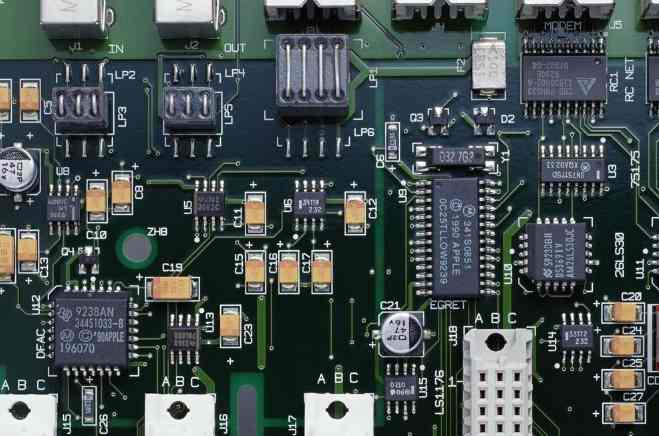
In the era of HDI high density connection technology, the line width and line distance will inevitably become smaller and denser, which results in the emergence of different types of PCB structures, such as through holes and laminated holes on the pad. On this premise, the inner buried holes are usually required to be completely filled and ground flat to increase the wiring area of the outer layer. The market demand not only tests the process capability of PCB manufacturers but also forces raw material suppliers to develop more Hi-Tg, Low CTE, low water absorption, solvent-free, low shrinkage, easy grinding and other characteristics of plug ink to meet the needs of the industry. The main processes of the plugging section include drilling, electroplating, coarsening of the hole wall (pre-plugging treatment), plugging, baking, grinding, etc.
The word plug hole is not a new term for the printed circuit board industry. In the early etching process of the outer circuit, in order to avoid the dry film cover hole is too small at the edge of the PTH hole ring, which can not completely cover the hole and cause the hole wall electroplating to be etched and Open, the plug hole method was used to fill temporary ink to protect the hole wall. After the tin hole process became the mainstream in the market, this method was gradually eliminated; Even so PCB multilayers are required to be solderproof green oil plug holes.
In addition to the wiring area as the main consideration, there is the requirement of uniform thickness of the medium layer. The purpose of the inner plug hole is:
1. Avoid damage to the outer circuit signal.
2. As the base of the superimposed pore structure.
3. Meet the requirements of customer characteristic impedance.
Inner plug mode and capability
Common inner plug hole methods include increased laminating filling hole (can be divided into RCC and HR high adhesive content PP, etc.) and resin plug hole, ink plug hole, generally speaking, if the inner layer is small aperture, low aspect ratio and the number of holes, buried holes can use increased laminating natural filling way plug hole; However, for burials with large aperture, high aspect ratio and many holes, the rubber content of RCC is not enough to fill the holes with large and deep aperture, so it is not suitable to plug holes in this way.
If the amount of glue can not completely fill the buried hole, it will cause the plug hole bubble, sag and insufficient thickness of the medium, and so on, which will also affect the overall reliability of the product. The resin contained in RCC also has a relatively high coefficient of thermal expansion CTE, which is the characteristic of the resin contained in a typical RCC. Too high CTE will cause the cracking or delamination of the filling material in the process of being subjected to heat (such as thermal shock, thermal stress and other reliability tests). The CTE and the bubble with plug hole are the main reasons for the above defects.
The advantages of screen plug hole are:
1. The printing machine has a wide range of uses and can be used in welding prevention and text printing and other processes.
2. The process arrangement is relatively easy for the common plug hole method.
3. Do not need the aperture of the plug hole can be set on the screen stop point to avoid ink.
4. No additional purchase of plug hole equipment, suitable for the industry's existing process.
The disadvantages of screen plug hole are:
1.PCB factory operators need to accumulate considerable operating experience before becoming skilled.
2. Cumbersome and complex operation parameters.
3. It is difficult to apply to the needs of different plug holes in the same inner layer.
4. Each inner plug plate shall be made of a corresponding mesh plate.
5. Poor production efficiency.
Roller scraper hole filling the main investment is the plug hole special machine, its construction method is different from screen printing plug hole, its operation mode is the roller ink filling into the plug hole to carry out the operation; During the operation, the inner plate enters between the two rollers. In the process of moving, the plug plate and the roller located on the bottom of the plug plate produce mutual pressure and pushing effect, forcing the ink roller under the ink roller to fill the ink into the hole aperture. Part of the lower roller is immersed in the ink storage tank, and the operation process can constantly supplement the required plug ink. Finally, as the plug plate continues to move forward, it will pass through the pre-set scraper to remove the excess ink.
The advantages of the roller scraper hole are:
1. The plug plate can be filled quickly.
2. There is no need for printing screen.
3. Fewer process parameters.
4. Easy to get a relatively smooth grinding surface.
The disadvantages of roller scraping and filling holes are:
1. The aperture that does not need to be plugged shall be covered separately.
2. High operational risk (such as sheet card)
3. The amount of ink required for an operation is larger, and the ink needs to have a good operation cycle.
4. There are fewer types of ink to choose from.
Screen printing plug hole and roller scraper filling hole have their own advantages and disadvantages and scope of application, such as screen plug hole because of low production efficiency is suitable for sample or batch number of plug hole plate, in terms of plug hole capacity is suitable for plate thickness thin plug hole plate, and roller scraper filling hole because of high production efficiency is suitable for batch number of plug hole plate, in terms of plug hole capacity is suitable for plate thickness thicker inner plug hole plate.
Inks applied to inner plug holes, whether screen printing plug holes or roller scraping fill holes, should have the following characteristics based on the above considerations:
1. 100% solid content, no solvent is allowed and low CTE is required to prevent cracking or delamination in the process of heating.
2 hardening ink hardness at least in the 6H pencil hardness above.
3. The plug hole shall have a flat surface after grinding, without any depression.
4. There needs to be good adhesion between the copper plated hole wall.
5 hardening ink metallization ability and adhesion need to be quite good.
6. The Tg point should be above 140℃.
7. The CTE below Tg point must be lower than 50 PPM.
8. Easy to grind, after grinding can not leave hole depression.
At present, most of the ink used in the inner plug hole of PCB board on the market, no matter what kind of hardening type, has been changed to the formula without solvent properties. The solvent will be volatilized by heat in the baking process, but if the plug hole aperture is high aspect ratio, the solvent will be relatively difficult to completely discharge and some of the residual solvent will remain in the hole, and the residual solvent will still expand again in the heat process. At this time it is possible to form cracks in the ink phenomenon, especially the combination of high temperature and short time baking and high aspect ratio aperture, easy to occur at the ring ink has hardened and the aperture inside the ink is still not completely hardened film effect, so it is easier to make the solvent residual hole caused by the plug hole; Low temperature baking for a long time can avoid the occurrence of the above situation is also conducive to the discharge of volatile components in the ink, 100% solid content and solvent-free plugging ink, can reduce the shrinkage of residual solvent expansion and hardening after the ink to a minimum degree.