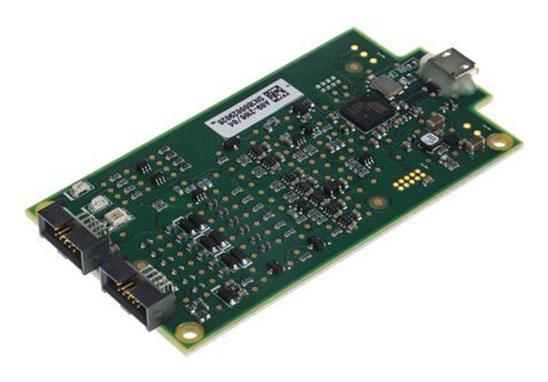
SMT is Surface Mount Technology (short for Surface Mount Technology), is the most popular technology and process in electronic assembly industry.
AOI stands for Automatic Organic Inspection, also known as automatic optical inspection. It uses high-speed and accurate visual processing technology to detect various misassembly and welding defects on PCB.
SPI is the abbreviation of Solder paste Inspection, also known as solder paste inspection. It is the solder paste quality inspection and verification and control of the printing process.
What is the role of AOI and SPI in SMT processing
1, quality control: cover manual detection of some defects, including (original offset, element less tin, solder short circuit, component reverse, component misinstallation, component deformation, component leakage, component erection.)
2. Process control: Generate statistical charts in real time, and feed back information such as fault type and frequency to the production department in real time, so that the production department can timely discover and correct the problems in the production process. As soon as possible to minimize the loss of time and materials.
3, process parameters and other verification: for a new special processing veneer, from the printing process parameters to reflow process parameters, all need to be carefully modulated, the setting of these parameters is reasonable, ultimately depends on the quality of welding, this process must be realized after many tests. AOI provides an effective means of verifying test results.
SPI is used after the printing press for quality inspection of solder printing and validation and control of printing process. SPI plays a significant role in the overall SMT.
And AOI is divided into pre - furnace and post-furnace two kinds, the former for device mounting detection, the latter for welding spot detection. The two functions are different. SPI detects solder paste printing, AOI inspects the stability of cracked parts before the furnace, and inspects welding quality after the furnace.
2. Introduction to common production processes of PCBA proofing processing
Many customers of PCBA proofing processing want to get the products immediately after signing the contract, it is best to drink a cup of tea, and they will keep trying to reduce the delivery time, and frequently urge the salesman. In fact, every process of PCBA proofing processing needs time, and many procedures of PCBA proofing are urgent. So what are the production processes of PCBA proofing processing? Next, Shenzhen PCBA processing manufacturer kingford will introduce you.
PCBA proofing processing common production process introduction
1. Repair:
The function of the repair is to rework the PCBA board that has detected a fault.
2. Mounting:
The function of mounting is to accurately install the surface assembly components to the fixed position of the circuit board.
3. Detection:
The function of testing is to test the SMT welding quality and assembly quality of the assembled circuit board.
4. Curing:
The purpose of curing is to melt the patch glue so that the surface assembly components and the circuit board are firmly glued together.
5. Cleaning:
The purpose of cleaning is to remove welding residues such as flux that are harmful to human body on the assembled circuit board.
6. Solder paste printing:
Solder paste printing machine is used to print solder paste onto the circuit board to prepare for SMT welding of electronic components.
7. Reflow welding:
The function of reflow soldering is to melt the solder paste so that the surface assembly components and the circuit board are firmly glued together.
8. Dispensing:
Dispensing is to drop red glue to the fixed position of the circuit board, its main role is to fix the components to the PCB board. This is an optional process, mainly for the plate with heavy components, the use of red glue process can increase the viscosity.
Shenzhen kingford Co., Ltd. specializes in providing overall PCBA electronic manufacturing services, including upstream electronic components procurement to PCB production and processing, SMT patch processing, DIP plug-in processing, PCBA testing, finished product assembly and other one-stop PCBA OEM services. The company gives full play to its competitive advantages in scale procurement and quality control, and has signed long-term cooperation agreements with many electronic component manufacturers at home and abroad and around the world to ensure the quality and stable supply of raw materials, and transfer the benefits to customers.