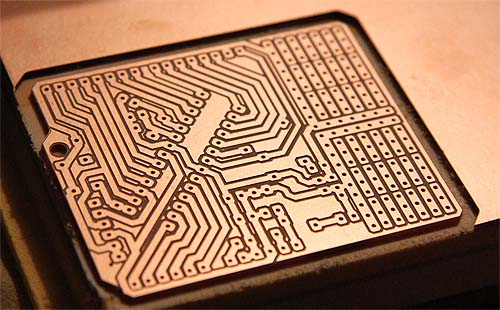
Detailed SMT chip processing and production process
SMT chip processing refers to the process of mounting electronic components and other materials on the bare PCB. It is a popular processing technology in the electronic assembly industry. SMT chip processing process consists of multiple processes, and the process control in the process determines the quality of finished products. Next, we will introduce the SMT chip processing process in detail. 1、 Preparation before SMT chip processing 1. Electronic files of standard circuit diagram of circuit board data (Gerber) shall include at least 4 layers: PAD file, through-hole file, text file and solder mask file; It is better to connect boards provided by PCB manufacturers
SMT chip processing refers to the process of mounting electronic components and other materials on the bare PCB. It is a popular processing technology in the electronic assembly industry. SMT chip processing process consists of multiple processes, and the process control in the process determines the quality of finished products. Next, we will introduce the SMT chip processing process in detail.
1、 Preparation before SMT chip processing
1. Circuit board information (Gerber)
The electronic archives of standard circuit diagram shall at least include 4 layers: PAD file, through hole file, text file and anti welding layer file;
It is better to use the connected board Gerber provided by the PCB manufacturer;
Standard plate edge specification: 10mm plate edge is reserved at the top and bottom respectively;
Specification of standard locating hole: one locating hole on the left and right of the same plate edge, 5mm in diameter from the center of the circle to the plate edge on both sides, 4mm in diameter;
Standard visual marking point specification: 1mm solid tin spraying dot with opposite diagonal asymmetry, 3mm diameter transparent ring of outer ring;
2. Bill of Materials (BOM)
Position coordinates (CAD, text file with extension of ". TXT") installed in electronic files;
List of mixing SMT front and back materials with DIP materials (please provide part coding principles and resolution of front and back parts);
Separate list of SMT front and back materials and DIP materials (please provide the resolution of front and back parts);
Separate list of SMT front/SMT back/DIP materials.
3. Supporting information
Temperature measuring plate (including scrapped plate of important parts);
Empty PCB board, Nordisk Electronics generally adopts Class A PCB board;
Printed steel plate;
32.jpg
2、 Detailed process of SMT chip processing
1. Material procurement, processing and inspection
The material purchaser purchases the materials according to the BOM list provided by the customer to ensure that the production is basically correct. After the purchase is completed, the materials shall be inspected and processed, such as row pin cutting, resistance pin forming, etc. Inspection is to better ensure production quality. Nordea's material procurement is provided by special suppliers, and the upstream and downstream procurement lines are complete and mature;
2. Silk screen
Silk screen printing, or screen printing, is the first process of SMT processing. Silk screen printing refers to the omission of solder paste or paster onto PCB pads to prepare for component welding. With the help of solder paste printing machine, solder paste is infiltrated through stainless steel or nickel steel mesh and attached to the bonding pad. If the steel mesh used for silk screen is not provided by the customer, the processor needs to make it according to the steel mesh document. At the same time, since the solder paste used must be frozen, the solder paste needs to be thawed to a suitable temperature in advance. The solder paste printing thickness is also related to the scraper, so the solder paste printing thickness should be adjusted according to the PCB processing requirements;
3. Dispensing
Generally, in SMT processing, the glue used for dispensing is red glue. Drop the red glue on the PCB to fix the components to be welded and prevent the electronic components from falling or false soldering due to self weight or unfixed during reflow soldering. Dispensing can also be divided into manual dispensing or automatic dispensing, which can be confirmed according to the process needs;
4. Mounting
The placement machine can quickly and accurately mount SMC/SMD components to the designated pad position of PCB without damaging the components and PCB through the functions of absorption displacement positioning placement. The mounting is generally before reflow soldering;
5. Curing
Curing is to melt the patch adhesive and fix the surface mounted components on the PCB pad, generally using thermal curing;
6. Reflow soldering
Reflow soldering refers to the soft soldering that realizes the mechanical and electrical connection between the solder ends of surface mounted components or pins and the PCB pad by remelting the paste solder pre allocated to the PCB pad. It mainly depends on the effect of hot air flow on the solder joints. The colloidal flux can physically react to achieve SMD welding under a certain high temperature air flow;
7. Cleaning
After the welding process is completed, the board surface needs to be cleaned to remove the rosin flux and some tin balls to prevent them from causing short circuits between components. Cleaning is to place the welded PCB board in the cleaning machine, and remove the harmful flux residues on the PCB assembly board surface or the flux residues after reflow welding and manual welding, as well as the pollutants caused in the assembly process.
8. Detection
Inspection refers to the welding quality inspection and assembly quality inspection of PCB assembly board after assembly. AOI optical detection, flying probe tester and ICT and FCT function test are required. QC team conducts spot check on PCB quality, detects substrate, flux residue, assembly failure, etc;
9. Rework
The repair of SMT is usually to remove the components that have lost function, damaged pins or wrong arrangement, and replace them with new ones. The maintenance personnel are required to be familiar with the repair process and technology. PCB boards need to be visually inspected to see if there are missing components, wrong direction, faulty soldering, short circuit, etc. If necessary, the defective boards need to be sent to a professional repair bench for repair, such as ICT test or FCT function test, until the tested PCB works normally.