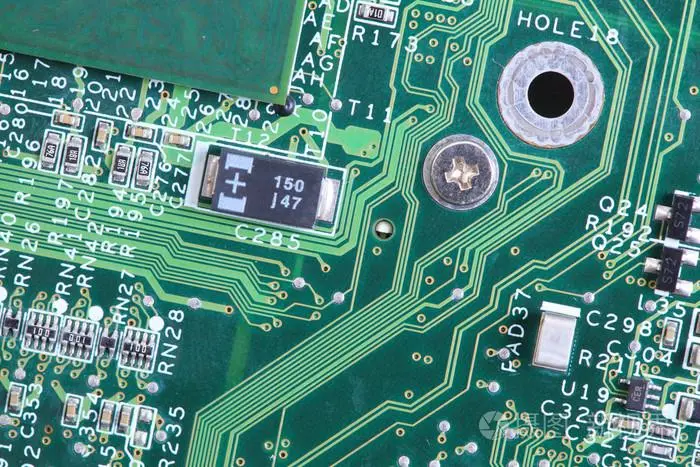
PCB hot air leveling technology is a relatively mature technology at present, but because its process is in a high temperature and high pressure dynamic environment, its quality is difficult to control and stabilize. This paper will introduce some experience on the control of hot air leveling process.
Hot air leveling solder coating HAL (commonly known as tin spraying) is a post-processing process widely used in circuit board factories in recent years. In fact, it is a process that combines dip welding and hot air leveling to coat eutectic solder in the metallized holes of printed boards and on printed wires. The process is to dip the PCB with flux, then dip the solder in the molten solder, and then pass between two air knives. Use the hot compressed air in the air knife to blow off the excess solder on the PCB, and at the same time remove the excess solder in the metal hole, so as to obtain a bright, flat and uniform solder coating.
The most outstanding advantages of solder coating with hot air leveling are that the coating composition remains unchanged, the edges of printed circuit can be completely protected, and the coating thickness can be controlled through the air knife; The bonding between the coating and the base copper makes the metal bond, with good wettability, weldability and corrosion resistance. As the post process of PCB, its advantages and disadvantages directly affect the appearance of PCB, corrosion resistance and welding quality of customers. How to control the process is a concern of PCB manufacturers. Now let's talk about some experience in controlling PCB process control of vertical hot air leveling, which is the most widely used one.
1、 Selection and application of flux
The flux used for hot air leveling is a special flux. Its role in hot air leveling is to activate the copper surface exposed on the printed circuit board and improve the wettability of solder on the copper surface; Ensure that the laminate surface is not overheated, provide protection for the solder when it is cooled after leveling to prevent the solder from oxidation, and prevent the solder from sticking to the solder barrier coating to prevent the solder from bridging between pads; The waste flux can clean the solder surface, and the solder oxide is discharged together with the waste flux.
The special flux for hot air leveling must have the following characteristics:
1. It must be water-soluble flux, biodegradable and non-toxic.
Water soluble flux is easy to clean, and there is less residue on the board surface, which will not form ion pollution on the board surface; Biodegradation can be discharged without special treatment, meeting the environmental requirements and greatly reducing the harm to human body.
2. Good activity
About the activity, that is, the characteristic of removing the oxide layer on the copper surface improves the wettability of the solder on the copper surface. Usually, an activator is added to the solder. In selection, both good activity and minimum corrosion to copper shall be considered, so as to reduce the solubility of copper in solder and reduce the damage of smoke to equipment.
The activity of flux is mainly reflected in the tin loading ability. Because the active substances used by various fluxes are different, their activities are different. High activity flux, good tin coating on dense pads and patches; On the contrary, copper is easily exposed on the board, and the activity of active substances is also reflected in the brightness and flatness of tin surface.
3. Thermal stability
Prevent green oil and substrate from high temperature impact.
4. Must have a certain viscosity
Hot air leveling requires a certain viscosity for the flux. The viscosity determines the fluidity of the flux. In order to fully protect the solder and the laminate surface, the flux must have a certain viscosity. The flux with low viscosity is easy to adhere to the PCB laminate surface (also known as tin hanging), and is easy to bridge at dense places such as IC.
