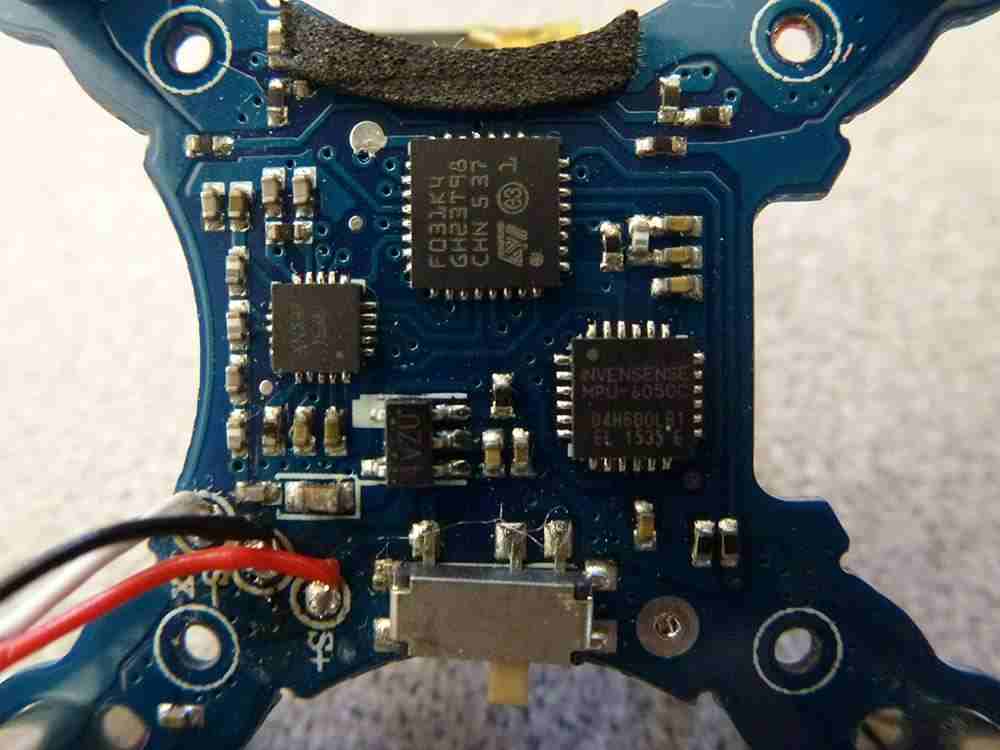
The LDC1000 is an inductor-to-digital converter. Provide low power consumption, small package, low cost solutions. Its SPI interface makes it easy to connect to MCU. LDC1000 only needs to connect a PCB coil board or self-made coil to realize non-contact inductance detection.
LDC1000 inductance detection principle is the use of electromagnetic induction principle. When an alternating current is added to the coil, an alternating magnetic field is generated around the coil. When a metal object enters the field, eddy currents are generated on the surface of the metal object. Eddy current is in the opposite direction of coil current. The eddy current generates an induced electromagnetic field in the opposite direction to that of the coil. The eddy current is related to the permeability of the metal body, the conductivity, the geometry of the coil, the geometry size and the distance between the head coil and the surface of the metal conductor.
A customer asked me if he could use microminiature PCB coils as sensing elements for the LDC1000 inductor-to-digital converter (LDC). The PCB coil has only three turns on each of the four layers of the circuit board, and the coil diameter is 2 mm. The inductance of PCB coil is too low to generate LC resonant loop that oscillates with LDC1000. Due to the limited space of the sensor location, it is recommended to add a fixed series inductor to solve the problem. The inductor-to-digital converter uses an external LC resonant circuit as the sensing element. The resonant loop consists of an inductor with series parasitic resistance and a shunt capacitor.
The oscillation frequency range of the resonant loop is limited by the drive strength of the output driver of the inductor to digital converter. To ensure stable oscillation of the LC resonant loop, the LDC1000 not only requires a sensor oscillation frequency of 5kHz to 5MHz, but also ensures that the resonant equivalent parallel resistance (RP) remains between 798Ω and 3.98MΩ. These boundary conditions can create scenarios where the impedance of the selected sensor is insufficient to design an appropriate LC resonant loop oscillator.
When measuring three-turn and four-layer PCB inductors through a network analyzer, I found that the inductance at the maximum allowable oscillation frequency of 5MHz was 150nH. At this frequency, the series resistance I measured was 0.54Ω.
The formula for calculating the oscillation frequency of LC resonant loop is:
Therefore, a 6.8nF capacitor is needed to reduce the oscillation frequency of the resonant loop to 5MHz. However, the resonant equivalent parallel resistance is calculated by the formula
Display: RP is only 40.8Ω, significantly lower than the minimum of 798Ω required by the LDC1000 resonant loop driver to ensure stable oscillation. The capacitor value cannot be added to the 150nH PCB board coil, so the LC resonant loop that can operate in the sensor and RP boundary conditions of the LDC1000 cannot be generated.
To overcome this problem, I added a fixed series inductor to the sensor inductance. Series inductors can increase sensor impedance without operating at unsupported oscillation frequencies. Suitable fixed series inductors include surface mount (SMD) inductors and multilayer PCB coils. Series inductors should not be used as secondary sensors, so they must be physically isolated from nearby movable conductive materials, or a shielded SMD inductor must be used.
Also note that resolution is affected when using a fixed series inductor because only part of the combination can be used as a sensor (similar to adding a DC offset to the AC signal). Therefore, you need to make the series inductors as small as possible while easily satisfying the boundary conditions of the LDC1000. This will produce the best resolution.
I added a TDK MLZ1608E4R7M multilayer inductor to the 0603 package with a standard inductance of 4.7μH. The measured value of the combined inductance of the sensor and the series fixed inductance at 5MHz is 5.3μH and the combined series resistance is 6.4Ω.
To get some margin, I added a 270pF resonant tank capacitor to produce an oscillation frequency of 4.2MHz. The resonant equivalent parallel resistance of LC resonant groove is 3.1MΩ, completely within the RP range specified by LDC1000.
If your LDC design space is limited, you must use a small sensor coil that supports low inductance, or you need to use a small spring as the sensing element, simply add a fixed series inductor. This will provide LC resonant loop oscillations within the boundary conditions of the LDC.