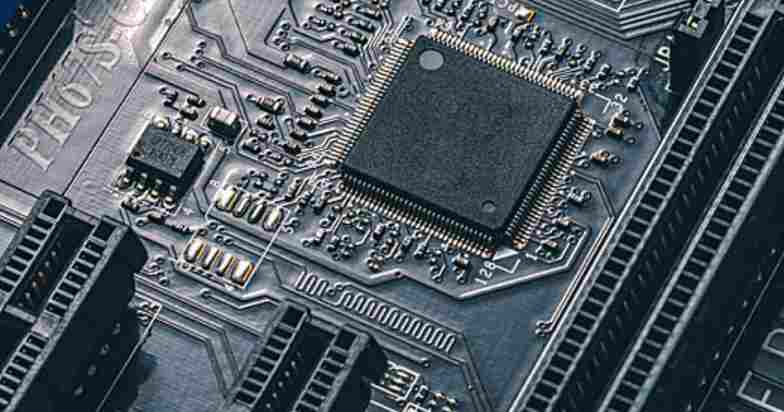
The line quality of the plate produced using vacuum etching technology is also very good. Detailed testing with various PCB manufacturershas shown that the new vacuum etching technique produces a straighter conductor profile, so that the produced board can more precisely match the wiring requirements.
In the vacuum etching process, the shrinkage rate of the lateral attack of the etching medium on the wire and the value of the etching factor used to describe the etching depth and lateral etching amount of the wire are very high.
Of course, there are a range of other factors that are largely unaffected by the manufacturer that affect the actual etching. For example, the thickness of the resist, the quality of the exposure and development process, and the copper thickness of the etching substrate all have significant effects. In general, it is estimated that the renewal frequency of the etching process or the etching solution accounts for only half of the effect of the etching effect. But Oliver Briel, PILL project manager, notes that "it turns out that we have this 50% under control".
Vacuum etching also shows a series of other advantages:
The capacity of the etching process can be fully utilized. The production of the etching process increases as the etching rate increases and the production time decreases.
Because the first etching can achieve satisfactory results, so there is no need to rework for reetching.
Can reduce the related plant control engineering, reduce the corresponding cost.
Vacuum etching systems use relatively simple technology to produce hyperfine wires, eliminating the need for oscillating jet manifels.
Intermittent nozzle construction with adjustable injection pressure can be eliminated. The main purpose of this design is to ensure that the puddle effect is reduced, which can now be accomplished simply by using the suction system. Vacuum etching technology allows for shorter, more compact flow modules that can simultaneously inhale and etch in the same module.
The additional advantage of vacuum etching systems is that the spray manifold can be positioned laterally along the direction of travel. The traditional injection manifold used to produce fine wire plates usually has the nozzle positioned longitudinally along the direction of travel so that different injection pressures can be present at the edge and in the plate. The nozzle is properly angled to the direction of travel for easy maintenance and less time to replace, and this arrangement also allows for simple electrical flow monitoring of each injector manifold individually. If an irregularity occurs, the user can immediately identify which injector manifold is in trouble and adjust it without delay.
Vacuum etching technology has great potential in the future, because the process is particularly suitable for the production of fine wire and ultra-fine wire structure plates. Preliminary tests of conductive patterns below 50 microns yield promising results. Further evaluation of the ability to produce thick copper plate lines using vacuum etching is under way, and all current data indicate favorable results. It is particularly noteworthy that not only traditional copper chloride but also ferric chloride (Ⅲ), which is widely used in Asia, was used as etching medium. Although using this etching medium takes a long time, it works well when the conductor profile is steeper and undoubtedly provides an alternative to the process now accepted as standard, especially for the production of ultra-fine lines.
When requested, the vacuum etch line can be fitted with an environmentally friendly regeneration system: instead of using hydrogen peroxide, it uses oxygen from the air, i.e. no additional pure oxygen is needed to re-oxidize the copper chloride solution. In practical application over a long period of time, the system using this technology has proved to be successful, and the investment cost can be recouped quickly.
PCB pure water equipment and circuit board pure water equipment mainly refers to the water purification equipment when some processes need to be cleaned in the production process of PCB and circuit board. The water quality requirements are generally 10us, if there are higher requirements, the water quality is generally less than 1us. Circuit board pure water equipment generally uses reverse osmosis pure water equipment. If the water quality is pure water with electrical conductivity below 10us, it is also necessary to configure mixed bed or EDI equipment to meet the water requirements. The following processes of PCB circuit board production need pure water cleaning: copper plating, gold plating, silver plating, nickel plating, tin plating. Can be used for multilayer circuit board, double layer circuit board and single layer circuit board production.
According to different water quality requirements, it is mainly divided into two technological processes:
Pure water equipment less than 10us:
Original water tank - stainless steel booster pump - multi-media filter - activated carbon filter - precision filter - reverse osmosis host - pure water tank - water point
PCB circuit board ultra-pure water process:
Original water tank - stainless steel booster pump - multi-media filter - activated carbon filter - precision filter - reverse osmosis host - ion exchange mixing bed - UV sterilizer - polishing mixing bed - interrupt filtration - water point
Features and advantages of PCB pure water equipment for circuit board washing
1. Two-stage RO+EDI water treatment process is mature, reliable, advanced and highly automated.
2, the treatment of ultrapure water quality meets the requirements, high water utilization rate, reliable operation, economic and reasonable.
3, PLC+ touch screen control, a full set of high degree of automation, high system stability, saving labor and maintenance costs.