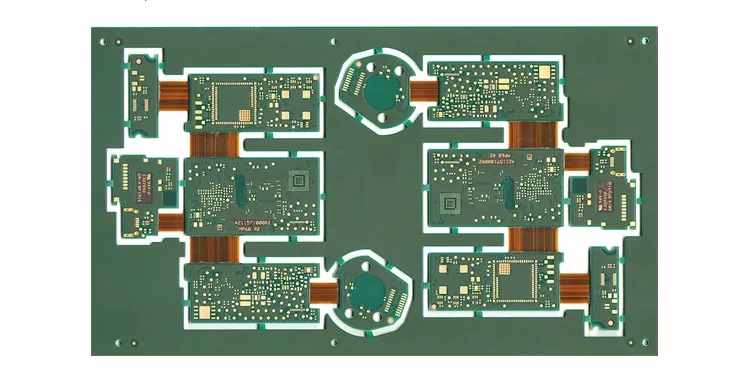
Switching Power Supply Output Filter for PCB Design: Design and Simulation
Switching power supply has many forms, such as in high-power desktop laboratory power supply, or embedded in PCB through special IC and passive components. These systems are designed to ensure that stable DC power is delivered to the rest of the system with minimal noise. It is also ideal to attenuate the effect of any residual ripple from the rectifier or eliminate any noise on the input. To keep the output noise free and stable, it may be necessary to use an output filter, which can be implemented using passive components in PCB layout.
I show how to use switching power supply output filters to suppress output noise, and how to use some simulation tools to optimize filter design to reduce noise. The noise reduction depends on the element value in the output filter and the inductor value in the circuit. As an example, let's take a look at the buck boost converter topology to understand how to implement an output filter for a switching power supply.
Design of Output Filter for Start Switching Power Supply
The output filter on a DC/DC converter (buck/boost or other topology) is a low-pass filter. Although the typical method is to place a pi filter to divert AC noise to ground, this can be as simple as a shunt capacitor. The reason for this is that the function of the switching converter is to convert the low-frequency ripple generated by AC-DC power conversion into the high-frequency switching noise generated by switching transistors. Then, the output filter will eliminate the high-frequency switching noise on the filter output, thus providing a clean DC power supply for the load.
Finally, we have the following parameters on PWM: 100 kHz switching frequency, 10 ns rise time, 30% duty cycle. Rather than focusing on the allowable range of PWM or passive values that give a specific power output, focus on the range of filter component values that minimize noise.
Initial power output
In fact, the transient overshoot depends on the PWM duty cycle and the rise time of the PWM signal. In some cases, when the converter switches between two voltage states, that is, between two PWM frequencies or duty cycles, the overshoot may be as high as 50% of the load current. This may produce large current spikes, which may damage your load.
The value of the load component will also affect the output ripple in the circuit. In the figure below, I show what happens when the load resistance increases to 1 MOhm, which is a useful value for analog CMOS integrated circuit input impedance. From here, we can see the real ripple on the output, which is reflected in the load current.
Ripple load is 1 MOhm.
Therefore, we hope to attenuate the response from the converter circuit, or redesign the filter part to avoid such problems when the output overshoot occurs. One option is to add some damping directly by adding some resistance.
Add resistance for damping
One way to solve the problem of insufficient transient response is to add some damping to capacitors C1 and C2. To this end, I added 1 Ohm resistor to capacitors C1 and C2 to provide some damping, and I am driving a 10 Ohm load. This will bring the transient response very close to the critical damping state and provide a smooth transition between OFF and ON states at the beginning of the simulation. If the PWM parameters are changed, the same smooth transition occurs between the two power supply output states. However, if the resistance is high, the transient response will be slower.
A small problem with this is that we lose a small amount of power: less current flows to the load, and the output voltage is slightly lower. Some power drops on the resistance of the RC part, resulting in some additional losses. Although the current is small, there will be some slight residual noise on the output current.
If we use a load of 1 MOhm, we will get the same response, but we will see some initial ripple in the voltage drop on the C1+(series resistance) network. This is a good response, because the ripple will not reflect to the output, but there is still the same slow output current rise. If you do not need to adjust very quickly through the feedback loop and want to ensure smooth transfer between states, you can do so.
Before continuing, I think it must be noted that although the response speed is much slower, we will quit~95% of the expected final current in about 3 ms, which is still a fairly fast opening time. For comparison purposes only, some commercial power supplies have a rated total on time of 10 times. The on time may be dominated by other components, such as PWM drivers, especially if a feedback loop provides precise control. So even if the opening time seems slow, we can still run fast enough.
