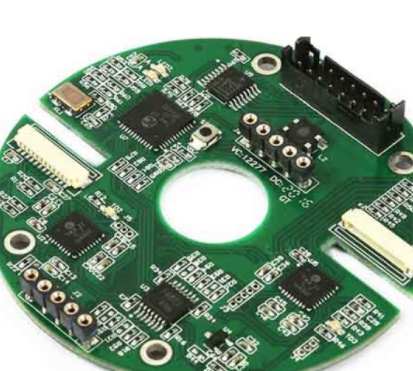
After the PCBA is processed and welded, it has to go through a series of tests, among which the aging test is one of them. The main purpose of the aging test of PCBA board is to simulate the daily use environment of the product through the comprehensive effects of high temperature, low temperature, high and low temperature changes and electric power, and expose the defects of PCBA, such as poor welding, mismatching of component parameters, and faults caused during debugging, so as to eliminate and improve them. It will play the role of stabilizing parameter for PCBA plate without defect. The following is the PCBA processing manufacturer -kingford- to share the PCBA board aging test standards and methods, hope to bring you some help!
I. pcba aging test standards
1, low temperature work
The PCBA board to be aged is placed in a high and low temperature testing instrument at a low temperature of -10±3℃. With rated load 187V and 253V, power on to run all programs, programs remain correct.
2, high temperature work
The PCBA board was placed at 80±3℃/h, and all programs were run on power under this condition with the load of 187V and 253V, and the programs remained correct.
3, high temperature and high humidity work
The PCBA board is run with rated load on power for 48h at the temperature of 65±3℃ and humidity of 90-95%. All procedures should be correct.
Ii. PCBA aging test method
1. Put the PCBA at the ambient temperature into the thermal aging device at the same temperature. The PCBA is running.
2. Reduce the temperature in the equipment to the specified temperature value at a specified rate. When the temperature in the equipment reaches a stable level, the PCBA board shall be exposed to low temperature for 2h.
3. The temperature in the equipment shall be raised to the specified temperature at the specified rate. When the temperature in the equipment reaches a stable level, the PCBA board shall be exposed to high temperature conditions for 2h.
4. Reduce the temperature in the equipment to room temperature at the specified rate, and repeat until the specified aging time, and make a measurement and record of PCBA board according to the specified aging time.
2. How does the SMT patch factory guarantee the PCBA processing quality?
PCBA processing is a multi-process process, each production link is closely linked, any problem in any link will lead to poor welding of PCBA, so how should we ensure the processing quality of PCBA?
First of all, if we want to have a complete SMT processing plant, we must establish a set of perfect ISO quality control system. Each post shall operate according to the operating instructions to avoid the negative influence of human factors to the greatest extent. From raw material procurement to production and processing to final shipment inspection, strict standard control is required, strict implementation of ISO9001:2008 quality management system, and production in accordance with IPC-A-610E electronic assembly acceptance standard. The ISO review agency strictly reviews the company's PCBA production quality control plan, establishes that the production site meets the standards and implements the quality control plan and measures as specified. The audit includes the ability of production operators, production procedures and operation instructions, equipment compliance, raw material selection and warehousing, production documents, production site environment and safe assembly, node Settings in the production process, etc., forming a complete set of operation guidance plan.
1. Procurement and inspection of components
The procurement of components requires strict channel control, purchase from large merchants and original factories, and 100% eliminate second-hand materials and counterfeit materials. Set up special incoming inspection personnel, strictly check the functions of components, to ensure that there are no defects in components.
2. SMT patch processing
SMT paste printing and reflow temperature control of systematic quality control details are key points in PCBA manufacturing. At the same time, for the printing of high-precision circuit boards with special and complex processes, it is necessary to use laser steel mesh according to the specific situation, in order to meet the higher quality requirements, processing requirements of more demanding circuit boards. According to PCB board requirements and customer product characteristics, some parts may need to add U-shaped holes or reduce steel mesh holes. The steel mesh needs to be processed according to the requirements of PCBA processing technology.
3, DIP plug-in after welding
DIP plug-in post welding is the circuit board in the processing stage of the most important, is also at the end of a process. In the process of post welding of DIP plug-in, it is very important to consider the over furnace fixture of over wave soldering. How to use the furnace fixture to greatly improve the yield, reduce even tin, less tin, tin deficiency and other bad welding, and according to the different requirements of customers' products, pcba processing plants must constantly sum up experience in practice, in the process of experience accumulation to achieve technology upgrade.
4. Test and program firing
Manufacturability report is an evaluation work before the whole production after we receive the production contract from the customer. In the early DFM report, we can provide some suggestions to the customer before the processing of PCBA, such as setting some key test points on PCBA(test points). In order to carry out PCBA welding test and subsequent PCBA processing circuit connectivity, connectivity of the key test. When conditions permit, you can communicate with the customer to provide the back-end program, and then through the burner to the PCBA program to the core master IC. In this way, the circuit board can be tested more concisely by touching action, so as to test and inspect the integrity of the whole PCBA and find defective products in time. In addition, many customers looking for PCBA processing one-stop service also have requirements for the back-end testing of PCBA. The content of this test generally includes ICT(circuit test), FCT(functional test), burn test (aging test), temperature and humidity test, drop test, etc.
Quality control is an important step to ensure product quality and production efficiency of SMT plant. Taking reflow welding process as an example, although the temperature control system and temperature sensor in reflow furnace can be used to control the temperature in the furnace, the actual temperature of solder joint on PCBA plate is not necessarily equal to the preset temperature of reflow welding. Although reflow welding works properly, temperature control is also within the temperature control accuracy range of the equipment. However, due to the influence of uncontrollable factors such as the quality of PCBA board, assembly density, PCBA quantity into the furnace, the furnace temperature curve will fluctuate accordingly. Therefore, it is necessary to continuously monitor the temperature of reflow welder to ensure the quality control. Quality control requires technical personnel to have good measurement knowledge, statistical knowledge, causal analysis ability, and in-depth understanding of equipment performance. Production line variability is inevitable. The aging of equipment, the adjustment of personnel, the quality of materials, etc., will affect each other, so that the quality of PCBA processed products fluctuate. Therefore, it is very difficult to adopt an effective and continuous quality control method without affecting production and increasing production cost.
The above is a brief introduction on how to ensure the quality of PCBA processing for SMT patch factory. For more knowledge about PCBA patch processing, please visit Shenzhen kingford Co., LTD