad. Screen printing helps the solder paste to stay on the pad accurately, and the cost is about 30% higher than that of chemical corrosion.