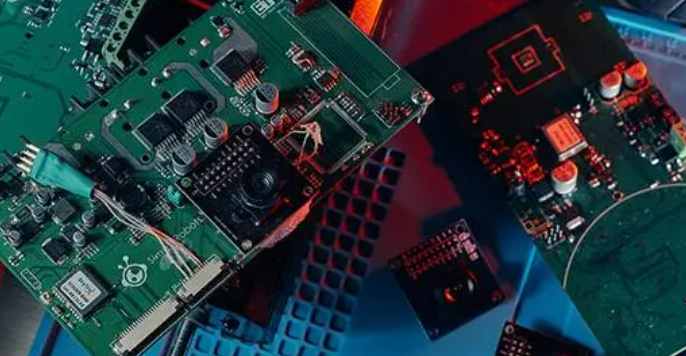
As a new member of the switching power family, LED switching power supply has been widely used in many fields. In the process of new product development, PCB component layout is an important part of the LED switching power supply design, and is also one of the key tests of the engineer's design scheme. So, what can we do to optimize the layout of PCB components?
If you want to have the best PCB component layout for your LED switching power supply, the first thing you need to do before the component layout design is to fully consider the size of the PCB. When the PCB size of the switching power supply is too large, because the printed line is too long, it will lead to the increase of impedance, the decrease of anti-noise ability, and the cost will increase correspondingly. The printed circuit board once too small, heat dissipation is not good, and the adjacent lines are susceptible to interference. Generally speaking, the best shape of the PCB circuit board for LED switching power supply is rectangular, the aspect ratio is 3:2 or 4:3, and the components located on the edge of the circuit board are generally not less than 2mm from the edge of the circuit board.
After the completion of the PCB size design, next we need to consider the distribution parameters between components, which is especially important for circuits operating under high frequency conditions. General circuit should be as far as possible to make parallel components, so that not only beautiful, but also easy to assemble welding, easy to mass production.
When placing PCB board components, do not blindly seek for speed, at this time need to consider the future welding problems comprehensively. This requires the engineer to carry out reasonable component layout, do not put the components too dense. During the design process, the engineer should focus on the core components of each functional circuit and make the overall component layout around the core components. In the process of layout, the components should be arranged evenly, neatly and compact on the PCB to minimize and shorten the leads and connections between the components, and the decoupling capacitor should be as close to the VCC of the device as possible.
In addition, in the PCB component layout of LED switching power supply, it is recommended that engineers arrange the position of each functional circuit unit according to the circuit flow. This layout allows signal flow to be more efficient and fast, and keeps the signal direction as consistent as possible. In the layout of PCB board, the first principle is to ensure the routing rate of the cloth, mobile devices pay attention to the connection of the fly line, the connected devices together. The area of loop is reduced as much as possible to suppress the radiation interference of switching power supply.
Discussion on PCB component layout inspection rules
In the process of PCB layout, after the system layout is completed, the PCB drawing should be examined to see whether the layout of the system is reasonable and whether it can achieve the optimal effect. Generally, it can be investigated from the following aspects:
1. Whether the system layout can ensure reasonable or optimal wiring, reliable wiring and reliability of the circuit. In the layout of the need to signal direction and power and ground network have an overall understanding and planning.
2. Whether the size of the printed board is consistent with the size of the processing drawings, whether it meets the requirements of the PCB manufacturing process, and whether there is a behavior mark. This point needs special attention, many PCB board circuit layout and wiring are designed very beautiful and reasonable, but the precise positioning of the positioning plug-in is neglected, resulting in the design of the circuit can not be connected with other circuits.
3. There is no conflict between components in two-dimensional and three-dimensional space. Note the actual size of the device, especially the height of the device. In the welding of non-layout components, the height is generally not more than 3mm.
4. Whether the component layout is dense and orderly, arranged neatly, and whether all the cloth is finished. In the layout of components, it is not only necessary to consider the direction and type of signals, the places that need attention or protection, but also to consider the overall density of the device layout, so as to achieve uniform density.
5. The components that need to be replaced frequently can be easily replaced, and the plug-in board can be easily inserted into the equipment. The convenience and reliability of the replacement and insertion of frequently replaced components shall be ensured.
6. Whether it is convenient to adjust adjustable components.
7. Whether there is an appropriate distance between the heat sensitive element and the heating element.
8. Whether the heat sink or fan is installed in the place that needs heat dissipation, and whether the air flow is smooth. Pay attention to the heat dissipation of components and circuit boards.
9. Whether the signal direction is smooth and the interconnection is shortest.
10. Plug, socket and mechanical design is contradictory.
11. Whether the interference problem of the line has been considered.
12. Whether the mechanical strength and performance of the circuit board have been considered.
13. The artistry and aesthetics of circuit board layout.