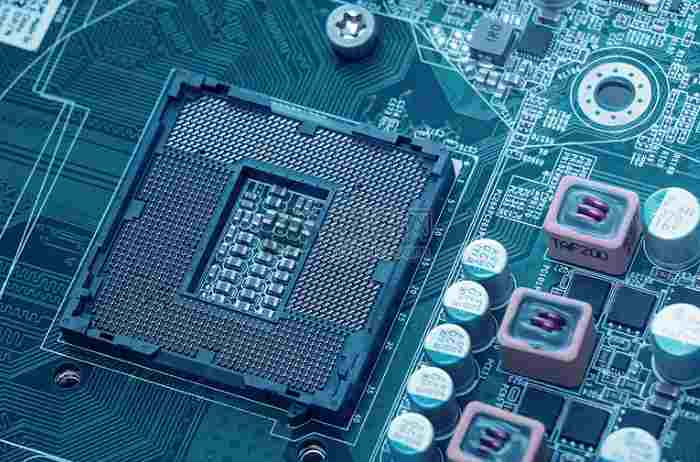
Area reduction, thickness reduction and multilayer. Different reliability requirements for PCBS at different locations
As far as public safety is concerned, cars fall into the high reliability product category, therefore, car PCBS must pass some reliability tests, with the exception of general requirements such as size, dimension, mechanical and electrical properties.
a. Thermal Cycle Test (TCT)
The PCB thermal cycle temperature is summarized in Table 1 below according to the five grades classified according to the different position of the vehicle.
b. Thermal shock test
Automotive PCBS are increasingly used in high temperature environments, this is especially true for thick copper PCBS that must deal with external heat and spontaneous heat. As a result, automotive PCB has higher requirements for heat resistance.
c. Temperature and humidity deviation (THB) test
Because automotive PCBS are in a variety of environments, including rainy or wet conditions, it is necessary to test them for THB. Test conditions include temperature (85℃), humidity (85% RH), and bias (DC 24V, 50V, 250V, or 500V).
THB testing must take into account CAF migration of PCBS. CAF usually occurs between adjacent through-holes, through-holes and lines, adjacent lines or adjacent layers, resulting in reduced insulation or even short circuiting. The corresponding insulation resistance depends on the through hole, the distance between the line and the layer.
Manufacturing characteristics of automotive PCB
High frequency substrate
Automobile anti-collision/predictive braking safety system plays the role of military radar equipment. Since automotive PCBS are responsible for transmitting microwave high frequency signals, a substrate with low dielectric loss needs to be used together with the ordinary substrate material PTFE. Unlike FR4 materials, PTFE or similar high-frequency matrix materials require special drilling and feed rates during drilling.
Thick copper PCB
Due to high density and high power as well as hybrid power, automotive electronics bring more heat energy, while electric vehicles tend to require more advanced power transmission systems and more electronic functions, thus placing higher requirements on heat dissipation and large currents.
It is relatively easy to make thick copper double-layer PCBS, and much more difficult to make thick copper multilayer PCBS. The key lies in thick copper image etching and thickness vacancy filling.
The internal path of thick copper multilayer PCB is thick copper, so the graphics transfer photodry film is relatively thick, requiring very high corrosion resistance. Graphic etching time of thick copper will be long, and etching equipment and technical conditions are in optimum condition to ensure complete wiring of thick copper. When external thick copper wiring is manufactured, a combination can be made between a laminated relatively thick copper foil and a graphically thick copper layer, followed by film gap etching. The anti-plating dry film of graphic electroplating is also relatively thick.
The surface difference between the inner conductor and the insulating substrate material of thick copper multilayer PCB is large, ordinary multilayer lamination can not fill the resin completely, and produce the cavity. To solve this problem, thin prepregs with high resin content should be used whenever possible. The copper thickness of the internal wiring on some multilayer PCBS is uneven, and different prepregs can be used in areas where the copper thickness difference is large or small.
Component embedding
In order to increase assembly density and reduce component size, embedded component PCB is widely used in mobile phone, which is also required for other electronic equipment. Therefore, component embedded PCB is also used in automotive electronic equipment.
There are a number of manufacturing methods for component embedded PCBS based on different component embedding methods. There are four main manufacturing methods for component embedded PCB used in automotive electronics, as shown in Figure 1 below.
Of these manufacturing types, the excavation type (Type a in Figure 1) follows the following process: excavation followed by SMD assembly via reflux or conductive glue. The laminated type (Type b in Figure 1) is achieved by backflow through thin SMD components on the internal circuit, or thin component fabrication. The ceramic type (Type c in Figure 1) is a thick-film component printed on a ceramic substrate. The module type (Type d in Figure 1) follows the following steps: SMD assembly via reflux and resin encapsulation. Modular component embedded PCB has relatively high reliability, more suitable for automotive requirements of heat resistance, moisture resistance and vibration resistance.
One of the key functions of automotive electronics lies in entertainment and communication, among which smartphones and tablets require HDI PCBS. Therefore, the techniques contained in HDI PCBS, such as microhole drilling and electroplating and lamination positioning, are used in automotive PCB manufacturing.
So far, with the rapid changes in automotive technology and the continuous upgrading of automotive electronic functions, the application of PCBS will multiply. For engineers and PCB manufacturers, attention must be focused on new technologies and new content so that they can meet higher automotive requirements.
Below is a scenario of existing automotive electronics applications
Then in the future, there will be amphibious flying cars on land and air, and relevant technologies will gradually take shape. We are slowly waiting for the arrival of this day.