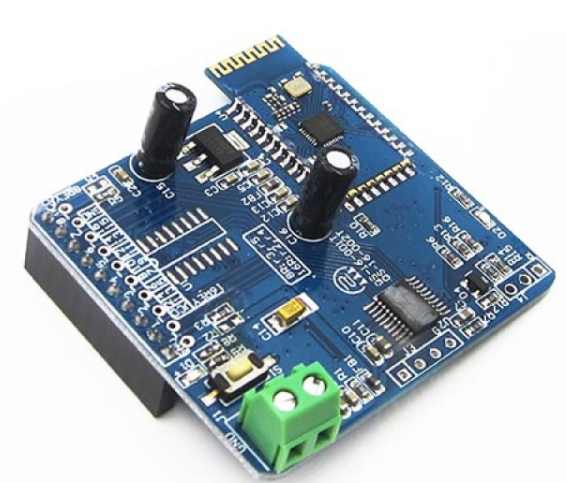
The solder paste connection between adjacent pads is called wet bridge. Sometimes wet bridging will automatically separate during reflow soldering due to the surface tension of solder melting. Failure to separate will result in a short circuit defect.
Cause analysis
1, the solder paste collapse, which is related to the characteristics of the solder paste, such as metal content or the size of the tin ball particle, or the control of the solder paste, such as whether hygroscopic. Of course, it may also be related to printing parameters such as pressure or release speed. Solder paste deposited on PCB solder pad can not effectively maintain the original shape and collapse to form a bridge.
2. The bottom surface of the steel mesh is stained, and there is dirt or other things at the bottom of the steel mesh, which will increase the gap between the PCB and the bottom of the steel mesh when printing, resulting in the solder paste overflow under the steel mesh and lead to the bridge.
3. Excessive pressure causes the solder paste to overflow from the bottom of the steel mesh to form a bridge.
4, the gap is too large, if there is a gap between the steel mesh and the pad, it may lead to the solder paste overflow the pad and form a bridge.
5, the steel mesh is damaged/damaged, the partition between the adjacent holes is broken or deformed, and the solder paste is printed to form a bridge.
6, welding resistance film thickness is not uniform, local areas may be higher than the pad, in the process of fine spacing components solder paste printing, such as 0201 or 0.4mm spacing below the CSP or connector components, there is no solder paste between the adjacent pad partition, solder paste may overflow the pad and form a bridge
7, steel mesh or PCB deviation, steel mesh holes and the pad is not completely aligned, solder paste printing out of the pad, resulting in the solder paste and adjacent pad between the gap decreases, when mounting components, components extrusion solder paste resulting in solder paste and adjacent pad connection, short circuit formation after reflux.
8. Multiple printing, sometimes in order to increase the amount of tin on the pad or increase the solder paste filling of the keyhole element, may be set to two printing, which may lead to excessive extrusion of the solder paste leading to collapse and short circuit.
9, the circuit board is stained, the circuit board is dirty or other things, this principle and the bottom of the steel mesh is stained, the direct cause is to increase the gap between the steel mesh and the pad, the solder paste overflow pad and form short circuit.
2. Improper solder paste covering area for SMT patch processing
Improper solder paste covering area for SMT patch processing
Covering area refers to the surface of the pad need to cover the solder paste area, theoretically the area of this area is equivalent to the steel mesh hole area. But in fact the solder paste cover on the pad may be smaller or larger than the steel mesh holes. When the solder paste coverage area is smaller than the pad may lead to less tin condition; On the contrary may lead to short circuit or tin problems.
1. Improper release of tin paste from steel mesh, printing parameters such as the impact of release speed, may lead to the release of steel mesh, tin paste edge irregular or included in the steel mesh, resulting in solder paste overflow pad or bare pad resulting in short circuit board or less tin problems.
2. In the printing process, the amount of solder paste on the steel net is insufficient, and it is usually necessary to add the solder paste regularly. If the amount of solder paste on the steel net is excessive consumption, the filling of the solder paste in the hole will be reduced, and the solder paste can not completely cover the pad, leading to the occurrence of less tin.
3, tin paste dry, tin paste placed on the steel net for too long, the thinner in the tin paste volatile, tin paste dry, thixotropy is poor, can not fill the mesh well, or tin paste adhesion to the hole wall, the solder paste deposit on the pad less or missing.
4, the bottom of the steel mesh stained, cleaning less than time or incomplete, resulting in the solder paste adhesion at the bottom of the steel mesh and formation of caking, increase the gap between the steel mesh and PCB pad, usually may lead to solder paste volume or coverage increase on the welding fin, of course, may also occur less tin, because these pollutants may instead take away the solder paste on the pad.
5, the solder paste slump couch is excessive, solder paste moisture absorption or other reasons, the edge collapse, solder paste overflow pad.
6. The printing speed is too fast, the solder paste slips on the steel mesh and cannot be fully filled with the steel mesh holes. The solder paste in the holes is not fully filled, and the solder paste deposited on the pad naturally cannot completely cover the pad.
7. Excessive pressure causes the solder paste to leak out from the bottom of the steel mesh and overflow the pad.
Kingford focus on the high-quality PCBA order demand of "Multiple varieties, medium and small batch, and short lead time"