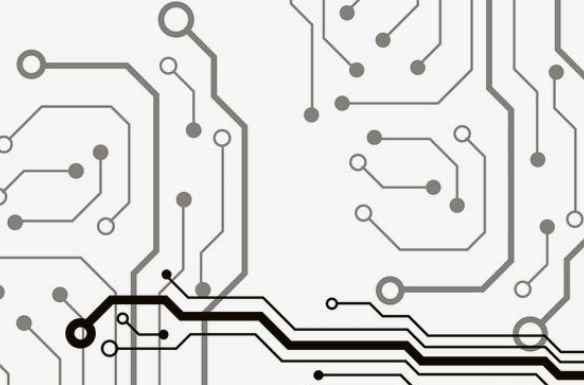
1. Short circuit caused by tin running: 1. Tin running is caused by improper operation in the film removing medicine water cylinder; 2, has retreated the film of the plate superimposed together to cause tin.
Improvement methods:
(1) The film retreating potion concentration is high, the film retreating time is long, the anti-coating film has fallen, the plate is still soaked in a strong alkali solution, part of the tin powder attached to the surface of copper foil, etching a very thin layer of metal tin protecting the surface of copper, corrosion resistance, resulting in the removal of copper is not clean, resulting in short circuit. Therefore, we need to strictly control the concentration, temperature and time of the film retreating potion. At the same time, when the film retreating, insert the plate frame is inserted, and the plate and the plate can not be stacked against each other.
(2) The retreated film plate is not dried and stacked together, so that the tin between the plate and the plate immersed in the non-dried film solution, part of the tin layer will dissolve attached to the surface of copper foil, etching a very thin layer of metal tin protecting the surface of copper, corrosion resistance, resulting in the removal of copper is not clean, resulting in short circuit.
Second, short circuit caused by unclean etching:
1. The quality of parameter control of etching potion directly affects the quality of etching. At present, our company uses alkaline etching liquid. If the PH value is low, the solution will become sticky, white in color, and the erosion rate will decrease. This situation is easy to cause side corrosion. The PH value is mainly controlled by adding ammonia water.
1.2 Chloride ions: The content of chloride ions is controlled between 190 and 210g/L. The content of chloride ions is mainly controlled by etching salt, which is composed of ammonium chloride and supplements.
1.3 Specific gravity: The specific gravity is controlled mainly by controlling the content of copper ions. Generally, the content of copper ions is controlled between 145~155g/L, and it is tested every hour or so to ensure the stability of specific gravity.
1.4 Temperature: Control at 48~52℃, if the temperature is high, ammonia volatilizer fast, will cause pH instability, and most of the cylinder of the etching machine is made of PVC material, PVC temperature limit of 55℃, beyond this temperature is easy to cause cylinder deformation, or even cause the etching machine scrap, so it must be installed automatic temperature controller to effectively monitor the temperature, Make sure it's under control.
1.5 Speed: Generally adjust the appropriate speed according to the thickness of the plate bottom copper. Suggestion: In order to achieve the stability and balance of the above parameters, it is recommended to configure automatic feeding machine, in order to control the chemical composition of the child liquid, so that the composition of the etching liquid in a relatively stable state.
2, the whole plate electroplating copper plating thickness is not uniform, resulting in unclean etching. Improvement methods: (1) Automatic line production should be realized as far as possible during the plating of the whole plate, and the current density per unit area should be adjusted according to the size of the hole area (1.5~2.0A/dm2). The plating time should be kept consistent as far as possible to ensure full load production. Meanwhile, negative and anode baffles should be added, and the use system of "electroplating edge" should be formulated to reduce the potential difference. (2) If the whole plate plating is manual line production, then the plate needs to use double clamping stick plating, as far as possible to keep the current density of the unit area, at the same time to install a timing alarm, to ensure the consistency of plating time, reduce potential difference.
Three, visual micro short circuit:
1, exposure machine Myra film scratches caused by the line micro short circuit; 2. Slight short circuit caused by scratches on the glass on the exposure plate. Improvement method:
(1) the exposure machine Myra film due to use time is longer, there is scratch phenomenon on the film surface, scratch accumulation dust form black or opaque "small lines", in line graphics exposure due to black or opaque "small lines" shading, making the development between the line formed copper point and short circuit, and the thinner the copper foil on the plate is easier to short circuit, The smaller the spacing, the easier the short circuit. So when we once found Myra film scratches, we must immediately replace or clean with anhydrous alcohol, ensure the transparency of Myra film, strict control of the existence of opaque scratches.
(2) exposure machine exposure plate glass due to the use of a long time, the glass surface scratch phenomenon, scratch accumulation of dust to form black marks or opaque "small lines", also in the line graphic exposure due to opaque "small lines" shading, after the development of the line between the formation of copper and short circuit. So when we find the phenomenon of glass scratches, we must immediately replace or clean with waterless sprinkling, strictly control the existence of opaque scratches