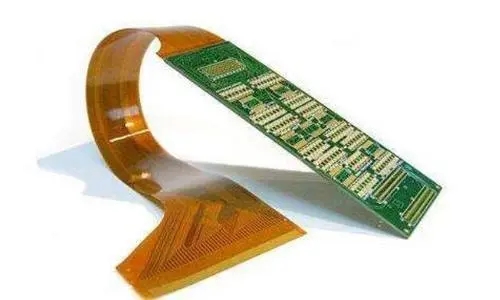
Testing methods for pressing accessories of flexible circuit board (FPC)
PCB manufacturers, PCB designers and PCBA manufacturers will explain the test methods for FPC pressing accessories
1、 Silicon aluminum foil auxiliary material test:
1. Appearance inspection: the surface is smooth and clean, without cracks, cracks, particles, bubbles, pinholes and foreign impurities.
2. Thickness: measure with micrometer, take five points for measurement, read data and record.
3. Size: Measure with a ruler or tape, take equal sides for measurement, read and record the data.
4. Temperature resistance: the silicon aluminum foil shall be continuously heated for temperature resistance test (temperature: 185 ℃; prepressing: 10s; molding time: 120s; pressure: 100kg/cm2 for continuous operation for 5-7 days), and no brittleness is allowed.
5. Silicon oil precipitation: continuously raise the temperature of silicon aluminum foil for temperature resistance test (temperature: 185 ℃; pre pressing: 10s; during forming
Room: 120s; The pressure is 100kg/cm2 for continuous operation for 5-7 days), and no silicon oil is allowed to separate from silicon aluminum foil.
2、 Test of glass fiber cloth accessories:
1. Appearance inspection: the surface is smooth and clean, without wrinkles, cracks, particles and foreign impurities.
2. Thickness: measure with micrometer, take five points for measurement, read data and record.
3. Size: Measure with a ruler or tape, take equal sides for measurement, read and record the data.
4. Temperature resistance: the glass fiber cloth shall be continuously heated for temperature resistance test (temperature: 185 ℃; prepressing: 10s; molding time: 120s; pressure: 100kg/cm2 for continuous operation for 5 to 7 days), and no brittleness is allowed.
3、 Test on auxiliary materials of fired iron plate:
1. Appearance inspection: the surface is smooth and clean, without cracks, cracks, particles, bubbles, pinholes and foreign impurities.
2. Thickness: measure with micrometer, take five points for measurement, read data and record.
3. Size: Measure with a ruler or tape, take equal sides for measurement, read and record the data.
4. Temperature resistance: the sintered iron plate shall be continuously heated for temperature resistance test (temperature: 185 ℃; precompression: 10s; molding time: 120s; pressure: 100kg/cm2 for continuous operation for 5-7 days), and no brittle fracture is allowed.
5. Silicon oil precipitation: continuously raise the temperature of the burned iron plate for temperature resistance test (temperature: 185 ℃; prepressing: 10s; molding time: 120s; pressure: 100kg/cm2 for continuous operation for 5-7 days), and silicon oil precipitation of the burned iron plate is not allowed.
4、 Green silica gel auxiliary material test:
1. Appearance inspection: the surface is smooth and clean, without cracks, cracks, particles, bubbles, pinholes and foreign impurities.
2. Thickness: measure with micrometer, take five points for measurement, read data and record.
3. Size: Measure with a ruler or tape, take equal sides for measurement, read and record the data.
4. Temperature resistance: continuously raise the temperature of green silica gel for temperature resistance test (temperature: 185 ℃; pre pressing: 10s; molding time: 120s; pressure: 100kg/cm2 for continuous operation for 5 to 7 days), and no brittleness is allowed.
5. Silicone oil precipitation: continuously raise the temperature of green silica gel for temperature resistance test (temperature: 185 ℃; prepressing: 10s; molding time: 120s; pressure: 100kg/cm2 for continuous operation for 5-7 days), and no green silica gel silicone oil precipitation is allowed.
5、 Tpx auxiliary material test:
1. Appearance inspection: the surface is smooth and clean, without wrinkles, cracks, particles and foreign impurities.
2. Thickness: measure with micrometer, take five points for measurement, read data and record.
3. Size: Measure with a ruler or tape, take equal sides for measurement, read and record the data.
4. Temperature resistance: TPX shall be continuously heated for temperature resistance test (temperature: 200 ℃; prepressing: 10s; molding time: 180s; pressure: 120kg/cm2 for 10~20 consecutive operations), and no brittleness is allowed.
5. Silicone oil precipitation: press the copper foil with the sample tpx (temperature: 180 ℃; preheating time: 10s; molding time: 180s; pressure: 100kg/cm2), press it for 10~20 times continuously, and then conduct nickel plating test after pretreatment. After nickel plating, observe with a 10x magnifying glass, and no copper exposure is allowed.
6、 Test of release film auxiliary materials:
1. Appearance inspection: the surface is smooth and clean, without cracks, cracks, particles, bubbles, pinholes and foreign impurities.
2. Thickness: measure with micrometer, take five points for measurement, read data and record.
3. Size: Measure with a ruler or tape, take equal sides for measurement, read and record the data.
4. Temperature resistance: the release film shall be continuously heated for temperature resistance test (temperature: 200 ℃; prepressing: 10s; molding time: 180s; pressure: 120kg/cm2 for 5~10 consecutive operations), and no brittleness is allowed.
5. Silicon oil precipitation: press the copper foil and the sample release film (temperature: 180 ℃; preheating time: 10s; molding time: 180s; pressure: 100kg/cm2), press for 3 to 5 times continuously, and then conduct nickel plating test after pretreatment. After nickel plating, observe with a 10x magnifying glass, and no copper exposure is allowed.
7、 High temperature resistant tape auxiliary material test:
1. Appearance inspection: the surface is smooth and clean, without cracks, cracks, particles, bubbles, pinholes and foreign impurities.
2. Thickness: measure with micrometer, take five points for measurement, read data and record.
3. Size: Measure with a ruler or tape, take equal sides for measurement, read and record the data.
4. Temperature resistance: the high temperature resistant tape shall be continuously heated for temperature resistance test (temperature: 200 ℃; prepressing: 10s; molding time: 180s; pressure: 120kg/cm2 for 10~20 consecutive operations), and no brittleness is allowed. PCB manufacturers, PCB designers and PCBA manufacturers will explain the testing methods for FPC pressing accessories