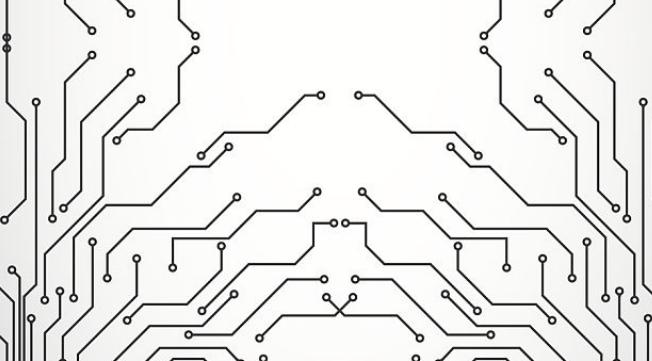
hydrodynamics
1) Surface tension of etching fluid: Since every object has a certain surface area, the surface of a liquid is like a tight film. This film has an inward attraction at the molecular level, which makes it tend to shrink. In order to maintain this tight surface equilibrium, an appropriate force of contact with the surface must be added to the surface perimeter so that the surface can maintain a certain area and no longer shrink. This force tangential to a surface is called surface tension.
The tension acting on a surface per unit length is denoted by the symbol σ. The units are dyne per centimeter. The influence of surface tension of etching solution on etching rate and etching quality is related to the wetting degree of solid surface (copper foil surface). Wetting is the adhesion of a liquid to a solid surface. That is, the shape of the liquid on the solid surface depends on the size of the contact Angle (θ). The greater the contact Angle, the poorer the wetting of the solid surface, that is, the poorer the hydrophilicity. To maintain the contact Angle (θ) as the minimum acute Angle, it is necessary to change the surface properties of the solid. That is to say, the lower the surface tension of the liquid, the better the wettability of the solid surface, but if the solid surface is stained, even if the liquid surface tension is low, it will not improve the degree of wetting of the solid surface.
Therefore, to obtain the best etching quality, it is necessary to strengthen the cleaning treatment of the substrate copper foil surface, improve the surface properties so that the etching fluid is better in the wet state. To improve the surface tension of the liquid, it is necessary to increase the operating temperature. The higher the temperature, the smaller the surface tension of the liquid, and the attachment of the solid is more ideal, and the treatment effect is good. This is because the increase of temperature causes the expansion of substances, which increases the distance between molecules and decreases the attraction between molecules. Therefore, the surface tension decreases gradually with the increase of the temperature of solution. Therefore, the contact state between solution and substrate copper surface can be improved by strictly controlling process conditions.
2) Viscosity: in the etching process, with the continuous dissolution of copper, the viscosity of the etching liquid will increase, so that the fluidity of the etching liquid on the surface of the copper foil on the substrate is poor, which directly affects the etching effect. In order to achieve the best state of the ideal etching fluid, it is necessary to make full use of the function of the etching machine to ensure the fluidity of the solution.
Electronic enterprise SMT SMT machine use precautions
1. Non-operators are not allowed to use the attaching machine.
2. Operators should be familiar with the contents of the instruction manual, and operate and maintain the equipment in strict accordance with its provisions.
3, must confirm the voltage 380V, total pressure 6.2kg/cm. The main power switch can only be opened when the air pressure of the mounting machine is 5.2kg/cm.
4. Check whether there is water in the filter every day, and release water if there is.
5. Before turning on the main power every day, check that the camera and suction nozzle should be clean according to the reference manual. Check and ensure that there are no obstacles on the conveyor belt, within the moving range of the mounting head, around the suction nozzle library and on the tray rack.
6. When adjusting the width of the guide rail, pull out all PCB supporting thimbles. There should be no PCB at the entrance and exit ends to prevent damage to the guide rail. After adjusting the width of guide rail, adjust the width of guide rail of buffer table at the same time to make PCB transmission smooth.
7, the feeding device should be in good condition before installation. If the equipment is not equipped with a feeder float device, the pneumatic feeder should be installed to ensure that the feeder is correctly installed in place to prevent damage to the mounting head; After the electric feeder is installed, the green light should be on, indicating that the installation is successful. After the tray feeder is installed, the door should be closed.
8. Before pressing the Start key, ensure that there are no obstacles around the mounting head, conveyor belt, feeder library and tray feeder.
9. Do not open or close the machine cover at will during the startup of the equipment; Don't connect the mouse or keyboard ahead of time. Any irregular operation will cause the abnormal start of the system.
10, normal operation, should cover the protective cover to operate the machine.
11. When installing the feeder, the equipment must be completely stopped before it can be carried out. After shutting down the machine, it is more than 15 seconds before starting the machine again. When the machine does not work normally, press the emergency stop switch immediately.
12. In case of sudden power failure, the equipment should be shut down immediately to prevent personal injury or damage to the machine caused by sudden restart.
13. When shutting down the equipment, first exit the program to close the monitor, then turn off the main power supply, and finally turn off the air source.
14. Keep the equipment clean and clean it once a week. Cover the cloth when not in use.
15, two people work carefully, not two people at the same time operation, to prevent equipment or personal injury, equipment work table is not allowed to place any debris.
16. After turning on the main power supply of the equipment every day, check whether the switches, ANC and PCB transmission of the equipment are normal according to the reference manual.
17. Check whether X-Y workbench, connectors, motors, CCD, alarm system and switches are normal according to the operation instructions every month.