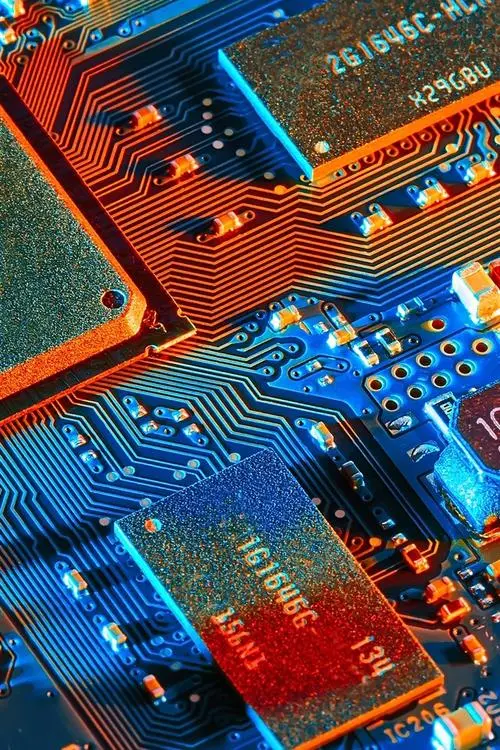
preface
PCB electroplating process management is an important link in electroplating production. Its determination is obtained by electroplating workers after tens of millions of times of repeated tests and research. Therefore, PCB electroplating process is highly scientific. The determination of PCB process should not only consider the deposition rate of the coating, the current efficiency of the cathode and anode, the balance of metal ion dissolution and deposition, but also consider the stability of pH value, the wide range of temperature and current density, as well as the light output rate, leveling performance, bright range and other aspects. Therefore, we must attach great importance to various technical parameters specified in the process, so as to ensure a good coating. The author puts forward the following opinions on how to strengthen the management of electroplating process.
Process management
1.1 Pretreatment
The pretreatment of PCB electroplating is the basis of electroplating quality. If the pretreatment is not good, the coating is not hairiness, or bubbles, shelling, or even both, resulting in the scrapping of defective products. The pretreatment of electroplating is mainly to remove oil stain, oxide skin, rust, etc. on the plated parts. This not only ensures the good adhesion between the substrate and the coating, but also speeds up the deposition rate of the coating. At the same time, it ensures that the plating solution will not be polluted due to the oil contamination of the plating piece and the introduction of foreign metal impurities.
If there is a galvanization factory, after galvanization, it is found that there are serious blisters and burrs on the coating, so it repeatedly adjusts the plating solution, and the problem cannot be solved. As a result, an old master found that there was a layer of similar colloidal substances on the surface of the workpiece before entering the groove. It was originally caused by the rubber inside the container containing concentrated sulfuric acid dissolved and stuck to the surface of the workpiece, which could not be cleaned. Therefore, the author suggests that the oil and rust must be removed according to the process regulations, and the surface state of the workpiece must be observed. The pretreatment includes ultrasonic degreasing, chemical degreasing, cathodic and anodic electrolytic degreasing, acid pickling to remove oxide scale and rust. It is necessary to regularly analyze the composition of the degreasing and rust remover fluid, and regularly feed materials. The alkali tank should be filtered regularly, and the acid tank should be regularly discharged and renewed. The degreasing and derusting solutions are kept in good condition to ensure the quality of the coating.
1.2 Detection and management of bath composition
1.2.1 Laboratory analysis
It is a more scientific management method to regularly test the content of bath components and adjust them in time. The test scale can be large or small. For pure plating seed manufacturers, only a few simple test equipment and a small amount of investment are required. Personnel can work part-time and can be trained to operate.
1.2.2 Specific gravity method
Measure with Baume specific gravity method. This method is only applicable to solutions with relatively simple bath composition. For example, chromium plating is dominated by chromic acid, and sulfuric acid accounts for only about 1%, which can be ignored. This method is also applicable to pre-treatment acid (hydrochloric acid or sulfuric acid), as well as various activated acid, which can also be referred to by Baume degree.
1.2.3 Explore laws and accumulate experience
Take less and more measures to gradually explore the law of consumption and loss to supplement, so as to make the composition relatively stable and accumulate some experience. However, this method is not scientific enough and is mainly controlled by experience.
1.2.4 Precautions in PCB process management
(1) To manage the process well, in addition to carefully controlling the content of ingredients, attention should also be paid to the water quality of the one-time preparation tank, as well as to prevent the wrong addition and wrong addition of chemical raw materials. The author once encountered that thiourea was wrongly added to the nickel plating bath as boric acid, resulting in blackening of the coating. Later, more hydrogen peroxide and activated carbon were added, and it gradually became normal after large treatment. Therefore, the author suggests that when adding chemical raw materials to the plating solution, "first look, second check and third add" should be carried out to avoid unnecessary loss.
