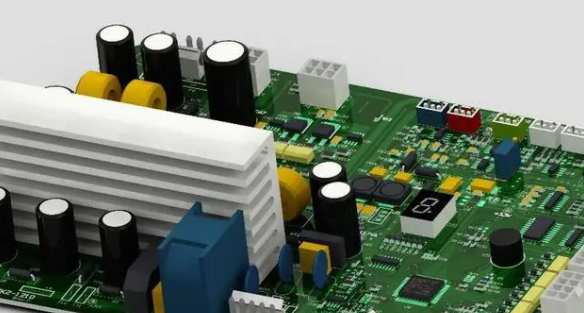
The detection of the first pcba processing means that the first product produced by pcba is inspected in each processing link, so it is also known as the first piece in the industry. The first piece test is an important control point to check the processing quality of the product. Mass production will be carried out only after the first piece meets the requirements of the document. At present, many pcba processing plants use the first-piece detector to judge the first piece. They only need to input the bom, coordinate and digit diagram of the product, and then the system will automatically inspect the first piece of product and check whether the data in the BOM is consistent with the processing. This can reduce the error of manual inspection, save labor costs, improve efficiency and provide customers with high-quality products.
The first piece detection is an effective measure to find the problem as early as possible and prevent the batch errors caused in the process of pcba processing. Through the first piece testing, errors such as mislabeling, missing labeling, multiple labeling and polar materials can be found on the pcba board, so that corrective or improvement measures can be taken to prevent the occurrence of batch nonconforming products. It is a means to control product quality in advance, and is also an essential process for pcba processing plants to ensure product quality and improve production efficiency.
The first detection generally appears in the first online launch of a new product, shift handover, line change, equipment parameter adjustment, and different practices of the same type of pcba. When the quality problem of the first item is found, it should be timely reported and dealt with, and the unqualified item should be confirmed again.
2. Why should the solder paste be stirred, thawed and warmed before SMT patch processing?
Friends working in SMT plant all know that solder paste used for SMT needs to be refrigerated and stored in (2-8℃) freezer. Its purpose is to slow down the reaction speed of flux and tin powder, ensure the welding quality of components and PCB, thus extending the quality of effective welding. Then why should solder paste be stirred and warmed before SMT patch processing? Maybe a lot of friends don't know the real reason.
First, the first step of the solder paste before SMT patch processing is temperature return. The so-called temperature return is also what we often call thawing. The solder paste thawing is self-heating thawing at room temperature, rather than thawing by other heating methods, which needs special attention. If the tin paste is not used in return temperature thawing, it is easy to condense the water vapor in the air and stick to the tin paddle. In the process of reflow welding, the water is heated and quickly vaporized, which is easy to cause the phenomenon of tin blasting and finally produce tin beads.
1, the purpose of thawing back temperature: can make the flux and tin powder evenly distributed, so as to give full play to the various characteristics of the solder paste; The viscosity and activity of the solder paste after refrigeration are different from that of the solder paste at room temperature. The purpose of return temperature is to make the solder paste fully recover the original viscosity and activity;
2. Thawing and reheating method: Remove the solder paste from the refrigerator and place it at the standard room temperature of 22-28℃ for normal thawing. The original packaging of the solder paste should be reheated for at least 4 hours. The second use of the solder paste must be defrosted in 3-4 hours;
Second, followed by solder paste mixing; Because there are various metal components and flux components in the solder paste, because the density of each substance is not the same, the dense metal will sink in the storage process, so the solder paste must be stirred before use after thawing and heating.
1. The purpose of mixing: the purpose of mixing is to make the internal tin powder particles and welding materials stir evenly, increase the fluidity and shaping property, the fluidity and shaping property of the solder paste after mixing will be greatly improved.
2, mixing method: mixing method has two kinds of hand mixing and machine mixing; Stirring time: about 5 minutes clockwise by hand, 3 minutes by machine. Solder paste stirring time should not be too long, too long may lead to solder paste than operating room temperature is higher, in printing flow. The mixing effect can be determined by scraping part of the solder paste with a scraper. When the scraper tilts, if the solder paste can fall smoothly and continuously, the mixing requirements can be met.
Three, solder paste is a very key SMT patch among the auxiliary material, but also affect the SMT patch processing and welding quality of an important process control point, solder paste in use no matter which step is very important. Therefore, we must follow each step above in the actual SMT application.
The above content is provided by SMT SMT factory -kingford- for you. To learn more about SMT SMT processing knowledge, please visit the official website of Shenzhen kingford Co., LTD