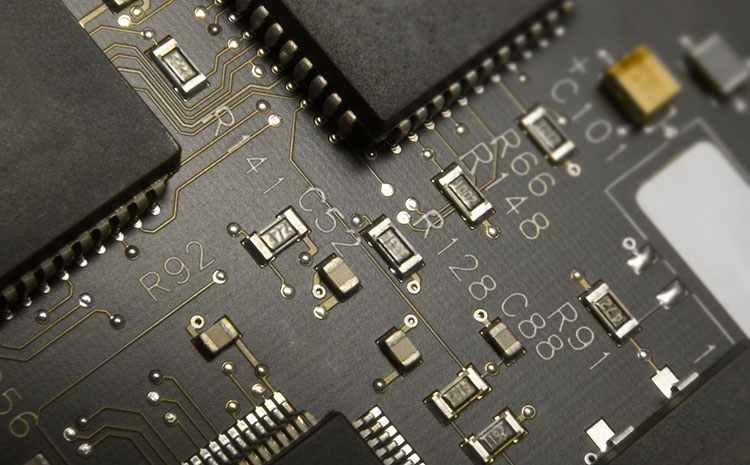
What is surface treatment technology
PCB surface treatment technology refers to the process of artificially forming a layer of surface which is different from the mechanical, physical and chemical properties of the substrate on PCB components and electrical connection points.
The role of surface treatment: Protect exposed copper surfaces and provide weldable surface components to the PCB. Of course, it also has to meet a series of functional criteria, such as environmental requirements, electrical performance, physical performance and durability requirements
Historical evolution of common surface treatments:
The surface treatment process uses a flux to weld components on the copper surface from the beginning, and when the product is required in large quantities, tin-lead plating is used. Hot air solder smoothing (HASL) begins to appear when PCB boards are coated with solder resistance. With the increase of wiring density, organic solderability protective film (OSP) appeared. For clean assembly operations, the ENIG process was widely used, and later came to be environmentally lead-free
Chemical precipitation of silver, chemical precipitation of tin, chemical nickel palladium, chemical nickel silver (ENIAg), etc.
There are two main types of surface treatment processes: metallic and organic.
(1) HASL, ENIG/ENEPIG, gold sinking and tin sinking belong to metal surface forming,
(2) OSP belongs to organic surface forming.
How to choose PCB surface treatment?
PCB surface treatment selection is the most important step in PCB manufacturing because it directly affects process yield, number of reworks, field failure rate, testing capability, reject rate and cost. To ensure high quality and performance of the final product, all important considerations regarding assembly must be taken into account in surface finish selection.
1. PCB surface treatment -- flatness of pad
As mentioned earlier, certain finishes can result in uneven surfaces, which can affect performance, weldability, and other factors. If flatness is an important factor, consider surface finish with thin, even layers. Appropriate options in this case include ENIG, ENEPIG, and OSP.
2. Weldability and wettability
Solderability is always a key factor when using printed circuit board. Certain finishes such as OSP and ENEPIG have been shown to hinder weldability, while others such as HASL are well suited.
3, gold wire or aluminum wire bonding
If your PCB requires gold wire or aluminum wire bonding, it may be limited to ENIG and ENEPIG.
4. Storage conditions
As mentioned earlier, certain finishes (such as OSPs) make PCBS brittle when treated, while others improve durability. Storage and handling requirements should be considered beforehand, and only when risk-free storage and handling requirements can be met should surface treatments that weaken PCBS be used.
5. Welding cycle
How many times will the PCB be welded and reworked? Many finishes are ideal for rework. However, other methods such as tinning are not suitable for rework.
6. RoHS compliance
RoHS compliance is critical when determining the surface finish to use. In general, all surface treatments using lead are not suitable for RoHS compliance and should be avoided.
As described above for each surface finish, some attributes are the most important elements to use as selection criteria. The following table shows the properties that each surface finish has and does not have.
Depending on the specific requirements and characteristics of the PCB product, you can follow this table to select the perfect surface finish option.
In summary, for the type of surface finish you choose, you must choose the best type to accomplish many functions. Each type of surface treatment has its own advantages and disadvantages. There are engineering tricks that can solve problems caused by poor surface finish.