5. Suitable acidity
The soldering flux with too high acidity is easy to peel the edge of the solder mask before spraying, and the residue after spraying is easy to blacken and oxidize the tin surface. Generally, the PH value of flux is about 2.5-3.5.
Other properties are mainly reflected in the impact on operators and operating costs, such as bad smell, high volatile substances, large smoke, unit coating area, etc., which should be selected by the manufacturer on the basis of experiments.
During trial, the following performances can be tested and compared one by one:
1. Flatness, brightness, whether the hole is plugged
2. Activity: Select fine and dense patch circuit boards to test their tin loading ability.
3. The circuit board shall be coated with flux for 30 minutes. After cleaning, use tape to test the peeling of green oil.
4. Leave the spray plate for 30 minutes, and test whether the tin surface turns black.
5. Residue after cleaning
6. Whether the dense IC bits are connected.
7. Whether tin is hung on the back of single panel (fiberglass board, etc.).
8. Smoke
9. Volatility, odor, whether diluent needs to be added
10. Whether there is foam during cleaning.
2、 Control and selection of hot air leveling process parameters
Hot air leveling process parameters include PCB solder temperature, dip welding time, air knife pressure, air knife temperature, air knife angle, air knife spacing and PCB rising speed. The impact of these process parameters on PCB quality will be discussed below.
1. Tin dipping time:
The tin dipping time is closely related to the quality of solder coating. During dip welding, a layer of metal compound JIMC is formed between the base copper and the tin in the solder, and a layer of solder coating is formed on the wire. The above process generally takes 2-4 seconds, during which a good intermetallic compound can be formed. The longer the time, the thicker the solder. However, if the time is too long, the base material of PCB will be layered and the green oil will bubble. If the time is too short, it is easy to have the phenomenon of semi immersion, causing local tin surface to be white, and in addition, it is easy to have rough tin surface.
2. Bath temperature:
Lead 37/tin 63 alloy is widely used as the soldering material for PCB and electronic components, and its melting point is 183 ℃. When the temperature of solder is 183 ℃ - 221 ℃, the ability to form intermetallic compounds with copper is very small. When the temperature is 221 ℃, the solder enters the wetting zone, and the range is 221 ℃ - 293 ℃. Considering that the plate is easy to be damaged at high temperature, the solder temperature should be selected lower. Theoretically, 232 ℃ is the maximum solder temperature, and in practice, 250 ℃ can be set as the optimal temperature.
3. Air knife pressure:
There is too much solder on the soldered PCB, and almost all the metallized holes are blocked by solder. The function of the air knife is to blow off the excess solder and conduct the metallized hole, so as not to reduce the aperture of the metallized hole too much. The energy used for this purpose is provided by the pressure and flow rate of the air knife. The greater the pressure, the faster the flow rate, and the thinner the solder coating. Therefore, the air knife pressure is one of the most important parameters of hot air leveling. Normally, the air knife pressure is 0.3 - 0.5Mpa
The front and rear pressure of the air knife is generally controlled to be larger in the front and smaller in the rear, and the pressure difference is 0.05MPa. According to the distribution of geometric figures on the board surface, the pressure of the front and rear air knives can be adjusted appropriately to ensure that the IC position is flat and the patch is free of protrusions. Refer to the factory manual of the tin spraying machine of the factory for specific values.
4. Air knife temperature:
The hot air flowing out of the air knife has little influence on the PCB and the air pressure. However, increasing the temperature in the air knife will help to expand the air. Therefore, when the pressure is constant, increasing the air temperature can provide a larger air volume and a faster flow rate, so as to produce a larger leveling force. The temperature of the air knife has a certain influence on the appearance of the solder coating after leveling. When the air knife temperature is lower than 93 ℃, the coating surface becomes dark. With the increase of air temperature, the dark coating tends to reduce. At 176 ℃, the darkened appearance disappears completely. Therefore, the minimum temperature of the air knife shall not be lower than 176 ℃. Generally, in order to obtain good tin surface flatness, the air knife temperature can be controlled between 300 ℃ and 400 ℃.
