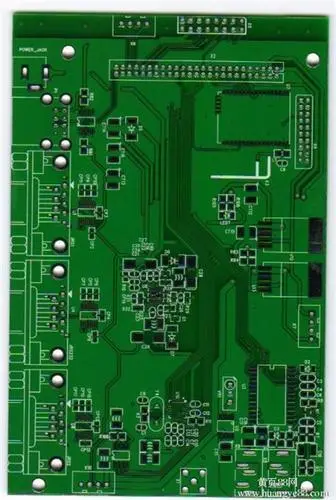
1、 High end PCB drilling and milling machine control system architecture
1.1 System structure description
T he PCB control systePCB control m adopts the structure of upper computer+lower computer+network I/O interface module. Because data communication is realized with the lower computer through gigabit Ethernet, there is no special requirement for the upper computer. Industrial personal computers, ordinary PCs and even laptops can be selected according to the working conditions. The lower computer realizes real-time motion control, I/O management and fault monitoring. The special motion controller connects the driver through the shaft interface, outputs analog signals, collects encoder/grating ruler feedback signals, and realizes closed-loop servo control, limit management, origin, drive alarm, reset, brake alarm and other signals. This part is related to the final speed accuracy and other key indicators. The independent controller of Gugao Company in China or the famous PMAC motion control card of DELTA TAU in the United States can be selected. The field network I/O expansion module realizes tool break detection, tool detection and auxiliary input and output functions.
1.2 Software function module
The NC program is also divided into upper and lower parts correspondingly. The upper program realizes human-computer interaction functions such as parameter setting, file input and conversion, graphics and image processing, and on-site monitoring. After the completion of the interpretation of processing files and the formation of processing instructions and tool instruction data, the main processing thread is opened to send the data to the lower program. The lower motion control main program completes the functions of shaft control and I/O management that require high real-time performance; The detection thread runs in the idle period of the CPU, monitors and diagnoses the system status, and displays the system status on the operation interface immediately.
The contents of the above two parts mainly describe the technical route of the conventional software and hardware for building the system, which is far from enough. In order to truly build and develop a high-grade control system and hope that it can compete with the top level controllers abroad, we still need to make great efforts in the control and client human-computer interface.
2、 Key technologies in control
The final overall effectiveness of the current domestic system is inferior to that of the imported system, which is largely caused by the following factors. To overcome these shortcomings, it is necessary to choose a powerful motion control card. The PMAC card of DELTA TAU is undoubtedly one of the best choices. The key functions it provides just meet the needs of building high-end PCB systems.
2.1 Selection of control mode
The traditional domestic equipment manufacturers all adopt the position control mode in low-end equipment. This is a way to accurately control the stepping motor or the servo motor working in the position mode by using the PCB board card channel to send pulses. Its response speed and closed loop characteristics are very poor, even not a real closed loop, so that the potential of the mechanical system cannot be brought into play. Later, with the gradual popularity of the speed control mode, the dynamic characteristics of the motor control have been greatly improved, and the real closed-loop control has also been achieved. The speed and accuracy of the machine tool have reached a higher level. These two motor control modes are the mainstream choices of domestic equipment manufacturers at present.
The torque and direct PWM control of motor are widely used by European and American manufacturers, and the application in China is basically blank. These two control methods completely reject the low response characteristics of position mode, and overcome the uncertainty caused by the lengthy steps of speed mode when debugging PID parameters. As the torque and direct PWM control mode are simpler and more direct in the control model, the speed loop and current loop are transferred to the control card side, which will lead to higher responsiveness, and at the same time, the response speed of the feedback link is also improved to a certain extent, so the combined force of the two will produce higher performance. Unfortunately, up to now, the domestic motion controller cannot support the above two advanced control modes, which limits the development of the domestic system to a certain extent.
2.2 System identification technology
At present, the domestic PCB manufacturers do not have enough knowledge about the connection between the servo system and the mechanical system, so even though they have selected excellent components to build the mechanical system, they still cannot obtain ideal control effect. That is, because the understanding of system identification is very vague, they cannot coordinate the relationship between the controller and the controlled object most effectively. If you want to develop a high-end controller, you should improve the tracking speed of the servo system as much as possible. The greater the bandwidth, the better the rapidity. The bandwidth of the servo system is mainly limited by the inertia of the control object and the actuator. The greater the inertia, the narrower the bandwidth. The advanced controller has the ability to automatically diagnose the bandwidth of the system, and then can selectively support low-pass filters or notch filters to avoid the natural frequency (resonance point) of the machine tool. To a certain extent, it can explore the potential of the machine tool as much as possible and avoid the damage to the machine tool caused by the machine vibration excited by high-speed movement.
2.3 Interference suppression and prevention
The influence of electromagnetic interference on the final machining accuracy of the machine tool is also fatal. In addition to taking active measures to suppress interference in circuit layout, shielding, grounding, etc., effective prevention after interference is also very important. However, most controllers do not have this function at present. High end motion controllers, such as PMAC, can judge whether the signal entering the controller comparison link is perfect or not by hardware monitoring whether the phase difference between the rising edge of A and B phases fed back by the encoder or grating ruler is normal. If any abnormality is found, an alarm will be given immediately to prompt the operator to eliminate the interference immediately to avoid machine tool deviation.
