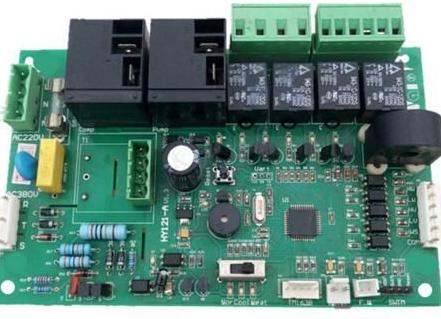
The development and change of electronic technology will inevitably bring many new problems and challenges to board level design. First of all, due to the increasing physical limit of high-density pins and pin sizes, low throughput is caused; Secondly, the timing and signal integrity problems caused by the improvement of the system clock frequency; Third, PCB engineers hope to use better tools to complete complex high-performance designs on the PC platform. From this, we can easily see that PCB design has the following three trends:
The design of high-speed digital circuits (i.e., high clock frequency and fast edge rate) has become the mainstream.
The miniaturization and high performance of products must face the problem of distribution effect caused by mixed signal design technology (i.e. digital, analog and RF mixed design) on the same PCB.
The improvement of design difficulty leads to that the traditional design process and design method, as well as the CAD tools on PC, are not competent for the current technical challenges. Therefore, the transfer of EDA software tool platform from UNIX to NT platform has become a recognized trend in the industry.
(2) High frequency PCB wiring skills
High frequency circuits often have high integration and high wiring density. Multilayer boards are necessary for wiring and an effective means to reduce interference
The lead between pins of high frequency circuit components should be bent as little as possible. The lead of high frequency circuit wiring should be full straight line, which needs to be turned, and can be turned by 45 ° broken line or arc. This requirement is only used to improve the fixation strength of copper foil in low frequency circuit, while in high frequency circuit, meeting this requirement can reduce the external transmission and mutual coupling of high frequency signals
The shorter the lead of high-frequency circuit device pin, the better
As far as possible, the less lead layer alternation between pins of high-frequency circuit components is, the better. That is, the less vias (Via) used in the component connection process are, the better. It is measured that one vias can bring about about 0.5pF distributed capacitance, and reducing the number of vias can significantly improve the speed
For high frequency circuit wiring, pay attention to the crosstalk introduced by the parallel routing of signal lines in short distance. If the parallel distribution cannot be avoided, a large area can be arranged on the reverse side of the parallel signal lines to greatly reduce the interference. Parallel routing in the same layer is almost unavoidable, but the direction of the routing in the adjacent two layers must be perpendicular to each other
Measures to enclose signal lines or local units of special importance with ground wires
The routing of various signal lines cannot form a loop, nor can the ground wire form a current loop
At least one high-frequency decoupling capacitor shall be set near each integrated circuit block (IC), and the decoupling capacitor shall be close to the Vcc of the device as far as possible
When analog ground wire (AGND), digital ground wire (DGND), etc. are connected to the common ground wire, high-frequency choke should be used. When actually assembling the high-frequency choke link, high-frequency ferrite beads with conductors in the center are often used, which can be regarded as inductors in the schematic diagram, and a component package should be separately defined for it in the PCB component library. Before wiring, it should be manually moved to a suitable location close to the common ground wire
(3) EMC design method in PCB
The selection of PCB substrate, the setting of PCB layers, the selection of electronic components and the electromagnetic characteristics of electronic components, the layout of components, and the length and width of interconnects between components all restrict the electromagnetic compatibility of PCBs. The integrated circuit chip (IC) on a PCB is the main energy source of electromagnetic interference (EMI). Conventional electromagnetic interference (EMI) control technologies generally include: reasonable layout of components, reasonable control of wiring, power lines, grounding The reasonable configuration of filter capacitors, shielding and other measures to suppress electromagnetic interference (EMI) are very effective, and are widely used in engineering practice
1. Wiring rules in electromagnetic compatibility (EMC) design of high-frequency digital circuit PCB
High frequency digital signal line shall use short line, generally less than 2inch (5cm), and the shorter the better
The main signal lines should be concentrated in the center of PCB board
The clock generation circuit shall be near the center of PCB board, and the clock fan out shall be daisy chain or parallel wiring
The power line shall be as far away from the high-frequency digital signal line as possible or separated by the ground wire. The distribution of power supply must be low induction (multi-channel design). The power layer in the multilayer PCB board is adjacent to the stratum, equivalent to a capacitor, which plays a filtering role. The power line and ground wire on the same layer shall also be as close as possible. The copper foil around the power layer shall be 20 times smaller than the stratum, which is the size of the distance between two plane layers, To ensure better EMC performance of the system, do not divide the ground plane. If the high-speed signal line is to be divided across the power plane, several low impedance bridge capacitors should be placed close to the signal line
