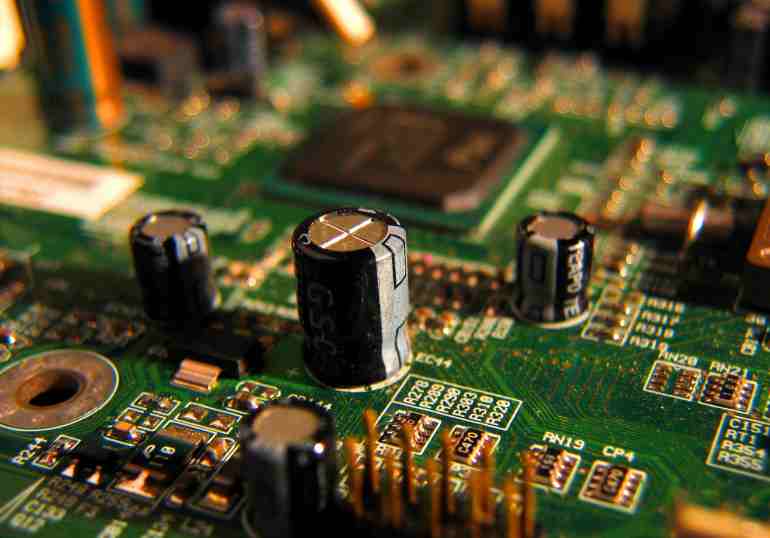
How to improve anti-jamming ability and electromagnetic compatibility when developing electronic products with processor?
1, some of the following systems should pay special attention to anti-electromagnetic interference:
(1) The microcontroller clock frequency is particularly high, the bus cycle is particularly fast system.
(2) The system contains high-power and high-current drive circuit, such as relay generating spark, high-current switch, etc.
(3) System with weak analog signal circuit and high precision A/D conversion circuit.
2. To increase the anti-electromagnetic interference capability of the system, take the following measures:
(1) Select low frequency microcontroller: Select low frequency external clock microcontroller can effectively reduce noise and improve the anti-interference ability of the system. Square wave and sine wave of the same frequency, square wave has much more high frequency component than sine wave. Although the amplitude of the high frequency component of the square wave is smaller than that of the fundamental wave, the higher the frequency, the easier it is to emit as a noise source. The most influential high frequency noise produced by the microcontroller is about 3 times of the clock frequency.
(2) Reduce the distortion in signal transmission: The microcontroller is mainly manufactured by high-speed CMOS technology. The static input current of the signal input terminal is about 1mA, the input capacitance is about 10PF, and the input impedance is quite high. The output terminals of high-speed CMOS circuits have considerable load capacity, that is, quite large output value. If the output end of a gate is led to the input terminal with quite high input impedance through a very long line, the reflection problem is very serious, which will cause signal distortion. Increase system noise. When Tpd > Tr, it becomes a transmission line problem and must consider signal reflection, impedance matching and so on.
The delay time of the signal on the printed boardis related to the characteristic impedance of the lead, that is, the dielectric constant of the printed circuit board material. Roughly speaking, the speed at which a signal travels through a printed board lead is between 1/3 and 1/2 the speed of light. The Tr (standard delay time) of logic telephone components commonly used in systems composed of microcontrollers ranges from 3 to 18ns.
On the printed circuit board, the signal passes through a 7W resistor and a 25cm long lead, with an on-line delay of roughly 4-20ns. That is to say, the shorter the lead of the signal on the printed line, the better, the longest should not exceed 25cm. And the number of holes should be as small as possible, preferably no more than 2.
When the rise time of the signal is faster than the signal delay time, fast electronics processing is required. At this point, impedance matching of the transmission line should be considered. For signal transmission between integrated blocks on a printed circuit board, Td > Trd should be avoided. The larger the printed circuit board, the less fast the system speed. A rule for concluding printed circuit board design is that the delay time of signal transmission on the printed board should not be longer than the nominal delay time of the device used.
(3) Reduce cross interference between signal lines: A step signal with rising time Tr at point A is transmitted to end B through lead AB. The delay time of the signal on line AB is Td. At point D, due to the forward transmission of the signal at point A, the signal reflection after reaching point B and the delay of line AB, a page pulse signal of Tr width will be induced after Td time. At point C, due to the transmission and reflection of the signal on AB, a positive pulse with a width twice the delay time of the signal on AB is induced, that is, 2Td. This is the cross interference between the signals. The intensity of interference signal is related to the di/at of point C signal and the distance between lines. When the two signal lines are not very long, what is seen on AB is actually the superposition of two pulses.