2.4 Independent operation of controller
In the past, most motion control cards were inserted into the ISA or PCI slot of the host computer. The interface form of a single fixed golden finger was not suitable for long-term work in harsh working environments, especially when the machine vibrated violently, communication interruption would occur, which would affect the stability of the system. Therefore, the independent operation of the controller was required. The method of network communication is used to effectively solve this problem. At the same time, the problem of common ground between the control system and the PC is avoided, so that the interference signal will not go to the computer to affect the normal operation of the main control program, and the stability is enhanced.
The independent operation of the controller also makes it possible to realize the networked control of machine tools, and the concept of an unmanned chemical plant is no longer remote. Once the network is connected and master control is obtained, any computer in the network segment can control and monitor the machine. Similarly, a computer can also control multiple machine tools, with great flexibility.
3、 Optimization of client graphical control interface
At present, some directors of PCB manufacturers have a misconception that as long as the functions can be realized, other requirements can be discounted. This kind of thought has directly led to the situation that China has not been able to develop a high-level control system so far. This overall backwardness is not only in the field of PCB drilling and milling, but also in the field of metal processing machine tools, and even in the entire industrial control field. In order to improve this situation, the author believes that the following aspects are crucial.
3.1 Application of software engineering ideas
At present, PCB industry control products are limited in the implementation and application of software engineering ideas, seriously lagging behind the management, finance, games and communication industries. On the one hand, the reason is that most programmers in the field of industrial control are mechanical or craft students, and their understanding of programming language and computer technology is relatively rough, and most of the software they write stays at a relatively primary level; On the other hand, engineers who master advanced programming technology are often vague about the concepts of hardware and control, and can't realize the technological process and human-computer interaction interface with perfect programming language. The fundamental solution to this contradiction is to implement the idea of software engineering in the process of industrial development, and use the model of developing large and medium-sized software systems in other fields for reference to form a reasonable team. The planners are experts in the industry, and the implementers are experts in computer programming. Only in this way can we make high-quality products, compete with foreign systems, and ensure that the software has good scalability and maintainability.
3.2 Application of database technology
At present, when saving data, machine configuration and a lot of working condition information, the domestic NC system software mostly adopts the format of text file or INF file, and its content cannot be effectively retrieved and managed when the amount of data is large. In order to achieve more complex interface configuration, dynamically add users, switch languages, classify and time share management of knife break information and operation information, and simple text access can no longer meet the requirements, so how to use small databases to organize and manage data has become a topic. The author adopts ACCESS database to manage and control the database through the interface of DAO350, so as to realize the dynamic management of a large amount of data and completely solve the inconvenience caused by data management with binary or ASCII files. Therefore, whether these advanced computer technologies can be effectively used is also one of the bases for judging the advantages and disadvantages of a system.
3.3 Cross hardware platform architecture
At present, there are many machine tool equipment manufacturers in China, which are generally divided into the Sichuan system and the coastal system. The Sichuan system started early but its technology has developed independently, which is relatively backward. Direct air landing of the coastal first series and imitation of foreign technology are in step with the international comparison. However, no matter where they are, equipment manufacturers will subdivide the PCB product market according to the different needs of customer groups, some for the low-end market, and some for the high-end market. Because the requirements for machine speed and accuracy are different, the selection of motion control components is also different. In order to meet the different needs of various manufacturers, it is necessary to design the control system as a universal system across mainstream hardware platforms.
3.4 Beautiful interface and realization of complex and intelligent functions
Many developers [The beauty and layout of the PCB industry are not given enough attention, but when comparing the self-developed system interface with the CNC84 system of SIEB&MEYER at large industry exhibitions, it is found that they are not at the same level at all. In addition, foreign systems are generally highly intelligent, such as the record management of tool breaking information and operation information, the overall consideration of 64 cases of any combination of 8 file quadrants and 8 mechanical quadrants, and the tool diameter detection is And the light point compensation function, various ways of manipulator knife, and so on. Because of various reasons, domestic system developers can not achieve such complete functions, so they can never compete with foreign systems. The reasons are still due to incomplete planning and lack of experience in developing large-scale software. The beauty of the interface and the intelligence of various functions are also important manifestations of the strength of developers.
4、 Conclusion
Through nearly 20 years of continuous technological breakthrough and market cultivation, China has created a number of PCB numerical control manufacturers, opened up the situation in the middle and low end market, and formed a certain market scale; However, in the technology intensive middle and high-end controller market, the scale of domestic controllers has never made a good breakthrough, the profit space has been squeezed, and the R&D system cannot support sustainable technological progress. In order to break through this situation, the author avoided international giants such as FANUC and SIEMENS in the metal processing field, chose PCB drilling and milling, which is a slightly remote field, deeply investigated the technology and market status of the controller in this field, and gave the technical route for building high-end controllers. After that, we made targeted technical breakthroughs from the core control technology and human-computer interface, carefully deployed them from the software and hardware levels, and effectively developed a set of CNC systems with high standards in various technical indicators and even appearance control, not only achieving fast, accurate, stable, but also beautiful and convenient, catching up with similar foreign PCB products in an all-round way. At the same time, we hope to find out a set of models to break the deadlock, which can be used for reference by peers.