The wires used at the input and output terminals shall not be parallel to each other as much as possible. It is better to add ground wires between lines to avoid feedback coupling
When the thickness of copper foil is 50um and the width is 1-1.5mm, the wire temperature is less than 3 ℃ when passing the current of 2A. The wire of PCB board should be as wide as possible. For the signal wire of integrated circuit, especially digital circuit, the wire width of 4mil-12mil is usually selected, and the wire width of power line and ground wire should be greater than 40ml. The minimum distance between wires is mainly determined by the insulation resistance between wires and breakdown voltage in the worst case, Generally, conductor spacing of more than 4mil is selected. To reduce crosstalk between conductors, the distance between conductors can be increased if necessary, and ground wires are inserted as line to line isolation
In all layers of the PCB board, digital signals can only be wired in the digital part of the circuit board, and analog signals can only be wired in the analog part of the circuit board. Single point parallel grounding should be used as far as possible for the grounding of low-frequency circuits. When the actual wiring is difficult, part of the circuit can be connected in series and then connected to the ground. The division of analog and digital power supplies can be realized, and the wiring cannot span the gap between the divided power supplies, The signal lines that must cross the gap between the split power supplies shall be located on the wiring layer adjacent to the large area of ground
There are mainly two kinds of electromagnetic compatibility problems caused by power supply and ground in PCB, one is power supply noise, the other is ground wire noise. According to the size of PCB current, try to increase the width of power line and reduce the loop resistance. At the same time, make the direction of power line and ground wire consistent with the direction of data transmission, which helps to enhance the anti noise ability. At present, The noise of power supply and ground plane can only be measured by prototype products or the capacity of decoupling capacitor can be set as the default value by experienced engineers based on their experience
2. Layout rules in electromagnetic compatibility (EMC) design of high-frequency digital circuit PCB
The circuit layout must reduce the current loop and shorten the wiring between high-frequency components as much as possible. The components that are vulnerable to interference should not be too close, and the input and output components should be as far away as possible
Arrange the position of each functional circuit unit according to the circuit flow, so that the layout is convenient for signal flow and the signal is kept in the same direction as far as possible
The core components of each functional circuit shall be taken as the center and arranged around it. The components shall be evenly, neatly and compactly arranged on the PCB to minimize the lead connection between components
Divide PCB into independent and reasonable analog circuit area and digital circuit area, and place A/D converter across different areas
One of the common methods of PCB EMC design is to configure appropriate decoupling capacitors in each key part of the PCB
(4) Signal integrity (SI) analysis
Signal Integrity (SI for short) refers to the quality of the signal on the signal line and the ability of the signal to respond with correct timing and voltage in the circuit
High switching speed of integrated circuit chips (ICs) or logic devices, incorrect PCB layout of termination components, or wrong wiring of high-speed signals will cause signal integrity problems such as reflection, crosstalk, overshoot, undershoot, ringing, etc., which may cause the system to output incorrect data, and the circuit to work abnormally or even completely
Signal Integrity and Design of PCB
In PCB design, PCB designers need to integrate the layout and wiring of components and what SI problem solving methods should be used in each case to better solve the signal integrity problem of PCB. In some cases, the selection of IC can determine the number and severity of SI problems. Switching time or edge rate refers to the rate of IC state transition. The faster the IC edge rate, the higher the probability of SI problems, It is important to terminate components correctly
A common way to reduce signal integrity problems in PCB design is to add terminating components on the transmission line. In the termination process, we should balance the requirements of the number of components, signal switching speed and circuit power consumption. For example, adding terminating components means that PCB designers have less space for wiring, and it will be more difficult to add terminating components in the later stage of layout processing, Because space must be reserved for new components and wiring, it should be made clear at the beginning of PCB layout whether to place termination components