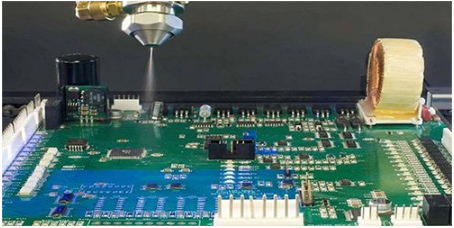
In the process of making PCB, have you ever encountered the problem of poor tin eating on PCB? For PCB engineers, once a piece has a bad tin problem, it often means that it needs to be re welded or even re welded. The consequences are very painful. So, what are the reasons for the poor tin eating of PCB? How can we avoid this problem?
Generally, the main reason why the PCB board has poor tin eating is that there is no tin on the surface of the circuit. This kind of PCB with poor tin eating is usually shown in reality.
pcb
PCB board with poor tin
There are many reasons for the occurrence of PCB tin eating defects, which can be summarized as follows.
The PCB board surface is covered with grease, impurities and other impurities, or there are grinding particles left on the circuit surface during the manufacturing process of the substrate, or there are silicone oil residues, which will lead to poor PCB tin eating. If the above conditions occur during the inspection, solvent can be used to clean the debris. However, if it is silicone oil, it needs to be washed with special cleaning solvent, otherwise it is not easy to clean.
There is another situation that can also lead to poor tin eating of PCB board, that is, the storage time is too long or the environment is humid during the storage process, and the manufacturing process is not rigorous, so the tin surface of the substrate or parts is oxidized and the copper surface is dark. When this happens, the problem cannot be solved by changing the flux. Technicians must solder again to improve the tin eating effect of PCB.
Insufficient temperature or time is not guaranteed during PCB welding, or the flux is not used correctly, which will also lead to poor PCB tin eating. Generally, the operating temperature of soldering tin is 55~80 ℃ higher than its melting point temperature, and insufficient preheating time will easily lead to poor tin eating. The distribution of flux on the circuit surface is affected by the specific gravity. Checking the specific gravity can also eliminate the possibility of misuse of improper flux due to incorrect labeling of the volume, poor storage conditions and other reasons.
In the process of welding, the quality of the solder material and the cleanliness of the terminal are also directly related to the final results. If there are too many impurities in the solder or the terminal is dirty, it will also cause poor PCB tin eating. During welding, the impurities in the solder can be measured on time to ensure the cleanness of each terminal. If the quality of solder is unqualified, the standard solder needs to be replaced.
In addition to the above mentioned cases, there is another problem similar to the bad tin eating of PCB, that is, tin stripping. PCB board tin stripping mostly occurs on tinned lead substrate, and its specific performance is very similar to that of poor tin eating. However, when the surface of the tin path to be welded is separated from the tin wave, most of the tin already on it will be pulled back to the tin furnace, so the tin withdrawal situation is more serious than the bad tin eating. At this time, the re soldering of the substrate may not necessarily improve. Therefore, once this situation occurs, the engineer must return the PCB to the factory for repair.