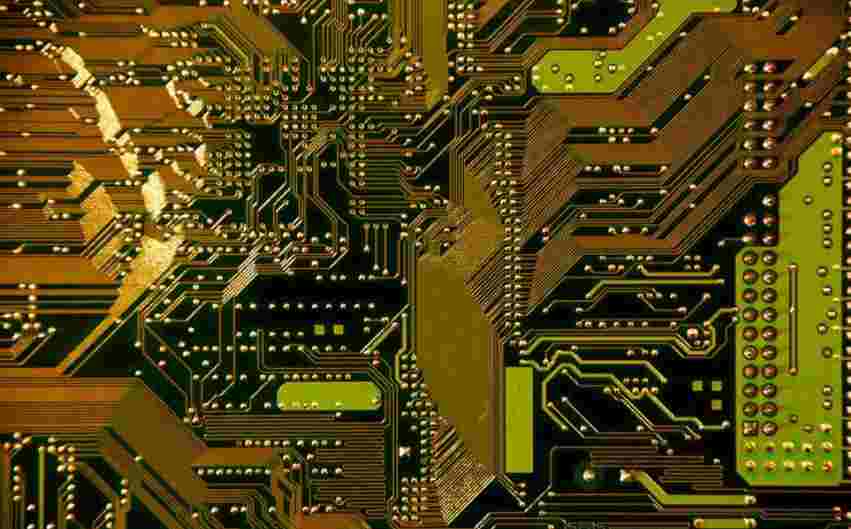
Regardless of the manufacturing process, manufacturing tolerances must be considered: including raw materials such as substrates and copper foils, as well as PCB manufacturingprocesses. In addition to differences from batch to batch and from panel to panel, tolerances are generally considered global, however, they are also local. The effective dielectric constant (Eref) of the substrate varies locally due to heterogeneous dielectric and copper foil. The structure itself also affects the outcome. For example, the position of the through-hole can affect the consistency of the plating, causing uneven currents while several layers of composite copper percentage changes
Local peaks and valleys may be produced, resulting in highly irregular effective substrates after pressing. The manufacture of printed circuit boards introduces local differences in etching/plating flow patterns depending on the direction.
One of the metrics that designers focus on is the ereff of the design object. For example, consider a PCB patch array for a 77GHz mid range radar for cars. The slope of the elevation pattern will vary according to the Erefr. A 1% change in the dielectric constant of the patch antenna string is equivalent to a 0.74 degree tilt.
Any changes to the designed circuit board can be optimized by building one or more prototypes. The fabrication tolerances of the substrate and PCB are known and controlled within a range that can be included in the simulation to achieve centralization of the design. However, these controls may not be completely relevant to the conditions experienced by RF devices. Substrate dielectric is self measured and controlled, copper foil is self controlled, both are point sampled. PCB manufacturing is controlled by verifying the specific dimensions of discrete locations. But what is the overall change in key parameters within a panel?
To assess these effects, a 16x16 ring resonator grid was measured on a typical RF substrate, forming a detailed distribution map of the Ereff. The average was 2.47, and the rate of change was ±1.4%. An antenna array fabricated on the substrate can be located in any position and orientation on the panel. Although each patch in an antenna is small compared to the entire antenna, the range of effective permittivity varies depending on placement. It may be more useful to know how the average Eref varies across the array. This can be worked out by placing the antenna in all possible positions and orientations, and calculating the average ereff under the array preferably including important edge fields. In this calculation, the antenna arrays overlap at 45 degrees and the mean ereff is 2.47, a variation of ±0.9%.
To sum up, the overall range of eref variation for a small component such as a single 77GHz antenna patch is 2.47±1.4%, while the entire array averages 2.47±0.9%. As an entity, the array varies significantly less on average. Similarly, erefr variation will be further reduced for all transmitting (Ex) and receiving (Rx) antenna combination systems. Local changes are the product of all factors, such as local changes in copper foil and substrate dielectric, PCB manufacturing process and board structure. Variations and tolerances in localization, from batch to batch, and from panel to panel depend on the specific materials and processes used, but tolerances are always present.
The permittivity measured from a ring resonator may not exactly correspond to the values experienced by antennas or other circuits. Again, any measurement has some tolerance and repeatability. In this experiment, the reproducibility of the measurement was determined to be ±0.3%. The averages developed for millimeter-wave patch antennas discussed here may not fully describe the performance variation of another millimeter-wave circuit, nevertheless, this example illustrates the concepts.
When designing an RF system, the manufacturing process must be selected to suit the system needs. Material and processing tolerances, batch to batch, panel to panel, and internal panel tolerances must be considered. Often, there are other system considerations that may affect the manufacturing process and the resulting tolerances. For example, the RFIC can be placed on the antenna side or opposite side of the PCB.
The use of through-holes to transmit signals to different layers is very common. The mismatch caused by the high impedance of the through-hole structure and the parasitic effect of the through-hole stub are very important in millimeter waves. stub reduction and additional matching are often required to compensate, and full three-dimensional electromagnetic (EM) simulation is used to verify performance. The manufacturing tolerance of all parameters should be considered at the beginning of the design.
In many millimeter-wave radars with frequencies higher than 60GHz, radiation from the through-hole structure must be prevented. A dense earthing through-hole ring is usually placed around the signal through-hole to provide earthing shielding, contain the electromagnetic field within a quasi-coaxial structure, and minimize radiation loss. However, these ground through-holes may shorten the line and block the route of the signal to and from the center signal through-hole. A through-hole structure and its PCB stack conducting 76-81GHz signals from bottom to top in automotive radar are shown. Six electroplated through-holes around the center signal hole serve as grounding through-holes. However, they do not provide adequate shielding at high frequencies and require two additional embedded through-holes to close
Clearance, without short-circuiting the wire. If these buried holes are removed, the insertion loss and return loss will rise significantly.
The tolerance of through-hole transition is studied. It includes fabrication tolerance of etching, through-hole registration, through-hole diameter, and changes in dielectric material thickness and dielectric constant. Taking into account all manufacturing variations, tolerance studies help ensure that RF performance meets system requirements.
As mentioned earlier, embedded through-holes require additional lamination, drilling, and plating, and these additional processes can significantly increase manufacturing costs. Surface mount (SMT) cross components can be applied to single layer panels to achieve the same effect and reduce manufacturing complexity.