CMOS process of microcontrol by high input impedance, high noise, noise tolerance is also high, digital circuit is superimposed 100~200mv noise does not affect its work. If line AB in the figure is an analog signal, this interference becomes intolerable. If the printed circuit board is a four-layer board, one of which is a large area of ground, or double panels, the opposite side of the signal line is a large area of ground, the cross interference between signals will be smaller. The reason is that the characteristic impedance of the signal line is reduced in a large area, and the reflection of the signal at the D terminal is greatly reduced. The characteristic impedance is inversely proportional to the square of the dielectric constant of the medium between the signal line and the ground and proportional to the natural logarithm of the thickness of the medium. If line AB is an analog signal, a large area of ground must be under the line AB to avoid interference from the digital circuit signal line CD. The distance between line AB and line CD must be two to three times greater than the distance between line AB and ground. Locally shielded ground can be used to cloth the ground wire on both sides of the side lead with a hitch.
(4) Reduce the noise from the power supply: when the power supply provides energy to the system, it also adds its noise to the power supply. The reset line, interrupt line, and other control lines of the microcontroller in the circuit are most susceptible to external noise interference. Strong interference on the grid enters the circuit through the power supply, and even in battery-powered systems, the batteries themselves have high-frequency noise. The analog signal in the analog circuit is more resistant to interference from the power supply.
(5) Pay attention to the high frequency characteristics of printed wire board and components: in the case of high frequency, the lead, through hole, resistor, capacitor, distributed inductance and capacitance of connector on the printed circuit board can not be ignored. The distributed inductance of the capacitor is not negligible, and the distributed capacitance of the inductor is not negligible. The resistance produces a reflection of the high frequency signal, and the distributed capacitance of the lead comes into play. When the length is greater than 1/20 of the wavelength corresponding to the noise frequency, an antenna effect is created, and noise is emitted outward through the lead. The hole of the printed circuit board causes a capacitance of approximately 0.6pf. The packaging material of an integrated circuit itself introduces 2~6pf capacitors. A connector on a circuit board with a distributed inductance of 520nH. A 24-pin IC stand with a double straight spike introduces a distributed inductance of 4~18nH. These small distribution parameters are negligible for the low frequency microcontroller system in this row; Special attention must be paid to high-speed systems.
(6) The component layout should be reasonably divided: the position of the component arrangement on the printed circuit board should fully consider the problem of electromagnetic interference resistance. One of the principles is that the lead between the components should be as short as possible. In the layout, the analog signal part, high-speed digital circuit part, noise source part (such as relay, large current switch, etc.) these three parts should be separated reasonably, so that the signal coupling between each other is minimal. G Handle the ground wire on the printed circuit board, the power cord and ground wire are the most important. To overcome electromagnetic interference, the most important means is grounding.
For double panels, ground layout is particularly exquisite, through the use of single point grounding method, the power and ground are connected to the printed circuit board from both ends of the power supply, a contact of the power supply, a contact of the ground. On the printed circuit board, there should be multiple return ground wires, which will converge to the contact of the return power supply, which is called single point ground. The so-called analog, digital, high-power device to open, refers to the wiring is separated, and finally gathered to the ground point. When connecting to signals other than the printed circuit board, shielded cables are usually used. For high frequency and digital signals, both ends of the shielded cable are grounded. Low frequency analog signal for the shielded cable, one end is better grounded.
Circuits that are very sensitive to noise and interference or circuits that are particularly noisy at high frequencies should be shielded with metal covers.
(7) Use good decoupling capacitors: good high-frequency decoupling capacitors can remove high frequency components up to 1GHZ. Ceramic capacitors or multilayer ceramic capacitors have better high-frequency characteristics. When designing a printed circuit board, a decoupling capacitor is added between the power sources of each integrated circuit. The decoupling capacitor has two functions: on the one hand, it is the energy storage capacitor of the integrated circuit, providing and absorbing the charging and discharging energy of the integrated circuit at the moment of opening and closing the door; On the other hand, the high frequency noise of the device is bypassed. The typical decoupling capacitor of 0.1uf in digital circuits has 5nH distributed inductance, and its parallel resonance frequency is about 7MHz, that is, it has a good decoupling effect on noise below 10MHz, but almost no effect on noise above 40MHz.
The 1uf and 10uf capacitors have a parallel resonant frequency above 20MHz, and the effect of removing high frequency noise is better. It is often advantageous to have a 1uf or 10uf dehigh-frequency capacitor at the point where the power enters the printing plate, which is required even for battery powered systems. A charge-discharge capacitor, or regenerative capacitor, should be added to every 10 pieces of integrated circuit, and the size of the capacitor can be 10uf. It is best not to use electrolytic capacitors, electrolytic capacitors are two layers of thin film rolled up, this rolled up structure at high frequency performance as inductance, the best use of bile capacitors or polycarbonate gestation capacitors.
The value of decoupling capacitance is not strictly selected and can be calculated according to C=1/f. That is, 10MHz is 0.1uf. For the system composed of microcontrollers, 0.1-0.01uF is acceptable.