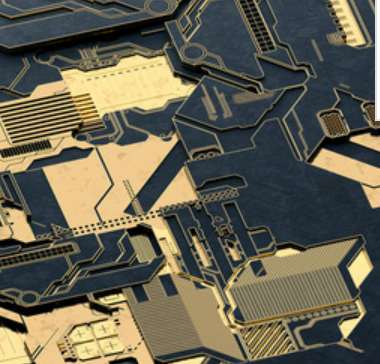
1, the transmission line corner to use 45° Angle, in order to reduce the loss;
2, to use insulation constant value according to the level of strict control of high performance insulation circuit board. This method is beneficial to effectively manage the electromagnetic field between insulation material and adjacent wiring.
3, to improve the high precision etching server PCB design specifications. Consider again specifying a total error of line width of +/-0.0007 inches, managing undercut and undercut of a wiring shape and specifying siding conditions. The overall management of wiring (wire) geometry and coating surfaces is important to the solution of skin effects related to microwave frequencies and to the implementation of these specifications.
4, the presence of tap inductance, to avoid the use of lead components. At high frequencies, surface mounted components are preferred.
5, for the signal hole, to avoid the use of hole machining (pth) process on the sensitive plate, because the process will cause lead inductance at the hole. Lead inductance can affect layers 4 to 19 if a single through hole in a 20-layer board is used to connect layers 1 to 3.
6, to provide rich ground. Molded holes should be used to connect these connections to prevent the influence of 3 - dimensional electromagnetic fields on the circuit board.
7, to choose non-electrolytic nickel plating or plating process, do not use HASL method for plating. This electroplated surface provides a better skin effect for high frequency current. In addition, this highly weldable coating requires fewer leads, helping to reduce environmental pollution.
8, solder resistance layer can prevent the flow of solder paste. However, due to the uncertainty of thickness and the unknown insulation properties, the entire surface of the plate covered with solder resistance material will lead to a large change in the electromagnetic energy of the microstrip design. Generally, welding dam (solderdam) is used as welding resistance layer.
These are the high frequency PCB design tips for PCB interconnect. If you are familiar with these methods, you will understand that the coplanar microstrip design with copper cladding on the back is more economical and practical than the strip design.
What is the high frequency board and high frequency circuit board parameters
The high frequency of electronic equipment is the development trend, especially in the wireless network, satellite communication development, information products to high speed and high frequency, and communication products to large capacity and fast wireless transmission of voice, video and data standardization. Therefore, the development of the new generation of products need high-frequency baseboards, satellite systems, mobile phone receiving base stations and other communication products must be applied to high-frequency circuit boards, in the next few years will develop rapidly, high-frequency baseboards will be in large demand.
The basic characteristics of high-frequency substrate materials are as follows:
(1) The dielectric constant (Dk) must be small and very stable, usually the smaller the better. The transmission rate of the signal is inversely proportional to the square root of the dielectric constant of the material. High dielectric constant is easy to cause signal transmission delay.
(2) The dielectric loss (Df) must be small, which mainly affects the quality of signal transmission, the smaller the dielectric loss, the smaller the signal loss.
(3) Try to be consistent with the coefficient of thermal expansion of copper foil, because inconsistency will cause the separation of copper foil in the change of cold and heat.
(4) Low water absorption, high water absorption will affect the dielectric constant and dielectric loss when wet.
(5) Other heat resistance, chemical resistance, impact strength, peeling strength, etc., must also be good.
In general, high frequency can be defined as frequencies above 1GHz. At present, the most commonly used HF circuit board substrate is fluoromethane substrate, such as polytetrafluoroethylene (PTFE), usually known as Teflon, usually used in 5GHz or above. In addition, there are FR-4 or PPO substrates, which can be used for products between 1GHz and 10GHz. The physical properties of these three high-frequency substrates are compared as follows.
At the present stage, epoxy resin, PPO resin and fluorine resin are used in these three categories of high-frequency substrate materials, the cost of epoxy resin is the cheapest, while fluorine resin is the most expensive; Considering dielectric constant, dielectric loss, water absorption and frequency characteristics, fluorine resin is the best, epoxy resin is worse. When the product application frequency is higher than 10GHz, only fluorine resin printed board can be suitable. Obviously, fluorine resin high frequency substrate performance is much higher than other substrates, but its shortcomings in addition to high cost is poor rigidity, and the coefficient of thermal expansion is larger.
For polytetrafluoroethylene (PTFE), in order to improve the performance with a large number of inorganic substances (such as silica SiO2) or glass cloth as reinforced filling material, to improve the rigidity of the substrate and reduce its thermal expansion. In addition, because of the molecular inertia of PTFE resin itself, it is not easy to combine with copper foil poor, so it is more necessary to combine with copper foil special surface treatment. Treatment methods include chemical etching or plasma etching on the surface of teflon to increase the surface roughness or add a layer of adhesive film between copper foil and teflon resin to improve the bonding force. However, it may have an impact on the performance of the medium. The development of the whole fluorine system high frequency circuit board requires the cooperation of raw material suppliers, research units, equipment suppliers, PCB manufacturers and communication product manufacturers to keep up with the rapid development of the field of high frequency circuit board.