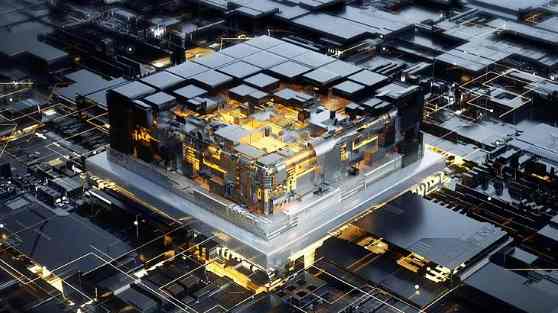
▪ The plugging action of connectors should be smooth and the socket should not be too close to other components.
▪ Component layout should consider the balance of the center of gravity. The center of gravity of the entire board should be close to the geometric center of the PCB. The center of gravity should not be allowed to drift to the edge of the board (1/4 area).
3, plug-in, welding and material turnover quality requirements for device layout
The different requirements for the device layout are put forward in the aspect of quality.
▪ Similar components are oriented in the same direction on the circuit board (e.g. diodes, leds, electrolytic capacitors, receptacles, etc.) so that plug-ins are errless, beautiful and productive.
▪ Horizontal design should be adopted for 220 package regulator tubes (especially those close to the edge of the plate), such as 7805/7812, which do not need heat sink, in order to prevent the element foot or copper skin from being broken by external forces during the process and transfer, handling, inspection and assembly.
▪ Metal-clad crystals, designed as horizontally as possible to withstand shocks and secured with glue.
▪ The orientation of the long axis of the patch element (especially the thicker patch element) should be as perpendicular as possible to the forward direction of wave soldering to avoid shadow areas as far as possible.
▪ As far as dual panels are concerned: SMT components for the solder paste process are prefered to be designed on the plug-in component surface, while for the red glue process, the plate is designed on the wave soldering surface as far as possible.
For patch components. The spacing between adjacent components and pads should not be too close. It is recommended to design according to the following principles.
(1) The distance between PLCC, QFP and SOP and each other is not less than 2.5mm.
(2) The spacing between PLCC, QFP, SOP and Chip and SOT is not less than 1.5 mm.
(3) Spacing between Chip and SOT ≥ 0.7mm.
▪ Multi-core socket, connecting wire group, foot spacing intensive double row foot manual plug-in IC, the long side direction must be parallel to the direction of the wave crest, and the front and back of the most next to the foot to increase the false pad or increase the area of the original pad, in order to absorb the trailing solder to solve the welding problem. As shown below:
▪ If the OFP and PLCC integrated blocks pass the crest by red glue process, they should be placed at a 45 degree bevel, and the last pin of each side should be added with a stolen tin pad;
4. Creepage distance and electrical clearance shall meet the requirements of GB4706.1-1998.
▪ When 130V < operating voltage ≤250V, no anti-dust ability conditions, electrical insulation gap between different phases ≥2.5mm, creepage distance ≥3.0mm, basic insulation (between strong and weak electricity) electrical gap ≥3.0mm, creepage distance ≥4.0mm, groove width should be greater than 1mm, the length of the groove should ensure creepage distance meet requirements.
5, the device layout should meet the requirements of fire protection design specifications.
▪ The heat dissipation effect of high-power components must be considered, and must be placed in a position with good heat dissipation effect.
▪ There should be a gap of more than 2mm between the high-power resistor body and the surrounding components body. In principle, the high-power resistor should be designed in elevated horizontal mode.
6. Device layout shall meet the requirements of EMC design specifications.
▪ Cell circuits should be placed as close together as possible.
▪ Devices sensitive to temperature characteristics should be kept away from power devices.
▪ Key circuits, such as reset and clock devices, should be kept away from high-current circuits.
▪ The decoupling capacitor should be close to its power supply circuit.
▪ The circuit area should be minimum.
Two, PCB manufacturing process on the welding pad requirements
▪ Test points should be added if the two ends of the patch components are not connected to the plug-in components. The diameter of the test points should be equal to or greater than 1.8mm for on-line testing.
▪ IC foot pad with dense spacing should be tested if it is not connected to the hand plug-in pad. If it is patch IC, the test point should not be placed in the patch IC screen printing. The diameter of the test point is equal to or greater than 1.8mm to facilitate online tester testing.
▪ If the spacing between pads is less than 0.4mm, white oil should be applied to reduce the continuous welding over the crest.
▪ The ends and ends of the patch components should be designed with tin guides. The width of the guide wire is recommended to be 0.5mm, and the length is generally 2 or 3mm.
▪ If a single panel has a hand welding component, the direction of the tin slot should be opposite to the direction of the tin, and the width of the hole should be 0.3MM to 1.0MM; (50-70% of the aperture) as shown below:
▪ The spacing and size of conductive rubber keys should be consistent with the actual size of conductive rubber keys, and the PCB board connected with this should be designed as gold fingers, and the corresponding gold-plated thickness should be specified.
▪ The size and spacing of the pad should be the same as that of the patch component (1:1).
▪ For solder joints with a distance of less than 0.4mm between pads (more than 4 pads) on the same straight line, on the basis of adding white oil, the long side of the element is as parallel as possible to the direction of wave crest, then add an empty pad at the end of the pad or increase the end of the pad, so as to eat the trailing solder to reduce the welding.