5. Air knife spacing:
When the hot air in the air knife leaves the nozzle, the flow rate slows down to a degree proportional to the square of the air knife spacing. Therefore, the greater the spacing, the smaller the air velocity and the lower the leveling force. The spacing of air knife is generally 0.95-1.25CM. The spacing of air knife cannot be too small, which will cause friction on the printed board and prevent the garden from being polluted. The distance between the upper and lower air knives is generally kept at about 4mm, and if it is too large, it is easy to have solder spatter.
6. Air knife angle:
The angle of the air knife blowing the board affects the solder coating thickness. If the angle is adjusted improperly, the solder thickness on both sides of the printed board will be different, which may also cause molten solder spatter and noise. The angle of most front and rear air knives is adjusted to be 4 degrees downward, which is slightly adjusted according to the specific plate type and the geometric distribution angle of the plate surface.
7. PCB rising speed:
Another variable related to hot air leveling is the speed of passing between the air knives, that is, the rising speed of the conveyor. This parameter will affect the thickness of the solder. The speed is slow, and there is more air blowing on the PCB, so the solder is thin. On the contrary, the solder is too thick, even blocking the hole.
8. PCB preheating temperature and time:
The purpose of preheating is to improve the activity of flux and reduce thermal shock. Generally, the preheating temperature is 343 ℃. When preheating for 15 seconds, the surface temperature of the printed board can reach about 80 ℃. Some hot air leveling has no preheating process.
3、 Uniformity of PCB solder coating thickness
The thickness of solder coated by hot air leveling is basically uniform. However, with the change of the geometric factors of the printed wire, the leveling effect of the air knife on the solder also changes, so the thickness of the solder coating for hot air leveling also changes. Generally, the printed wire parallel to the leveling direction has small resistance to air and large leveling force, so the coating is thinner. The printed wire perpendicular to the leveling direction has large resistance to air, so the leveling effect is smaller. Therefore, the coating is thicker, and the solder coating in the metallized hole is uneven. It is very difficult to obtain a completely uniform and flat tin surface because PCB solder is immediately in a dynamic environment of strong pressure and high temperature as soon as it is put into the high-temperature tin furnace. However, it can be as smooth as possible through parameter adjustment.
1. Select active flux and solder
Flux is the main factor of tin surface flatness. A smooth, bright and complete tin surface can be obtained with a good flux activity.
Lead tin alloy with high purity shall be selected as the solder, and copper bleaching shall be carried out regularly to ensure that the copper content is below 0.03%.
2. Equipment adjustment
The air knife is a direct factor to adjust the flatness of the tin surface. The angle of the air knife, the pressure and pressure difference between the front and rear air knives, the temperature of the air knife, the air knife spacing (vertical distance, horizontal distance) and the lifting speed will have a great impact on the board surface. For different plate types, their parameter values are different. Some technologically advanced tin spraying machines are equipped with microcomputers to store the parameters of various plate types in the computer for automatic adjustment.
Clean the air knife and guide rail at regular intervals, and clean the residue in the air knife gap every two hours. When the production is large, the cleaning density will increase.
3. Pretreatment
The micro etching treatment also has a great influence on the flatness of PCB tin surface. The micro etching depth is too low, and it is difficult for copper and tin to form copper tin compounds on the PCB surface, resulting in local tin surface roughness; The poor stabilizer in the micro etching solution will lead to too fast and uneven copper etching and uneven tin surface. APS system is generally recommended.
For some plate types, baking pretreatment is sometimes required, which will also have a certain impact on tin coating smoothness.
4. Previous PCB process control
Because hot air leveling is the last process, many previous processes will have a certain impact on it, such as poor tin coating due to poor development. Strengthening the control of the previous process can greatly reduce the problems in hot air leveling.
Although the above solder coating thickness for hot air leveling is uneven, it can meet the requirements of MIL-STD-275D.