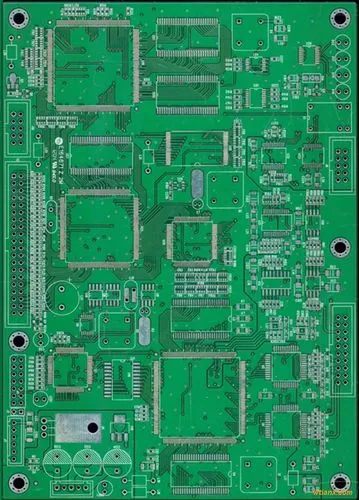
PCB engineering change (ECO) will drive up the design cost, resulting in a large number of delays in PCB product development, thus delaying the time to market. However, most ECOs can be circumvented by seriously thinking about the seven key areas where problems often occur. These seven areas are: component selection, memory, humidity sensitivity level (MSL), design for testability (DFT), cooling technology, radiator and coefficient of thermal expansion (CTE).
1、 Component selection
To avoid ECO, it is important to read the component specifications thoroughly. PCB designers routinely check the electrical and engineering data of components, as well as product life and usability. However, when the components are in the early stage of market promotion, the data manual may not have all the key indicators. If the components have been on the market for only a few months, or only a small batch of samples can be provided, the reliability data currently available may not be universal or detailed enough. For example, in the end, it may not be possible to provide enough reliability data or quality assurance data on site failure rate.
Don't believe the superficial articles in the specification are very important, but actively contact the component suppliers to learn as much as possible about the characteristics of components and how to apply these characteristics to the design.
A good example is the maximum expected current or voltage that a component needs to handle. If the selected element cannot handle enough current or voltage, the element is likely to burn out.
At present, there is no IPC standard for holes specifically related to LGA devices. At present, in some cases, LGA devices with the highest void level of 30% are considered reliable. In general, however, a lower void level of up to 25% is better, and 20% is better.
In the absence of empty data, design engineers must rely on their experience, skills and common sense, and use components that will not stop production immediately, can be obtained from multiple channels, and are easy to find in the market to carry out their design.
It is also important to perform additional analysis and calculation during component selection, such as calculating the current or voltage at peak performance. A component may specify the performance index at a certain peak temperature and current value. However, for a particular design, the PCB designer must take action to ensure that he or she does these critical calculations himself or herself.
The engineer shall not only be responsible for calculating a single component, but also consider the relationship between the component and other components used in a specific design. For example, this calculation is particularly important for analog components with high heat output. For example, many analog components are placed on the same side of the circuit board and next to each other. These components will generate considerable power, so the heat generated will be much higher than the other side of the circuit board (digital components naturally). In this case, the solder mask may peel off on the side full of the simulator.
The analog part of the component circuit will generate a lot of heat. Overheating may lead to stripping of the solder mask, and in the worst case, components may be burned.
Design and layout engineers need to cooperate in the layout of components in the layout design stage to avoid components being too close to the edge of the circuit board, or too close to other components, so as to avoid not leaving enough space between them. It is easy to design component layout on the computer, but if component packaging is not accurately created in the layout, the mounter may not be able to perfectly place these components next to each other. For example, Figure 4 shows that the components protrude slightly from the circuit board.
2、 Memory
The same principle applies to memory selection. As a new generation of more advanced DRAM and flash memory are constantly on the market, PCB designers have a very challenging task if they want to stay at the forefront of technology and judge how changing memory specifications affect updated design in a timely and accurate manner.
PCB designers need to pay attention to the rise of DDR4 at any time and keep close cooperation with OEM customers, because they are likely to include DDR4 DRAM when they launch the next generation of embedded systems. They must have a good grasp of new features and functional dynamics to avoid the satisfaction of design and the resulting engineering change order. Another thing to note is that memory prices fluctuate.
3、 Humidity sensitivity level (MSL)
Humidity sensitivity level (MSL) is easily ignored. If OEMs ignore MSL in their design and key MSL specifications are not treated correctly, users may not consider MSL information, and circuits may not work properly when they are used in the field. This possibility is higher when the actual MSL level is 3, 4 or 5. In this case, baking may not be completed correctly, and moisture may enter through the void, resulting in an engineering change order. When LGA is involved, PCB assembly companies will have to replace these packages on PCBs.
4、 Design for testability
Design for Testability (DFT) is very important for PCB testing and debugging in the production process. When placing components on the circuit board, it is important to pay close attention to the layout position of DFT detection points and the angle when the probe extends to contact vias, pads and other test points.
At the early stage of the initial design, before DFT was allowed, testing became a big problem, and ECO came into being. In some extreme cases, if ECO cannot solve the problem, it needs to be redesigned to solve the problem.
5、 Cooling, radiator and thermal expansion coefficient
Cooling methods are easy to be ignored in PCB design, but ECO can often be avoided by carefully evaluating cooling requirements in the early stage of design.
Some types of cooling are water cooling. For example, most large dedicated computer boards containing a large number of BGAs and microprocessors for data intensive applications (such as animation, image or video processing) require water cooling.
When using heat sinks, PCBs or heating devices are usually connected to the chassis to dissipate heat to the surrounding environment. In many cases, the radiator shown in Figure 6 is also used to help dissipate heat. If the correct radiator is not specified, an engineering change order may be generated. This engineering change order must be developed and introduced in order to successfully heat the radiator.
PCB designers need to ensure that components match the coefficient of thermal expansion (CTE) in terms of thermal performance, and have carried out all relevant calculations. He must ensure that not only the components and their package sizes match each other, but also the PCB materials (such as FR4, Rogers or Teflon), to avoid generating a lot of heat, or generating the difference in thermal expansion coefficient between the components and the circuit board.