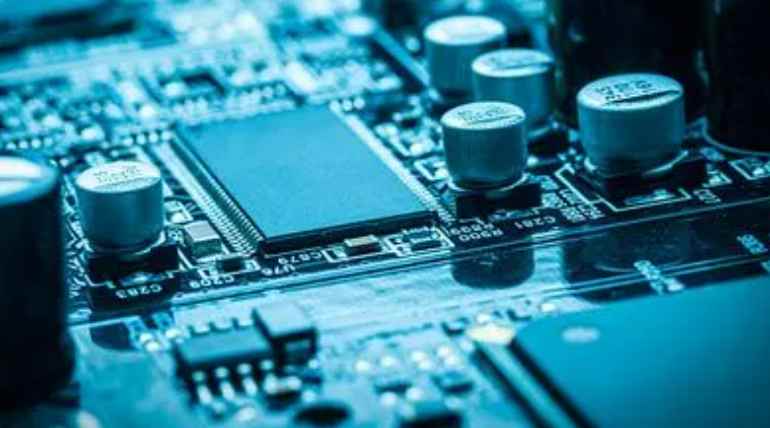
Etching process is one of the basic steps in the PCB production process. Simply speaking, the base copper is covered by the anti-corrosion layer, and the copper that is not protected by the anti-corrosion layer reacts with the etching agent, so as to be bitten off, and finally forms the process of designing circuit graphics and welding pad. Of course, the principle of etching can be easily described in a few words, but in fact the implementation of etching technology is quite challenging, especially in the production of micro lines, small line width tolerance requirements, do not allow any error in the etching process, so the etching result should be just right, not wide, not over etching.
Further explaining the etching process, PCB manufacturers prefer to use horizontal etching lines for production in order to achieve maximum production automation and reduce production costs. However, horizontal etching is not perfect. The "pool effect" that cannot be eliminated makes the upper and lower surface of the board produce different etching effects, and the etching rate of the edge of the board is faster than that of the center of the board. Sometimes, this phenomenon can lead to a large difference in the etching results on the board.
In other words, the "pool effect" can cause the line on the edge of the plate to overerode more than the line in the center of the plate, and even careful line correction (appropriately widening the line width at the edge of the plate) to compensate for different etching rates will fail because very fine controlled etching tolerances are required to obtain ultra-fine lines.
This situation leads to a significant change in etching rate. Located above the board, near the edge of the board, the etching solution is more likely to flow out of the board, and the old and new etching solution is easier to exchange, thus maintaining a better etching rate. In the center of the plate, it is easy to form a "pool" situation, the flow of etching agent is therefore limited, and the solution rich in copper ions is relatively difficult to flow out of the surface of the plate. As a result, compared with the edge or the bottom of the plate, the etching efficiency is reduced, and the etching effect is worse. In practice, it is not possible to avoid the "pool effect" because the horizontal drive roller of the chain type prevents the discharge of the etching fluid, resulting in the accumulation of the etching fluid between the rollers. This phenomenon is more pronounced in the production of large plates or ultra fine lines, even with more special process control and compensation methods. For example, the level of the transmission direction can be adjusted independently of the spray system, increase the oscillation type of spray pipe and increase the correction of the etching section, if there is no huge technical investment, this problem can not be well solved, so to avoid the "pool effect" goal without having to go back to the starting point, start again.
Late last year, PILL e.K. released a new process that prevents the puddle effect by improving the flow of the etch in the upside-down part of the board simply by pumping the used etch. This method is called vacuum etching.
The first vacuum etching line was demonstrated to the public at Productronica in November 2001. Tests conducted by circuit board manufacturers have also confirmed that the vacuum etching process can achieve superior results with less effort to control engineering conditions.
After vacuum etching, the etching effect is very uniform on both sides of the plate.
The principle of vacuum etching is simple. Not only is the nozzle installed in the etching section, but also the extraction unit is installed at a relative distance between the nozzle and the board surface. After the used etching fluid is sucked away by these extraction units, it is returned to the liquid tank of the module through a closed loop.
Vacuum in this context refers to the negative pressure in the operating area of the system and the low suction force just enough to prevent the etching fluid from creating a puddle effect. Even the thinnest inner plate cannot be lifted by the air extraction unit, and the production accuracy must be guaranteed. By connecting the pump rail to the upper roller in the conveyer system, the designer ensures the optimum distance between the pumping process and the plate surface, regardless of whether the sheet or thick plate is produced. This point means that no matter what type ofPCB board, can get uniform etching liquid extraction rate. Only 1 micron fluctuation in copper thickness was observed on the up facing side of the circuit board throughout the 24 "X24" large board surface. By comparison, the etching effect of the up-facing part and the down-facing part of the plate is basically the same.