One option here is to redesign our switching power supply output filter circuit without increasing the resistance to produce similar results.
Change C1, C2 and/or L2
Another option here is to delete the resistor and change C1/C2 and L2. The problem with modifying C1 and C2 is that when you modify the critical damping conditions, the final ripple at the output will be affected by the values of these capacitors. The condition for generating critical damping is a rather complex quadratic expression, but the intuition should be clear here:
If the value of the capacitor is too low, the high-frequency oscillation will produce a serious insufficient damping response.
If the capacitor value is too high, our response will be very slow, because it takes a long time for the capacitor to be charged to the required DC level.
You may want to know; How do we generate overshoot transient responses in pi filters? In fact, because there are multiple reactance elements (2 inductors and 2 capacitors), we have 2 LC filters with multiple poles in the combined transfer function. If we carefully observe the above results, we can see that the two transient responses are superimposed on each other. These are switching LC responses from L1 and C1 (standard buck boost converter responses), and typical RLC responses from L2, C2, and load resistors.
Adjusting L2 and output capacitor together is another way to obtain low output ripple. In the following figure, I created a frequency sweep in the Analog Dashboard to move between a series of inductance values. Here, I want to limit the actual inductance I will find in smaller components when driving a 10 Ohm load. To ensure that I am as close to the critical damping as possible, I will traverse the different values of C1=C2 and L2. I started with a small capacitance (1 uF) and then scanned the value of L2 to 0.2 mH. For 1 MOhm load, just follow the same steps using the key damping conditions in the RLC circuit.
It has been proved that the optimal inductance value of L2 is about 150-200 uH. There are many wire wound inductors whose DC current rating exceeds 〜 1.5A. Vishay's IHV30EB150 is an example.
A range of L2 values and a power output of a 10 ohm load.
Filter Policy Summary
What have we learned here? We have gained some insights from these simulations and can draw several suggestions from them:
Your filter design largely depends on the output capacitor value of the converter. If the output capacitor is too small, an additional capacitor needs to be connected in parallel to make the cut-off frequency small enough to provide noise filtering.
We only study the output filter, but putting the filter on the input is usually more effective for reducing the total noise. Basically, this is what you do with the output capacitor on the full wave rectifier: you are trying to feed a stable DC power supply into the power conversion part of the power supply.
There is an excessive phenomenon in the transient response of pi filter, which may be very large. This can be damped in the usual way by placing the resistance in series with capacitors C1 and C2 or adjusting the value of L2.
When adding damping, make sure to compare the required resistance with the ESR value of the capacitor used. Also note that you will slow the response of the circuit and sacrifice some power.
Since the current spike on the load during the transient response depends on the PWM parameters, we can also use this method to determine the PWM frequency/rise time range that allows for sufficiently low noise.
Further improvement
After redesign, the last option to continuously improve the filter response is to use RC buffers before and after the filter. This will attenuate the response and compensate for ripple on the output current. Please pay attention to this, because doing so may add another pole to the transfer function of the filter circuit. In addition, the front and rear buffer circuits may require different capacitance values; The output side usually uses a slightly larger capacitor to ensure full reduction of high-frequency ripple. Circuit board assembly and circuit board processing manufacturers explain the switching power supply output filter of circuit board design: design and simulation.
Complete your SMPS schematic
In the above example, we only show the converter part of SMPS, and other important circuit blocks are needed to make SMPS work properly. The other parts required in SMPS depend on the final application and what level of control or precision is required in the system. In the above example, we did not include some other necessary functions:
PWM generation: For a given PWM frequency, to set the output voltage to a specific level, you can use a PWM generator to ensure that the output voltage is the required level. This can be as simple as a VCO circuit, or a dedicated PWM generator IC can be used.
Control loop: Some power topologies, such as LLC resonant converters, will require a large current control loop in which the output of the converter is measured and PWM duty cycle or frequency is adjusted to maintain the voltage at the required level. The operational amplifier with reference voltage is the simplest method for this adjustment, or it can be completed digitally through MCU. You can also use a dedicated controller chip.
User Interface: The system may need some way to accept user input and apply the PWM duty cycle/frequency required to achieve the desired output voltage. The simplest method is the application program implemented on MCU.
Some power controller components will be located in the control loop, measure the output voltage, and adjust the PWM signal according to the settings applied through the digital interface (usually I2C) and implemented by the MCU. Circuit board assembly and circuit board processing manufacturers explain the switching power supply output filter of circuit board design: design and simulation.