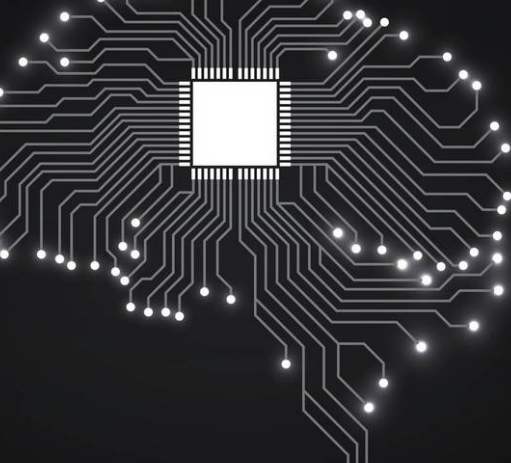
Heat, as you all know, is another enemy of the PCB and the components on it. During the operation of the circuit board, the various materials inside the PCB will undergo a wide range of temperature variations, while each component has a specified range of thermal variations. The component will absorb heat, how much heat will be absorbed depends largely on its size and shape. The higher the power, the higher the density of the electronic products will generate more heat, and too much heat will produce significant mechanical stress, which affects the solder connection and burn out the element. To prolong the life of devices and prevent failures, effective heat transfer management is very important. Overheating conditions on the board can not only speed up the failure mechanism, but also cause the device to become too hot to handle and in some cases pose a fire risk.
In addition to heat-related issues, the continued push for miniaturization means there is no room for multiple boards in electronics, and designs using hybrid technologies are on the rise, where analog, digital and radio frequency (RF) circuits are tightly integrated with high-voltage circuits, making it increasingly difficult to meet clearance and creepage design requirements. Even a very small change in the environment in which the board is located, whether it is increased dust, increased humidity, splashing water, or exposure to potentially corrosive gases, can be enough to push an otherwise safe functional design beyond the safe operating gap and creepage range and cause performance failures.
Other factors contributing to and component failures include poor solder joints, unconsumed or excessive flux, and tin whiskers. Cold solder spot refers to the solder spot formed when the solder is not completely melted during the assembly process, this solder spot causes poor connection of surface mounted components, will burn out components and cause power problems. Residual flux can also cause corrosion by absorbing moisture, resulting in short circuits and damaged components. Tin whiskers can also cause short circuits. A tri-shield coat usually prevents tin whiskers from forming during the operation of the device, but is less effective if tin whiskers are already present in the component before the coat is applied. In general, the effect of three anti-solder coatings on tin whiskers depends mainly on the coverage of the coating, rather than the performance of the coating, although some ambiguous data suggest that the harder and tougher the coating is better at relieving tin whiskers, but this relief must be balanced with the effect of extending the life of the solder joint. Overall, focusing on achieving 100% coverage of the metal surface may be a more effective tin whisker mitigation strategy.
Power surges, lightning strikes, and overheating can cause wiring damage. Damage to the silver or copper conductive path is usually visible to the naked eye, but not always. Cable damage can cause serious problems, including electrical conductivity problems, component problems, and device reliability problems. Fortunately, these wiring damages can usually be detected and repaired during the initial inspection.
While this is not an exhaustive list of every single factor contributing to PCB failures, it provides a comprehensive overview of the key factors contributing to PCB failures, which can be used to help find the cause of the failure in the event of a board failure. Finally, the board design itself may be responsible for PCB failures. In order to increase the life of the board, it is necessary to ensure that the components and materials selected are suitable, that the layout of the board is adequate, and that design validation is carried out for the specific requirements of the design. Design is also important in determining the appropriate coating method. The design of the circuit board will involve the cycle time and cost of the three-proof coating process. Something as simple as trying to place connectors or other non-coating areas all on the same side of a component that can be easily coated can have a huge impact on the ease of coating, cost of coating, and overall reliability of the component.
The most important test for the performance of the three-guard paint when the circuit board is energized is performed under wet conditions. The three test conditions are condensation, soaking or salt spray on the three-guard paint. Water containing soluble impurities is conductive, which will pick up all the weak spots in the coating and eventually short-circuit the PCB's surface. In order to provide protection in these cases, 100% defect free coverage of the metal surface of the PCB must be achieved with triple resistant paint, which is a real challenge for both the coating material itself and the coating process. Fortunately, a new two-component three-paint resistant material called "2K" enables a thicker coating thickness and perfect coating coverage, resulting in a higher level of protection. The advantage of Electrolube's 2K coating material is that it performs well, combining the strength and corrosion resistance of the encapsulating resin with the ease of use of the coating, which has been proven positively in three of the most demanding tests any coated material can undergo, including power condensation and power brine immersion.
conclusion
Our daily life and work depend on a variety of electronic devices, from smart phones, tablets, personal computers and laptops, to street lights, TV, refrigerators, microwave ovens and cars, and PCB is the basis of all electronic devices can play a role, is the vitality of electronic devices. When a PCB fails, it can cause huge damage and is vital in applications such as aerospace. Thus, the material chosen to protect the electronic components can actually make or break a printed circuit board, especially if the board must withstand a large amount of physical shock and thermal cycling. Inspection and testing before and after application is essential to ensure reliable operation and improve the life of PCBS, especially for PCBS destined to work in harsh environments. Choose the right materials to provide the necessary protection for the board, apply them well, and allow the coating to cure completely. Check the interactions between the coated material and chemicals used in other processes and thoroughly clean the components before applying. If possible, spend some time during the design phase simplifying the coating process. The connector is uncoated, and it is simple to place the connector on the same side of the assembly as as many non-coated components as possible. This will simplify the coating process of the three-guard paint. Unfortunately, PCBS can still malfunction after the use of three resistant paints, but the positive news is that board failures can be prevented through systematic pre-coating inspection, correct material selection, coating method, and more rigorous post-coating testing.