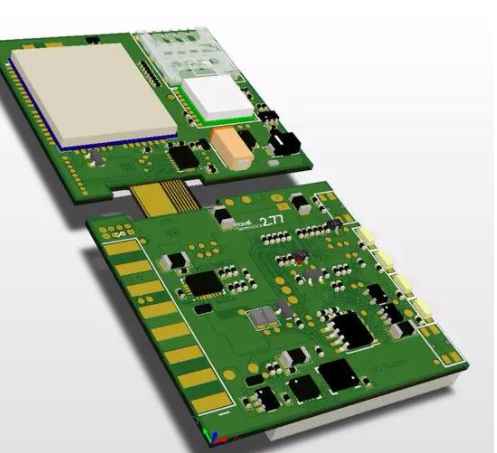
Electronic product research and development enterprises in the PCBA processing plant for SMT proofing or small batch production, often hear start-up costs and engineering costs. SMT patch processing requires fast and efficient production. Generally SMT workshop will carry out non-stop production. Downtime to replace machines will increase production costs and reduce profits. As a result, small orders often charge a start-up fee.
First, SMT proofing small batch processing said that the high charge mainly refers to the loss of time, rather than start-up loss. That is to say, before SMT processing, no matter it is large area SMT processing or small scale SMT processing, the preliminary work needs to be done is the same, such as SMT processing machine programming, PCB positioning, and first part confirmation after startup. In fact, the time in patch processing is very short. Thus, when the amount is smaller, the so-called loss is more time lost. The project cost is the production of documents, the production of steel mesh, equipment debugging, SMT line replacement, etc. Because the order is too small to meet the minimum consumption level, the customer needs to bear the cost of these works.
Ii. With the same time cost, the production efficiency of mass SMT patch processing is higher, and there is no need to waste time on the preliminary work after one morning or one day of production. Sometimes customers take it for granted that a small quantity will lead to a low price. In fact, this is not the case. The preliminary work of mass SMT machining is the same as that of small batch machining. The SMT placement machine programming, PCB positioning and first part confirmation are all the same after starting up. Just debug the placement machine well. So small batch processing will charge engineering fees, or some places called boot fees. Otherwise, the quantity is too small, not enough labor cost and machine loss, and the time in and out is basically wasted. This is the reason why SMT proofing small batch processing cost is high.
2.SMT SMT processing requirements for PCB design components layout
SMT patch processing has requirements for PCB design component layout, and reasonable layout planning will play a role in the process of processing and production. If the layout problem is arbitrary and does not consider the actual processing situation, it will cause certain troubles to the production, and the layout requirements of different processing methods are different.
Component layout requirements for SMT patch processing
1. Replaceable and adjustable components. If you encounter components and parts that need to be replaced or adjusted frequently, you need to consider the characteristics and requirements of the whole machine and place them in a position that is easy to replace.
2. In the mounting process of temperature-sensitive components, if you encounter temperature-sensitive components, you must stay away from heating components, such as audions, integrated circuits, electrolytic capacitors, etc., and stay away from high-power components, radiators and high-power resistors.
3. Arrangement direction. In the actual processing of SMT patches, the arrangement direction of the patch components is also required. Try to keep the same direction and the feature direction should be consistent, so as to facilitate the subsequent installation, welding and detection.
4. Balanced distribution. In the process of reflow soldering, the heat capacity of patch components with higher quality will be larger than that of ordinary components, which will lead to local temperature difference and even virtual welding problems. Maintaining balanced distribution in SMT patch processing can avoid such problems and maintain the balance of the circuit board.
5, heating components, different components contact together, will have an impact on other components, such as heating components, this is generally placed on the corner, ventilation position, conducive to heat dissipation. The heating element must have other leads or supports to support, but also to maintain a certain distance from the printed circuit board surface, the minimum is not less than 2mm, otherwise it will affect the quality of the circuit board.
Why choose Shenzhen kingford for SMT proofing small batch processing?
1. Strength guarantee
▪SMT workshop: We have imported SMT machines and several sets of optical inspection equipment, with a daily output of 4 million. Each process is equipped with QC personnel, who can keep an eye on product quality.
▪DIP production line: We have two wave-soldering machines, among which there are more than 10 old employees who have worked for more than three years. The skilled workers can weld all kinds of plug-in materials.
2. Quality assurance, cost-effective
▪ High-end equipment can stick precision shaped parts, BGA, QFN, 0201 materials. Can also template patch, loose material hand.
▪ Sample and size batch can be produced, proofing from 800 yuan, batch 0.008 yuan/point, no start-up fee.
3. Rich experience in SMT and welding of electronic products, stable delivery
▪ Accumulated SMT SMT processing services for thousands of electronic enterprises, involving many kinds of automotive equipment and industrial control motherboard. The products are often exported to Europe and the United States, and the quality can be affirmed by new and old customers.
▪ On time delivery, normal 3-5 days after complete materials, small batch can also be expedited on the same day shipment.
4. Strong maintenance ability and perfect after-sales service
▪ Experienced maintenance engineers can repair all kinds of patch welding caused by bad products, to ensure the connection rate of each piece of circuit board.
▪ 24-hour customer service staff at any time response, the fastest speed to solve your order problems.