The removal of chloride ions in bright copper acid solution can be carried out by using the silver salt method, that is, the calculated amount of silver nitrate (5 parts of silver nitrate are required to remove 1 part of chloride) is dissolved in distilled water, and then the sodium carbonate is dissolved in distilled water. The sodium carbonate solution is gradually added to the silver nitrate solution under stirring, and then it is stopped when it becomes alkaline. Then it is rinsed several times with distilled water, and the precipitate is silver carbonate. Ag2CO3+2HCl=2AgCl+H2O+CO2 is added to the acid copper solution under stirring. Filter it. This method is good, but it is expensive, so it is seldom used in production. The zinc powder method can also be used to remove chlorine, with low cost, but the treatment essentials must be paid attention to. First, use 1~3gL of water to make a paste of analytical pure zinc powder. After gradually stirring, add it to the copper acid solution. After adding it and standing for 0.5h (copper acid solution does not need to be heated), add 1.5~2.0gL of powdered activated carbon, stir it evenly, standing for 0.5~1.0h, and filter it. The author told one unit that added hydrochloric acid by mistake, and the other unit that used township tap water to prepare tanks. The former had a good effect, while the latter had no effect due to overnight precipitation and re filtration.
(2) In order to ensure the stability of the bath, be careful not to bring foreign metal impurities into the bath. The author suggests that for nickel plated products on copper, the nickel plating solution must be periodically electrolyzed with corrugated iron plates with a current density of about 0.05A dm2, or copper remover must be added to ensure the brightness of the low current density area. In addition, parts falling into nickel plating bath or acid copper plating bath shall be taken out in time to prevent accumulation of impurities. For the falling of copper and zinc alloy parts, it is recommended to make a flat screen slightly wider than the bottom of the slot with window screens, and fasten the four corners with plastic tubes (rods). When off duty, four plastic rods should be lifted to take out the falling copper and zinc alloy parts, so as to avoid or reduce the accumulation of copper and zinc impurities in the nickel plating solution, thus reducing the plating solution failure. (3) The insulation of the hanger is incomplete or bubbling, which makes the chrome plating solution not clean, causing the chrome plating solution to be carried into the cyanide copper plating solution or nickel plating solution, polluting the plating solution and causing failures. Therefore, it is required that the hanger insulation must be intact. For the hanger hanging to the bottom of the automatic line, the workpiece shall be hung after chromium removal to avoid chromium contamination of the plating solution.
1.3 Operating conditions
1.3.1 Temperature and current density
In practical operation, it is very important to select the best temperature for the quality and stability of electroplating. It is an important measure to ensure PCB quality to select the best temperature according to various workpieces and strictly control it. The temperature is generally proportional to the cathode current density. With high temperature (within the process range), the cathodic current density can be increased, the coating is fine, and the deposition rate is fast.
1.3.2 Conductive contact
Conductive contact generally refers to the contact between the hanger and the pole, the contact between the anode hook and the pole, the contact between the pole and the copper ingot, and the contact between the copper bar and the copper ingot. Each conductive contact point needs to maintain the color of copper, which reduces the resistance or reduces the non-conductive due to poor local contact, thus affecting the quality of the plated parts. The author suggests that conductive contact parts should be brushed frequently to keep them clean.
1.3.3 Cathode movement and stirring
The purpose of cathode moving and stirring is to accelerate the convection and diffusion of ions, increase the cathodic current density, improve the uniformity of the coating, and facilitate the release of hydrogen. If the cathode moving stroke or frequency fails to meet the requirements, gas tumors or streaks may occur when plating large flat workpieces. The travel of cathode movement must be controlled at about 10cm, with a frequency of 15 times per minute. In addition to the above functions, air agitation can also reduce the production of univalent copper for bright copper acid solution, but air agitation must be combined with continuous filtration. Its continuous filtration shall not be less than 5~10 cycles per hour, otherwise it is easy to produce burrs.
2. Quality management
PCB electroplating enterprises should implement modern quality management. To do a good job in quality management, the first thing is to establish a quality management system in accordance with GBT19000-ISO9000 quality management standards. To this end, it is necessary to establish electroplating quality standards, including the quality requirements for each process, such as sanding, degreasing, acid etching, and other process quality standards. At the same time, it is necessary to establish the corresponding inspection system, such as the inspection method of finished products, whether to inspect one by one or sampling inspection. Formulate standards and strengthen inspection to prevent unqualified plated parts from leaving the factory, prevent unqualified plated parts from flowing into the next process between processes, block the occurrence of batch defective products, and eliminate defective products in the production process, so as to ensure quality and improve the rate of authentic products. Therefore, the author suggests strengthening the basic work of modern quality management.
3. Control the quality of raw materials
When PCB enterprises purchase metal and chemical raw materials, they pay more attention to their quality while paying attention to the price. The author believes that both price and quality should be considered. If only considering the price, it will cause instability of the plating solution and many failures, and finally the electroplating enterprise will suffer losses. For example, some zinc ingots have poor quality, lead impurities exceed the standard, the coating quality is unstable, and failures are frequent. The author believes that both price factors and the importance of raw material quality should be considered when purchasing raw materials. The price and quality cannot be neglected. Only by focusing on the quality of PCB raw materials and equipped with a modern quality management system can PCB enterprises achieve good economic benefits