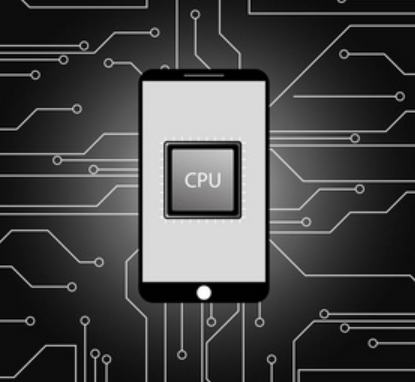
PCB device layout is not a random thing, it has certain rules that need to be followed. In addition to the general requirements, some special devices will also have different layout requirements.
Layout requirements for crimp devices
1) There shall be no components higher than 3mm around the surface of bending/male and bending/female crimping devices, and there shall be no welding devices around 1.5mm; There must be no component within 2.5mm of the pinhole center of the crimping device on the opposite side of the crimping device.
2) There shall be no components 1mm around the straight/male and straight/female crimping devices; For straight/male and straight/female crimping devices, no component shall be placed within 1mm from the edge of the sheath, and no component shall be placed within 2.5mm from the crimping hole when the sheath is not installed.
3) Live plug seat of ground connector used with European connector, long needle front end 6.5mm prohibited cloth, short needle 2.0mm prohibited cloth.
4) The long PIN of the 2mmFB power supply single pin corresponds to the 8mm cloth at the front end of the board socket.
Requirements for the layout of thermal devices
1) During device layout, thermal sensitive devices (such as electrolytic capacitors, crystal oscillators, etc.) should be kept away from high-heat devices as far as possible.
2) The thermal sensitive device should be close to the element under test and away from the high temperature area, so as not to be affected by other thermal equivalent components and cause misoperation.
3) Put the heat and heat resistant devices near the outlet or the top, but if they can not withstand higher temperatures, they should also be placed near the air inlet, and pay attention to other heating devices and heat sensitive devices as far as possible in the direction of air rise staggered position.
Layout requirements with polar devices
1) Polar or directional THD devices have the same direction in layout and are arranged neatly.
2) The polar SMC should have the same direction on the plate as far as possible; Devices of the same type are neatly arranged and beautiful.
(With polar devices including: electrolytic capacitor, tantalum capacitor, diode, etc.)
Layout requirements for through-hole reflow soldering devices
1) For PCB with non-transfer side size larger than 300mm, heavy components should not be arranged in the middle of PCB as far as possible, so as to reduce the influence of the weight of the plug-in component on PCB deformation during welding and the influence of the plug-in component on the devices already placed on the board.
2) For easy insertion, it is recommended that the device be placed near the operation side of insertion.
3) It is recommended that the length direction of a device with a long size (such as a memory socket) be consistent with the transmission direction.
4) The distance between the edge of the through hole reflow device pad and the QFP, SOP, connector and all BGA with the pitch≤0.65mm is greater than 20mm. Distance from other SMT components > 2mm.
5) The distance between the body of the through-hole reflow welding device is > 10mm.
6) The distance between the edge of the pad and the transfer edge of the through-hole reflow welding device is not less than 10mm; Distance from non-transmission edge ≥5mm.
Have you neglected the design of pad in PCB board design?
When designing PCB pad in PCB board design, it is necessary to design strictly in accordance with relevant requirements and standards. Because the design of PCB pad is very important in SMT patch processing, pad design will directly affect the weldability, stability and heat transfer of components, related to the quality of patch processing, so what is the design standard of PCB pad?
1. Design standards for the shape and size of PCB pad:
1. Call PCB standard package library.
2, the minimum single side of the pad is not less than 0.25mm, the maximum diameter of the whole pad is not greater than 3 times the aperture of the component.
3. Try to ensure that the spacing between the edges of the two pads is greater than 0.4mm.
4. The welding pad with aperture exceeding 1.2mm or the diameter of the welding pad exceeding 3.0mm shall be designed as diamond or plum shaped welding pad
5, in the case of dense wiring, it is recommended to use oval and oblong connection disk. The diameter or minimum width of single panel pad is 1.6mm; Double panel of weak current line welding pad only need to add 0.5mm hole diameter can be, welding pad is too large easy to cause unnecessary welding.
Two, PCB pad hole size standard:
The inner hole of the welding disc is generally no less than 0.6mm, because the hole less than 0.6mm is not easy to process when the opening die punching. Under normal circumstances, the diameter of the metal pin plus 0.2mm is used as the diameter of the inner hole of the welding disc. If the diameter of the metal pin of the resistance is 0.5mm, the diameter of the inner hole of the welding disc corresponds to 0.7mm, and the diameter of the welding disc depends on the diameter of the inner hole.
Three, PCB welding pad reliability design points:
1 symmetry, in order to ensure the balance of molten solder surface tension, both ends of the pad must be symmetrical.
2. Pad spacing, too large or too small pad spacing will cause welding defects, so ensure that the component end or pin and pad spacing is appropriate.
3. The remaining size of the pad. The remaining size of the component end or pin after lap with the pad must ensure that the solder joint can form a meniscus.
4. The width of the pad should be basically consistent with the width of the end or pin of the component.
Correct PCB pad design, if there is a small amount of skew during patch processing, can be corrected during reflow welding due to the action of surface tension of the molten solder. If the design of PCB pad is not correct, even if the mounting position is very accurate, welding defects such as component position deviation and suspension bridge will easily appear after flow welding. Therefore, great attention should be paid to the design of PCB pad during PCB design.