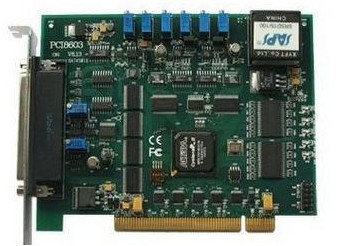
The electromagnetic interference of electronic system not only comes from the radiation of electric field and magnetic field, but also from the common impedance of the line, the vehicle coupling between conductors and the circuit structure. When developing and designing circuits, we also hope that the printed circuit board designed will not be easily affected by external interference as much as possible, and that it will also interfere with other electronic systems as little as possible. There are many factors that affect the anti-interference performance of PCB, including the thickness of copper foil, the width and length of printed wire and the crosstalk between adjacent wires, the rationality of the layout of components in the board, the common impedance of the wire, the electromagnetic field generated by the wire and components in space, etc.
The primary task of PCB design is to analyze the circuit and determine the key circuit. This is to identify which circuits are interference sources and which circuits are sensitive circuits, and find out which paths interference sources may interfere with sensitive circuits. In analog circuits, low-level analog circuits are often sensitive circuits, and power amplifiers are often interference sources. When the working frequency is low, the interference source mainly interferes with the sensitive circuit through the barrel closing between lines; When the operating frequency is high, the interference source mainly interferes with the sensitive circuit through electromagnetic radiation. In digital circuits, high-speed repetitive signals, such as clock signals and bus signals, contain rich frequency components, which are the largest interference source and often pose a threat to sensitive circuits. Reset circuit, interrupt circuit, etc. are sensitive circuits, which are vulnerable to peak signal interference, so the digital circuit cannot work normally. The input/output circuit (1/0) is connected to the outside world, which should also be paid special attention to. If the UO circuit is close to the clock line and other interference sources, the unwanted high-frequency energy will be connected to the output wire, and the noise on the wire will interfere with the sensitive circuit near the cable through radiation or conduction.
On the basis of fully analyzing the circuit and determining the key circuit, the circuit must be properly arranged on the printed board. For example, for digital circuits, high-speed circuits (such as clock circuits, high-speed logic circuits, etc.), medium and low speed logic circuits and UO circuits should be arranged in different areas, and the interference sources and sensitive circuits should be separated as far as possible in space, which can greatly reduce the radiation interference of interference sources on sensitive circuits.
2. Anti interference design of printed board
The purpose of anti-interference design of PCB board is to reduce the electromagnetic radiation of PCB board and the crosstalk between circuits on PCB board. In addition, the ground wire design of PCB also directly affects the common mode voltage radiation of 1/0 cable. Therefore, the anti-interference design of PCB is of great significance to reduce the electromagnetic information radiation of the system.
2.1 PCB layout design
The density of printed circuit board (PCB) is getting higher and higher, and the anti-interference ability of PCB design has a great impact, so the layout of PCB is in a very important position in the design.
Layout requirements for special components:
1. The shorter the connection between high-frequency components, the better, to minimize mutual electromagnetic interference; Components susceptible to interference shall not be too close to each other; Input and output elements should be as far away as possible;
2. Some components have high potential difference, so the distance between them should be increased to reduce common mode radiation. Special attention shall be paid to the rationality of the layout of components with high voltage;
3. The thermal element shall be far away from the heating element;
4. The vehicle release capacitor shall be close to the power supply pin of PCB chip;
5. The layout of adjustable components such as potentiometers, adjustable inductors, variable capacitors, microswitches, etc. shall be placed at the position convenient for adjustment as required;
6. The position occupied by the positioning hole and fixing bracket of the printed board shall be reserved.
Layout requirements for common components:
1. Place the components of each functional circuit unit according to the circuit flow to make the signal flow direction as consistent as possible;
2. The core components of each functional circuit shall be taken as the center and arranged around it. The components shall be evenly and orderly arranged on the PCB to minimize and shorten the leads and connections between components;
3. For the circuit working at high frequency, the interference between components shall be considered. Generally, the components shall be arranged in parallel as far as possible to facilitate wiring;
4. The distance from the PCB's outlet line to the edge of the circuit board is generally not less than 80 mil. The optimal shape of the circuit board is rectangle. The aspect ratio is 3:2 or 4:30.
2.2 PCB wiring design
The wiring density of PCB is increasing, so the wiring design of PCB is particularly important.
1. The power line layer of the four layer board shall be as close as possible to the ground wire layer to obtain the minimum power impedance. From top to bottom: signal line, ground line, power line and signal line. In consideration of electromagnetic compatibility, the six layer board from top to bottom should preferably be: signal line, ground wire, signal line, power line, ground wire, signal line;
2. The clock line shall be adjacent to the ground layer, and the line width shall be increased as much as possible. The line width of each clock line shall be consistent;
3. The signal layer adjacent to the ground wire is laid with high-speed digital signal lines and low-level analog signal lines, and the remote layer is laid with low-speed signal lines and high-level analog signal lines;
4. The wiring of input and output terminals shall avoid adjacent parallelism as far as possible to avoid feedback vehicle merging;
5. 135 ° obtuse angle is generally taken at the bend of printed wire;
6. The line width of power line and ground wire shall be increased as much as possible, and the wiring width of devices with 0.5mm pin spacing shall not be less than 12ml;
7. In general, the width of digital circuit signal line is 8.il-10nul, and the spacing is 6mi1-8mil;
8. The lead of the radiation release capacitor shall not be too long, especially the lead of the high-frequency bypass capacitor;
9. The digital ground and analog ground on the mixed signal circuit board are separated. If the wiring crosses the separation gap, the electromagnetic radiation and signal interference will increase sharply, resulting in electromagnetic compatibility problems. Therefore, PCB design generally adopts a unified, partitioned PCB layout and wiring through digital circuits and analog circuits;
10. For some high-speed signals, differential pair wiring can be used to reduce electromagnetic radiation.
3 Test cases
Here are some practical examples to illustrate the interference caused by different reasons and the practical solutions.
3.1 Interference caused by power line and ground wire
Some circuits of an outsourced high-voltage control and protection PCB. (a) It is the original design circuit. Because the width of the printed wire of the power line and ground wire is too thin, the circuit is subject to external interference during operation; And (b) is an improved circuit. Its power line and ground wire are thickened to 5mm, which solves the interference problem of the circuit.
3.2 Interference caused by unreasonable component layout
Part of the circuit of the magnetic field control and protection PCB of a radar transmitter. The improved PCB circuit (b) has a great improvement in anti-interference performance compared with the original PCB circuit (a).
3.3 Interference caused by unreasonable wiring
The above figure is taken from some circuits of the CFA power control and protection PCB of a radar. (a) It is the original design circuit. When wiring, the high-voltage sampling signal line is laid in the closed-loop sampling circuit, which makes the closed-loop sampling circuit vulnerable to external interference during operation, causing frequent false alarm of overvoltage fault; And (b) is the improved PCB circuit. Because it avoids the interference caused by the high-voltage sampling signal line, the improved PCB circuit works reliably and stably.