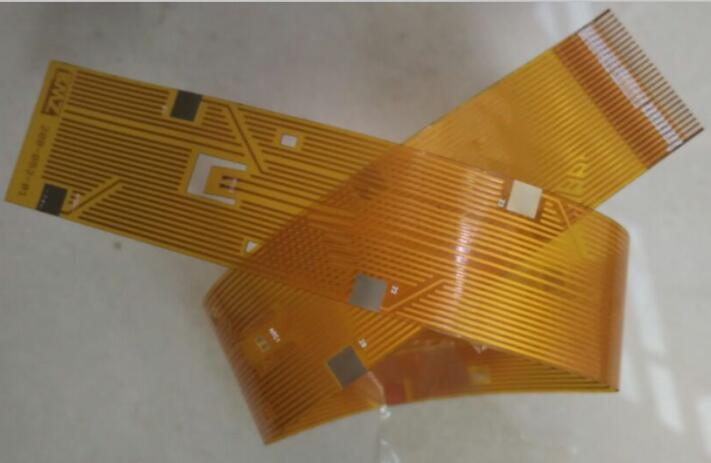
As the carrier plate absorbs heat in the furnace, especially the aluminum carrier plate, the temperature is high when it is discharged, so it is better to add a forced cooling fan at the outlet to help rapid cooling. At the same time, operators need to wear insulating gloves to avoid being scalded by high temperature carrier plates. When taking the FPC that has been welded from the carrier plate, the force should be uniform and no brute force should be used to avoid the FPC being torn or creased.
The removed FPC shall be visually inspected under a magnification of more than 5 times, focusing on problems such as glue residue on the surface, discoloration, gold finger tin, solder beads, empty soldering and continuous soldering of IC pins. Because the surface of FPC cannot be very flat, which leads to a high error rate of AOI, FPC is generally not suitable for AOI inspection, but with the help of special test fixture, FPC can complete ICT and FCT tests.
Because most FPCs are connected boards, it may be necessary to perform board splitting before ICT and FCT tests. Although blade, scissors and other tools can also be used to complete board splitting, the work efficiency and quality are low, and the scrap rate is high. If it is a large-scale production of special-shaped FPC, it is recommended to make a special FPC stamping parting die for stamping segmentation, which can greatly improve the operating efficiency. At the same time, the edges of the FPC blanking are neat and beautiful, and the internal stress generated during stamping and cutting is very low, which can effectively avoid solder joint tin cracking.
In the assembly and welding process of PCBA flexible electronics, the precise positioning and fixation of FPC is the key point, and the key to good or bad fixation is to make a suitable carrier plate. The second is the pre baking, printing, mounting and reflow of FPC. Obviously, the SMT process of FPC is much more difficult than that of PCB hard board, so it is necessary to set the process parameters accurately. At the same time, strict production process management is also important. It is necessary to ensure that operators strictly implement every provision of SOP. The line following engineer and IPQC should strengthen patrol inspection, timely find the abnormal conditions of the production line, analyze the causes and take necessary measures to control the defective rate of FPC SMT production line within dozens of PPMs.
In the process of PCBA production, it is necessary to rely on a lot of machinery and equipment to complete the assembly of a board. Often, the quality level of machinery and equipment in a factory directly determines the manufacturing capacity.
The basic equipment required for PCBA production includes solder paste printing machine, chip mounter, reflow soldering, AOI detector, component leg shearing machine, wave soldering, tin furnace, plate washer, ICT test fixture, FCT test fixture, aging test rack, etc. The equipment provided by PCBA processing plants of different sizes will be different.