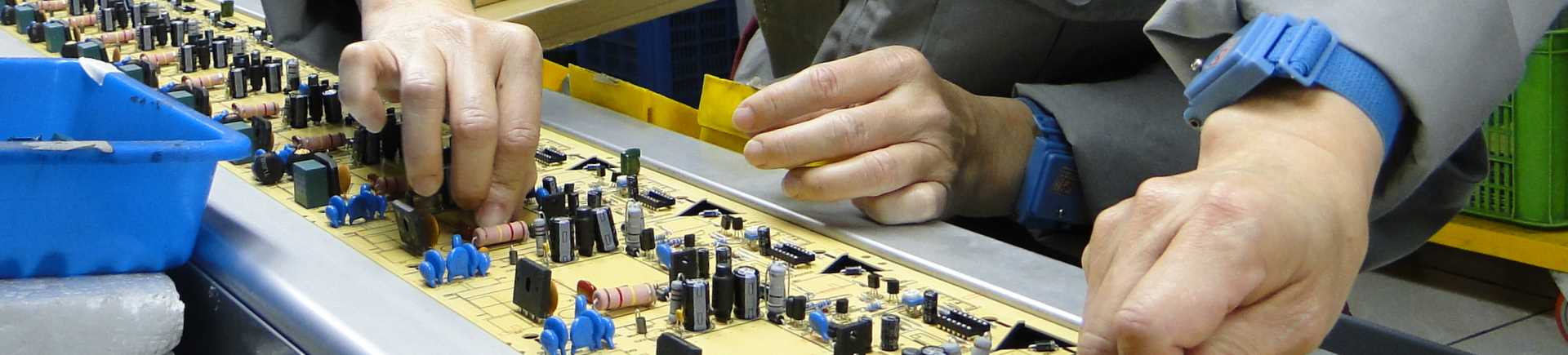
Basic situation of fully automated PCB factory
1. Brief introduction of fully automatic PCB factory
There is one factory in the US - Whelen Engineering, a manufacturer of sirens and sirens located in New Hampshire. Because it costs them $7 million a year to buy circuit boards and the lead time is long, Whelen management decided to build a PCB factory by itself, mainly to produce internal orders. They hired Alex, an ace engineer, and gave him a task: build a PCB factory according to the demand, and the return on investment time is 5 years. Designing on a 45,000-square-foot blank canvas with a $12 million budget and planning a product lineup of 2,500 different part numbers was the base requirement for Whelen, but they got far more than that. Engineer Alex found that the only way he could meet Whelen's requirements was to use a fully automatic method, using only the minimum number of personnel, all materials can be recycled, and there is no polluting emission. Finally in 2015, Alex realized the automated production of the entire factory, owning the world's first fully automated online, no lighting, zero waste water discharge, 100% digital PCB factory, which is different from any PCB factory facilities seen before .
Overhead view of Whelen PCB factory
The factory is the most automated PCB factory in North America, and it is also the world's first fully automated online, no lighting (black light), zero waste water discharge, and 100% digital PCB factory. The complete digital processing process of its fully automatic production line includes 38 integrated equipment. The factory operates itself according to the control plan set in advance, and the operation is stable and the product quality is guaranteed. At present, the factory mainly produces metal core printed boards, and also produces a small amount of rigid-flex circuit boards and multi-layer rigid boards. The maximum batch size of panels produced is 1,000 pieces, and the minimum batch size is 1 piece.
The greatest significance of the Whelen factory is that the customized and automated production lines not only shorten the production cycle, but also greatly reduce labor costs. Compared with traditional production lines, the production efficiency has improved significantly. At present, the equipment and equipment of the entire factory come from 39 different suppliers. Whelen cooperates with suppliers to set chemical parameters and mechanical parameters; in this factory, the control system is the nerve network of the smart factory. Once all the programming logic is programmed into Factory automation programs immediately generate unified, real-time mechanisms for problem solving and continuous improvement of system performance.
From the perspective of effect, the Whelen factory has almost subverted the traditional PCB industry, as follows:
The production cycle is greatly shortened: the average production time of each circuit board in the traditional production line is 6 weeks (some companies can increase it to about 1 week), and the production cycle of Whelen's automated production line is 4.5 hours per panel, which can be achieved in the fully automatic mode. A panel is produced every 75 seconds, and drilling, sub-paneling and testing are required in the later stage, so on average, an additional two hours are needed. Production efficiency has been greatly improved.
The labor force is significantly reduced: the traditional production line requires 75-100 people to produce the same level of circuit boards, but the Whelen fully automatic PCB factory has only 17 employees, and there are only two operators next to the entire production line, and the labor cost has dropped significantly.
Economies of scale are easier to achieve: about 2,500 different part numbers are in production, and costs are even more favorable relative to the Asia-Pacific region.
Successfully achieve zero emissions: only part of the solid waste is generated, and most of them can be reused, truly achieving "zero emissions"
Process flow and division of labor
WHELEN Processing Sequence WHELEN Labor Requirements 1 Loader Worker #1 Worker #3 (Backup) 2 Deburring 3 Inline Loading/Unloading 4 Conductive Polymer/Horizontal Copper Plating 5 Inline Loading/Unloading 6 Pre-Clean 73C Panel Smart Buffer (Random Storage) Take) 8 inkjet line imaging 9 online loading/unloading 103C panel intelligent buffer (random access) 11 tin plating 12 FIFO buffer machine 13 stripping (printing & etching) 1490 degree change direction 15 etching 16 stripping ( Printing & etching) 17 online loading/unloading 18 tinned strip 19 online loading/unloading 20 oxide/mask layer pre-cleaner #221 online loading/unloading 22 oxide post-dipping 23 online loading/unloading 24 groups of solder layers Protective layer 25 sets of welding layer spot welding oven 26 online loading/unloading 27 LDI using robots 28 online loading/unloading 292 word printing machines using robots 30 online loading/unloading 31 final curing 32 online loading/unloading 3390-degree steering 34HASL Pre-cleaning 35HASL36HASL Pre-cleaning 3790 degrees turning 38 unloading Off-line process Ι drilling/milling/cutting worker #4 IIET/final inspection shipping worker #5 III lamination/lamination/plasma treatment worker #6 IV maintenance worker