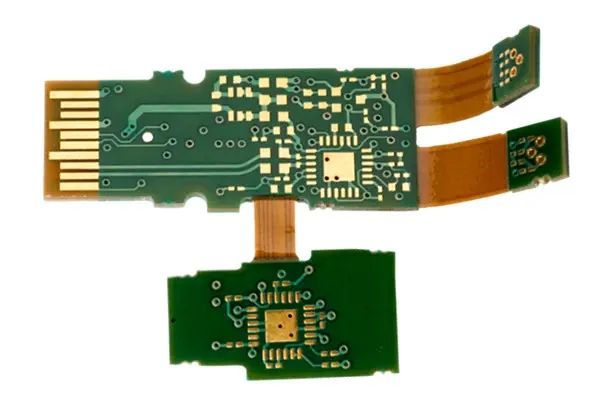
Common Problems of PCB Dry Film and Methods of Identifying PCB
PCB manufacturers, PCB designers and PCBA manufacturers explain the common problems of PCB dry film pasting and the methods of identifying PCB
With the continuous development of the electronic industry and the continuous upgrading of products, in order to save the space of circuit boards, the lines of many circuit boards are already very small when they are designed. The previous wet film can no longer meet the current graphic transfer process. Now, generally, the small lines are produced with dry film. What problems do we have in the film coating process
Summary of common problems and solutions of PCB dry film pasting
01 Bubbles appear between the dry film and the copper foil surface
Bad problem: selecting flat copper foil is the key to ensure no bubbles.
Solution: increase the pressure of PCB film, and handle the board with care.
Bad problems: the surface of the hot pressing roller is uneven, with pits and drilling dirt on the adhesive film.
Solution: Regularly check and protect the flatness of the hot pressing roll surface.
Bad problem: The temperature of PCB film is too high, which causes some contact materials to wrinkle due to temperature difference.
Solution: Reduce the film temperature of PCB.
PCB multilayer circuit board/circuit board
02 Dry film wrinkling
Bad problem: The dry film is too sticky, so place the board carefully during operation.
Solution: In case of contact, handle it in time.
Bad problem: The PCB board is overheated before pasting the film.
Solution: The preheating temperature of the circuit board should not be too high.
03 The dry film is not firmly stuck on the copper foil
Unfavorable problem: the copper foil surface is not cleaned properly, and direct operation will leave oil stain or oxide layer.
Solution: Wear gloves to wash the board.
Adverse problems: The quality of dry film solvent is not up to standard or has expired.
Solution: PCB manufacturers should select high-quality dry films and regularly check the shelf life of dry films.
Bad problems: fast transmission speed, low film temperature of PCB circuit board.
Solution: Change the speed and temperature of PCB film application.
Bad problem: The processing environment humidity is too high, which leads to the extension of the dry film bonding time.
Solution: Keep the relative humidity of the production environment at 50%.
04 Excess glue
Bad problem: poor dry film quality.
Solution: Replace the dry film.
Bad problem: exposure time is too long.
Solution: Have an understanding of the materials used and conduct reasonable exposure time.
Bad problem: Developer failure.
Solution: Change the developer.
Method release time for identifying PCB
Due to the competition of enterprises in the market, the price of PCB materials is also rising. Many manufacturers monopolize the market at a low price in order to improve their market competitiveness. But behind the low price is to reduce the material cost and manufacturing process, which is very bad for the production of PCB materials. Now, I will show you how to identify the quality of PCB.
Distinguish the quality of the circuit board from the appearance
Generally, the appearance of PCB can be analyzed and judged from three aspects;
1. Standard rules for size and thickness.
The thickness of a circuit board is different from that of a standard circuit board. Customers can measure and check according to the thickness and specification of their products.
2. Light and color.
The external circuit boards are covered with ink. The circuit board can play an insulating role. If the color of the board is not bright and there is less ink, the insulation board itself is not good.
3. Weld appearance.
Due to the large number of parts of the circuit board, if the welding is not good, the parts are easy to fall off, which seriously affects the welding quality of the circuit board. Good appearance, careful identification, and a stronger interface are very important.
A good PCB should meet the following requirements
The telephone shall be easy to use after the components are installed, that is, the electrical connection shall meet the requirements;
2. The line width, line thickness and line spacing of the line shall meet the requirements to avoid heating, open circuit and short circuit of the line;
3. The copper skin is not easy to fall off under high temperature;
4. The copper surface is not easy to be oxidized, which affects the installation speed. It will be damaged soon after being oxidized;
5. No additional electromagnetic radiation;
6. The appearance is not deformed to avoid shell deformation and screw hole dislocation after installation. Now it is mechanized installation, and the hole position of the circuit board and the deformation error between the circuit and the design should be within the allowable range;
7. High temperature, high humidity and special environment resistance should also be considered;
8. The mechanical properties of the surface shall meet the installation requirements;
PCB manufacturers, PCB designers and PCBA manufacturers will explain the common problems of PCB dry film pasting and the methods of identifying PCB.