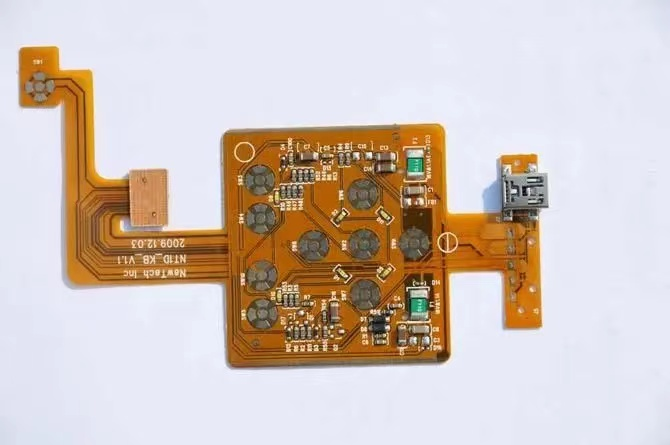
At present, more than 100% of FPC of flexible printed boards are inspected. Of course, in addition to FPC disconnection and short circuit must be checked and there are inspection equipment, there are also many other items for visual inspection. Generally, the lines can be inspected by human eyes or magnified by 2-3 times, but the high-density lines should be inspected by high-power microscope. Inspection 100 μ For lines around m, use a magnifying glass with a magnification of 5~10 times, 50~100 μ A magnifying glass with a magnification of 10-20 times is used for the line of m, 50 μ Lines below m shall be examined with a stereo microscope with a magnification of more than 20 times. It is not that the higher the magnification of the microscope, the better. It is also very important to have a wide field of vision for efficient inspection. Although it is high magnification, the inspection efficiency cannot be improved without electronic image magnification function.
Double sided FPC
The inspection of defects of flexible printed boards with automatic optical inspection instrument (AOI) is still limited to some batch production. The automatic optical tester has been used in the tape rolling process, but the automatic optical tester can only check the defects of the circuit, and can only partially replace the inspectors. Moreover, the flexible circuit is different from the normal digital circuit, and the conventional automatic optical tester cannot be used, and special procedures must be added. It is difficult to adapt to the rapid development of micro lines.
With the high density of the circuit, the magnification of the microscope used will also increase correspondingly, and the inspection time per unit area will also be extended. The proportion of working hours required for flexible PCB inspection is not small, and this proportion will further increase with the further development of the circuit density. When the defect rate decreases, the inspection speed will be accelerated, but the density of lines will continue to develop. From the perspective of inspection, the qualification rate of precision graphic lines will not be significantly improved.
All inspection items of flexible printed boards are not carried out in the final process, especially the inspection of circuit and covered defects in the process is better. The reality is that the inspection in the process can not completely replace the final inspection, but it has a certain effect on improving the efficiency of the entire production.
Processing of FPC reinforcement plate
Adhesives are generally film like, and both sides are protected by release film. Paste the adhesive film of the tear off release film on the reinforcing plate, then process the shape and hole, and then laminated it with the flexible printed board by hot roll lamination. The dimensional accuracy of the shape varies with the materials used. The rigid plates of epoxy glass cloth laminates and paper based phenolic laminates can be machined with CNC drilling and milling machines or molds to form shapes and holes. Polyester and polyimide films can also be simply processed with a knife mold. Generally, the film shaped reinforcement plate does not need to process micro holes, but can be processed with NC drilling and mold. If it can be processed or automated in a short time, the manufacturing cost will be reduced. The process of aligning and positioning reinforcement plates on flexible printed boards with machined shapes and holes is difficult to achieve automation and accounts for a large proportion of the processing cost. Since this operation has to be carried out manually, if a flexible printed board needs multiple reinforcement plates of different materials, the cost will rise. On the contrary, if the design is simple or the use of easily operated clamps, the production efficiency will be significantly improved, Thus reducing the cost. All factories are making efforts to improve this process, but they still need personnel with certain production skills to operate.
The bonding of reinforcing plates includes pressure-sensitive (PSA) and thermosetting, and the labor required for processing is also different. It is very simple to use the pressure-sensitive type. After the release film on the pressure-sensitive type is torn off and aligned with the position on the FPC, it can be pressurized in a short time, even if it is pressed down by hand. When a certain adhesive strength is required, a simple press can be used to apply pressure for several seconds or a hot pressing roller can be used.
The use of thermosetting adhesives is not so simple. Generally, 3~5MPa (30~50kg/cm) is required It must be pressed for 30~60min under the pressure of 60~180 ℃. In order to prevent the flexible printed circuit board from being affected by stress, the pressure on the stiffener must be uniform. If the stiffener is simply pressurized, the end of the stiffener may be broken due to stress.
In addition, the double-sided adhesive film with release film on both sides can be used to bond the flexible printed board, the flexible printed board or the flexible printed board with the rigid printed board, which is equivalent to the semi-solid sheet used for the rigid PCB. Its processing and curing process is the same as the laminate process of the reinforcement board.