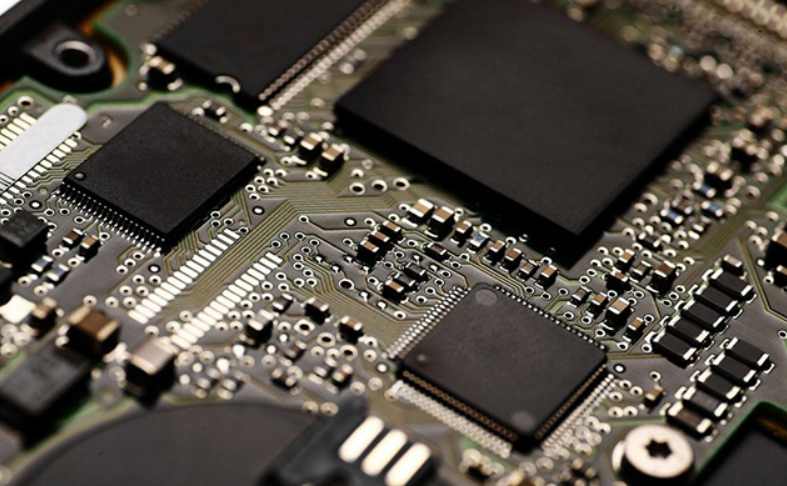
In PCB proofing, temperature sensitive elements can limit the application of reflow soldering, whether in cartridge or SMD. Therefore, selective welding can be used after reflow welding in most applications. This will be an economical and efficient method of welding the remaining inserts and is fully compatible with future lead-free welds. Next, let the professional PCB manufacturers for you detailed printed circuit board selective welding technology.
First, process characteristics
The most obvious difference between the two is that the lower part of the PCB in wave soldering is completely immersed in the liquid solder, whereas in selective welding, only certain areas are in contact with the solder wave.
Selective welding must also be pre-coated with flux before welding; Compared with wave soldering, the flux is only applied to the lower part of the PCB to be welded, rather than the entire printed circuit board.
In addition, selective welding is only applicable to the welding of cartridge components.
Two. Technological process
Selective welding process: flux spraying, PCB preheating, dip welding and drag welding.
1. Flux coating process
Flux coating process plays an important role in selective welding. At the end of welding heating and welding, the flux should be sufficiently active to prevent bridging and prevent PCB oxidation. Flux spraying The PCB is carried by the X/Y manipulator through the flux nozzle, and the flux is sprayed on the PCB to be welded. The flux can be sprayed by single nozzle spray, microporous spray and synchronous multi-point/graphic spray.
The most important thing for microwave peak selective welding after reflow welding process is accurate spraying of flux. Microjet will never stain the area outside the solder joint. The minimum flux spot graphic diameter of micro-dot spraying is greater than 2mm, so the flux position accuracy of spraying deposited on the PCB circuit board is ±0.5mm, in order to ensure that the flux is always covered on the welding site.
2. Preheating process
The main purpose of preheating is not to reduce thermal stress, but to remove the solvent pre-dried flux, so that the flux has the correct viscosity before entering the solder wave. During welding, PCB material thickness, device package specification and flux type determine the setting of preheating temperature.
3. Welding process
There are two kinds of selective welding process: drag welding process and dip welding process.
The drag welding process is done on a single small nozzle solder wave and is suitable for welding in very tight Spaces on PCB. During welding, the PCB moves on the solder wave of the welding nozzle at different speeds and angles to achieve the best welding quality.
To ensure the stability of the welding process, the inner diameter of the welding nozzle is less than 6mm. After the flow direction of the solder solution is determined, the solder nozzle is installed and optimized in different directions for different welding needs.
Compared with the dip welding process, the motion of solder solution and PCB board in the drag welding process makes the thermal conversion efficiency better than the dip welding process. However, the heat required to form the weld connection is transferred by the solder wave, but the solder wave quality of single nozzle is small, only the solder wave temperature is relatively high, to meet the requirements of the drag welding process. Nitrogen is supplied in the welding area to prevent oxidation of solder wave, so as to avoid the generation of bridge defects in the tow welding process. This advantage increases the stability and reliability of the tow welding process.
Single nozzle solder wave drag welding process also has shortcomings: welding time is the longest in the flux spraying, preheating and welding three processes. And because the welding spot is a drag welding, the welding efficiency can not be compared with the traditional wave soldering process. But things are changing, and multiple nozzle designs can maximize production.