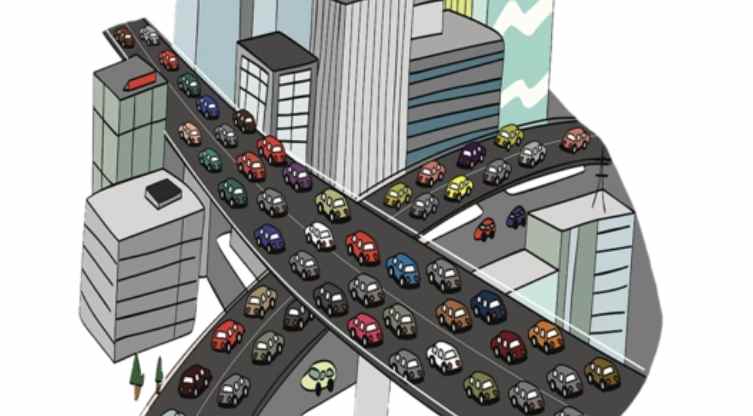
At present, with the development of printed circuit boardsin the direction of high density and high precision, more stringent requirements have been put forward for copper sulfate plating process. It is necessary to control various factors in the process of copper plating, in order to obtain high quality coating. The following analyzes the causes of excessive chloride ion consumption in the process of copper plating.
The antecedents of excessive chloride ion consumption are:
When copper plating, the low current area of the circuit board surface appears "dull" phenomenon, and the concentration of chlorine formula is low; In general, after adding hydrochloric acid, the coating in the low current density area of the plate can disappear, the chloride ion concentration in the plating solution can reach the normal range, and the surface coating is bright. If a large amount of hydrochloric acid is added to solve the coating "tarnish" phenomenon in the low current density area, it is not necessarily caused by the low concentration of chloride ions, and the real reason needs to be analyzed. If take to add a large amount of hydrochloric acid: one, may produce other consequences, two to increase the cost of production, is not conducive to enterprise competition.
Correct analysis of "low current density area coating luster" reasons:
A large amount of hydrochloric acid is added to eliminate the phenomenon of "low current density area coating is not bright", indicating that if there are too few chloride ions, it is necessary to add hydrochloric acid to increase the concentration of chloride ions to reach the normal range, so that the coating in low current density area is bright. What if you have to multiply hydrochloric acid to get the concentration of chloride into the normal range? What's consuming a lot of chloride? Too high concentration of chloride ions will make brightener consumption fast. It indicates that chloride ions will react with brightener and excessive chloride ions will be consumed. In turn, excess brightener also consumes chloride ions. Because too little chloride ion and brightener excess are the main reasons for the low current density area coating is not bright, so it can be seen that "the main reason for excessive chloride ion consumption in copper plating is the concentration of brightener is too high.
Reflow welding technology of SMT SMT machine production line
Reflow welding process is to weld the mechanical and electrical connections between the welding surfaces or pins of surface-mounted components and the PCB welding pad by melting the solder paste pre-allocated to the PCB welding pad.
Reflow welding can ensure excellent welding results. The main process elements of reflow welding are reflow furnace and its welding ability, which is mainly reflected in the cooling system, heating system, inert gas protection system and flux management system of reflow furnace. Among them, the heating system is related to temperature control precision, heating efficiency, temperature uniformity and stability.
The main function of the cooling system is that when the peak temperature of reflow welding is high, if the temperature of the base plate out of the reflow welding furnace is too high, it is easy to cause the bending of the base plate. Timely cooling refines the structure and prevents the intermetallic compounds from thickening. Improves reliability.
Flux is volatile in reflow welding process. If there is not an excellent flux management system in time to remove volatile flux and filter circulation, flux will follow high temperature airflow into the cooling zone, and condense in the radiator and furnace, it will reduce the cooling effect and pollute the equipment and substrate. When the activity of the solder paste used to match the substrate is not good enough or there are ultra-fine-spaced components and complex pieces on the circuit board, and the substrate needs to pass through the reflow furnace for several times, it is considered to fill the reflow furnace with inert gas to reduce the chance of oxidation and improve the welding activity. A common inert gas used is nitrogen.
The welding ability of reflow furnace also needs to be developed by editing the control program of reflow furnace. When the circuit board of the finished patch passes through the reflow furnace, it generally goes through the preheating stage, the holding stage, the reflow stage and the cooling stage. The welding quality is guaranteed by the control procedure of reflow furnace.
The auxiliary process is used to assist the smooth installation and prevent testing and post-testing. The auxiliary technology mainly consists of optically aided automatic detection technology and "spot paste" technology. "Dispensing" process is through the special glue to "spot" below or around the required components, and the components are properly protected to ensure that the components will not fall off after repeated reflow welding. Reduce the stress impact of components in the mounting process, to ensure that components in the complex use environment is not damaged.
"Dispensing" process mainly includes "dispensing" equipment, special glue and "dispensing" parameter Settings. It is necessary to choose the equipment reasonably and set the parameters to ensure the process effect.
The process of optically assisted automatic detection mainly includes: first, special optical equipment is used to measure the thickness uniformity and printing accuracy of the solder paste after printing, the accuracy of the patch is detected after patting, and the defective circuit board is detected and reported in time before reflow welding, and then special optical equipment is used to detect the solder joints after reflow welding, and the circuit board with solder joints defects is detected and reported. Special optical measuring equipment mainly includes X-ray detection equipment and visible light detection equipment. The latter is mainly automatic optical detection equipment AOI, the former is mainly three and five dimensional X-ray equipment. The latter is mainly used to detect visual solder joints, and the former in addition to the detection of visual solder joints, but also can detect non-visual BGA class parts of the solder joints. Whether to use auxiliary technology is determined by the characteristics of the required mount product.